By Jennifer Crisman
When a concrete sealer does not look or perform as expected, the root cause can usually be traced back to issues like overapplication, application in non-ideal conditions, or a buildup of multiple coats. Below are the top five most common concrete sealer issues that are encountered in the construction field, why they occur, and how contractors can avoid and/or fix them.
1. SEALER BUBBLES
The presence of bubbles in concrete sealer is usually a result of a heavy product application. During application of the sealer, outgassing from the concrete surface should be free to quickly move through a thin, wet sealer film. For instance, at a typical coverage rate of 300 square feet per gallon, one coat of an acrylic concrete sealer should be about 5 mils thick when wet. However, when the sealer is dry, it should be only about 2 mils thick. As a point of reference, a sheet of copy paper is 10 mils thick, and a credit card is 120 mils thick. When the sealer is applied too heavily, the air displaced through the surface can’t escape, and it forms a bubble in the sealer surface. To resolve this, two thin coats should be applied, as opposed to one heavy coat.
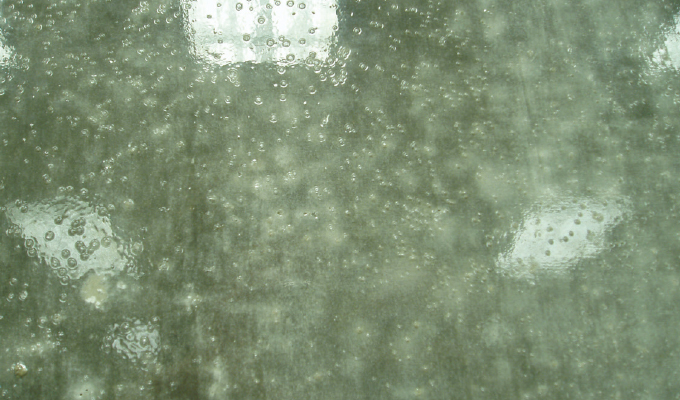
In addition, bubbling of a sealer can also occur if applied in hot weather or if the concrete is exposed to direct sunlight. Under these conditions, the sealer will “skin over” and dry on the surface before all of the solvent has evaporated. As the solvent attempts to evaporate, pressure buildup will form a bubble on the sealer surface. To avoid this issue, it’s best to apply concrete sealers during the coolest part of the day, when concrete is not in direct sunlight.
2. SOLVENT-BASED SEALER TURNS WHITE, PEELS, OR FLAKES
There are two key contributors to “blushing,” or whitening, of a solvent-based concrete sealer. The first is application of the sealer to a wet concrete surface, or to fresh concrete that still contains bleed water. When this occurs, the sealer will not bond to the concrete surface, but will instead float on a trapped film of water. The second cause of sealer blushing is an application that is too thick. Heavy coats of sealer, or a buildup of sealer applied numerous times over the years, will lead to moisture becoming entrapped under the sealer and, in time, the sealer losing adhesion to the concrete. When this occurs, the trapped moisture and air under the de-bonded sealer creates a refractive index—in turn making the sealer appear white to the human eye and, eventually, peel or flake off the surface.
To avoid this problem, be sure to carefully follow the manufacturer’s recommendations regarding coverage rate and the number of suggested coats. In addition, concrete should not be resealed until the previous coat(s) has worn away or been stripped off. Afterward, use a solvent wash and allow to fully dry.
3. WATER-BASED SEALER IS WHITE OR POWDERY
The drying process of water-based sealers is quite complicated and significantly affected by the temperature and humidity of the environment during application. Water-based, acrylic sealers dry by a process called “coalescence,” during which the water and then the coalescing solvent evaporate so the acrylic particles fuse together to form the sealer film. If the temperature during application is too low or humidity is too high, the coalescing solvent will evaporate prior to the water, and the sealer will dry white or powdery as a result of the latex particles not fusing together before drying. As a best practice, always be sure to identify required temperature and humidity conditions for the successful application of a water-based sealer.
To resolve this issue, pressure wash or scrub the concrete to remove any loose debris, before allowing the sealer to completely dry. Next, perform a solvent wash to bring remaining product back to the surface and to reestablish the seal. If a solvent wash does not provide the gloss and seal desired, apply a very light coat of sealer after the solvent wash has dried. Concrete cure and seal solutions typically last 1-3 years, so some peeling and flaking should be expected as the product wears away—particularly in areas of high traffic or direct sunlight. When working with solvents, be sure to carefully follow the instructions and safety precautions outlined in the product data sheet and SDS.
4. SEALER IS STAINED FROM WEAR AND TEAR
Over time, it’s not uncommon for concrete sealers to become stained from general wear and tear resulting from repeated or prolonged exposure to oil, tire treads, fertilizer, and other debris. The most common concrete sealers are manufactured with acrylic polymers that do not provide exceptional chemical or stain resistance for the concrete.
In order to maximize durability and stain resistance, consider using an epoxy or urethane coating system, and ensure that the coating is appropriate for exterior use before applying to concrete in an outdoor environment.
5. CONCRETE IS DARK AND/OR BLOTCHY AFTER SEALER APPLICATION
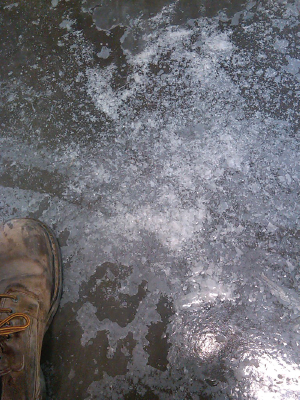
Most acrylic sealers will darken concrete and leave a glossy shine to some extent, giving the concrete a “wet” appearance. Because every slab is unique in its color and texture, the color of the concrete after sealer application can be difficult to predict. A variety of factors—such as mix design, use of chemical admixtures, finishing techniques, or porosity—can have an impact on concrete surface color.
Using a sealer will deepen the true color of concrete and highlight disparities in the surface texture that result from floating and finishing. In addition, sealers bring out the “grain” in concrete, just like a varnish does on wood. If changing the concrete color after sealing is a concern, it’s recommended to use a penetrating, water-repellent sealer, or to perform a small test application of a film-forming sealer to ensure the result is acceptable before addressing the entire area.
CLOSING THOUGHT
Throughout the course of its lifetime, concrete suffers many different forms of damage. Though concrete sealers add a protective layer to concrete floors and structures to help maximize their durability and minimize moisture permeability, common issues associated with sealing concrete can be a source of frustration. Knowing these five common issues will be beneficial for application success.
About the author:
Jennifer Crisman is director of marketing services at The Euclid Chemical Company, a leading manufacturer of specialty concrete and masonry construction solutions. For more, visit www.euclidchemical.com.
Modern Contractor Solutions, June 2020
Did you enjoy this article?
Subscribe to the FREE Digital Edition of Modern Contractor Solutions magazine.
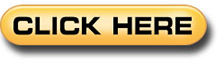