Aggregate producers, road builders, and contractors can tell you how important quality, portable screening plants are, but what’s right for one operator may lead to production issues for the next. From small, highly customized design modifications to the overall type and size, there is a multitude of factors to sift through. Below are things to consider when filtering through the facts.
ANALYZE EVERYTHING
It’s important to factor in everything from output capacities to business goals before you buy. First, match the equipment to the operation by determining the ideal production, capacity, and desired number of end-size products.
Make sure you fully understand the company’s sales goals to determine what size screener you’ll need. For example, if an operation can sell 500,000 tons per year, its screeners need to sort nearly 42,000 tons per month. If the screener is in operation 2 days per week (approximately 8 days per month), 10 hours per day, the operation will require a machine capable of screening around 525 tons per hour (TPH). A screener that processes 300 TPH would limit profits and cap growth potential. A machine with a potential output of 900 TPH would come with extra expenses and no added value.
SCALP OR SCREEN
Several main differences separate a scalping plant from a standard screening plant.
Scalping screening plants handle the toughest materials, fed directly onto the screen, but are not as precise as standard screening plants. Scalpers are ideal for sorting materials prior to crushing them, processing scrap metals and recyclables, and extracting rock on construction sites.
Often considered “finishing screens” because of their capability to produce specific sized end products, standard screens typically have two or three screen decks. They are ideal for use in sand and gravel pits, on asphalt jobs, and in quarries.
LIVEHEAD AND TIPPING GRID
Operators can add a livehead or tipping grid to a screener above the hopper for additional sizing. While they perform a similar duty, they are very different. A tipping grid is essentially a hinged grid that blocks larger materials from entering the hopper. This is an affordable option, but can become a chore, particularly in wet or dirty applications where the tipping grid may become plugged frequently.
A livehead is essentially a vibrating screen that attaches to the hopper and is ideal for heavy-duty, dirty, wet, and sticky applications. The unit can be used for two purposes: to scalp dirty material off and eliminate the need for manual cleaning, or to size material going into the machine so operators can produce an additional sized product. While these are generally very efficient, operators should know that screeners with 14-foot hoppers would not be used to the full potential. A typical livehead measures 12 feet, leaving 2 feet of the hopper unusable.
BELT FEEDER VS. APRON FEEDER
A belt feeder is another key element to evaluate, as different products vary in durability. The standard belt feeder is perfect for sand and gravel operations, but is likely to tear or break when working with metal, large rock, or extremely abrasive material. An apron feeder, which is essentially a belt made of metal, is durable and can handle nearly anything an operator throws at it.
SCREEN MEDIA
Operations working with abrasive materials may want to consider stainless steel as an alternative to regular wire mesh. Stainless steel costs nearly twice as much but offers longer wear life.
Additional options are appropriate for some operators. For example, bofar bars, formed of long bars with spaces between, are designed for miscellaneous dirty material. Punch plates, used for heavier applications, are essentially a piece of sheet metal with spaced holes. Finger decks are ideal for reclamation, landfill jobs, or jobs where clogging, blinding, or breakage might be an issue. Finger decks can easily accommodate high-impact loads mixed with recycled waste and debris.
CONVEYORS
Conveyor rollers commonly break under pressure and belts become punctured. As an alternative, some manufacturers offer an impact or sleigh bed conveyor. The impact bed is solid and runs the width of the conveyor to best accommodate the impact of material and prevent belt damage. These conveyors provide additional support and are more durable so they can handle heavy products.
Most discharge conveyors are about 48 inches wide, but the industry offers belts up to 63 inches wide to help prevent clogging. Because the screener is wide and funnels down to the conveyor, machines with smaller conveyors create a bottleneck effect. The material begins blinding in the corners, narrowing the opening. This creates productivity and maintenance problems, forcing operators to shut down and clean it out. Look for a machine that has less—or no—restriction as it transitions onto the discharge belt. A free-flowing machine with a low drop height is the best option to minimize wear and keep productivity elevated.
COUNTDOWN TO THE PURCHASE
Purchasing the wrong screener can cause problems, slow production, and result in revenue losses. Taking time to sift through the facts and separate the good from the bad at the front end will prevent headaches, downtime, and loss of production later. ■
About The Author: Sean Donaghy is the national sales manager at IROCK. He has more than 20 years of crushing and screening experience and has been with IROCK for 8 years. IROCK is a leading manufacturer of portable crushing plants, screening equipment, and other related products. www.irockcrushers.com.
_________________________________________________________________________
Modern Contractor Solutions, August 2015
Did you enjoy this article?
Subscribe to the FREE Digital Edition of Modern Contractor Solutions magazine.
Separating The Good From The Bad
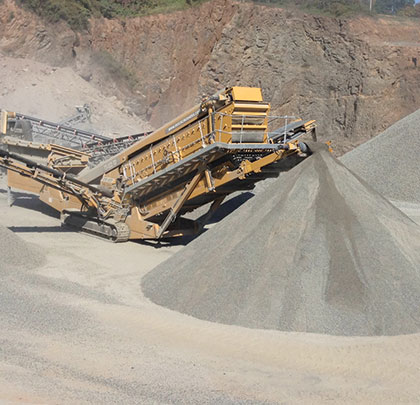