Process additive turns scrap tires into modern material for durable roads
Vehicle tires of course belong on the road, but for the last two decades, they have also increasingly found their way into the road. That is made possible by recycled scrap tires and VESTENAMER®, a process aid manufactured by Evonik Industries for the rubber and construction sector.
INNOVATION FOR ROADS
Road quality and durability are key concerns for the public sector. The clearly emerging demand for high-performance road construction materials to avoid ruts and cracks—and to save maintenance costs—is increasingly moving into public awareness. At the same time, raw material costs for asphalt, and specifically for asphalt modification compounds, have increased considerably, creating another obstacle to cost-effective road construction. Obviously, there is a need for alternative concepts.
Evonik is pursuing a sustainable and cost-effective approach to road construction. VESTENAMER, the specialty chemical company’s process additive for the rubber industry, makes it feasible to process rubber powder from scrap tires to generate asphalt with rubber content. The recycled material is mixed into road construction bitumen or asphalt to improve the quality of the mixtures and to extend the service life of road surfaces.
EXTENDED SERVICE LIFE
In the United States, asphalt mixtures containing rubber have been used for decades. Long-term studies have demonstrated a significant improvement in road durability. “The market for elastomer-modified, i.e., rubber-containing, road surfaces has been growing in Europe over the past years as well,” says Frank Lindner, senior business manager for VESTENAMER. “The positive properties are obvious since the material significantly reduces cracking, ruts, and potholes in the road surface, which in turn extends road service life.”
Another sensory experience also speaks in favor of using rubber-modified bitumen: The rubber powder is frequently used in porous asphalt—also known as low-noise asphalt—that cuts down on traffic noise. Scientific studies have documented that using larger shares of rubber powder in road surfaces can result in a noise reduction of one to two decibels. This is highly significant because in human perception, a reduction by 3 dB is comparable to cutting the traffic volume in half.
EFFICIENT USE OF SCRAP TIRES
Every year, a waste volume of some 19.3 million metric tons of scrap tires is generated worldwide—including over 3.6 million metric tons in Europe alone. Twenty years ago, over half of all scrap tires were incinerated to generate energy in Germany alone, while only every tenth scrap tire was processed into granulate. By now, the volume of the latter has caught up with energy-related processing.
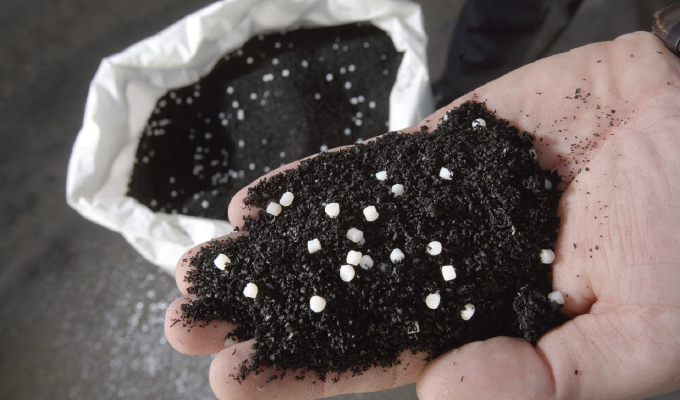
Recycling scrap tires definitely makes environmental sense. “Reusing recycled tires secures valuable resources,” says Thomas Engenhorst, sustainability strategy manager in the Resource Efficiency Segment of Evonik. “Tires are not classified as waste, but are considered a valuable material, which may not, for example, be disposed of in landfills. This use eliminates the disposal question: Instead of incinerating the tires, they have another life stage in road traffic—not as part of an engine-powered vehicle, but in the form of an elastomer or rubber powder in the road surface.”
As part of a test track in the German town of Paderborn, the local road Detmolder Strasse was resurfaced in 2012 in compliance with the objectives of the EU Waste Directive. Fifty percent of the new asphalt mixture consisted of milled material—asphalt granulate—from the old road. The new mixture formulation also included rubber powder and VESTENAMER. For every 100 meters of track, some 80 scrap tires were turned into an elastomer-modified road surface, along with recycling the old asphalt.
FEWER CO2 EMISSIONS
A study by the renowned Institute for Energy and Environmental Research in Heidelberg provides further information about the ecobalance: Each metric ton of recycled rubber powder saves some 2.7 metric tons of carbon dioxide, which would otherwise be generated during the incineration process. Accordingly, this material use significantly optimizes the carbon footprint.
The application of VESTENAMER is a clean affair in many respects: The emissions of volatile and semi-volatile compounds, including hydrocarbons and sulfur compounds, are much lower in road surfaces containing rubber than in conventional, polymer-modified asphalt types.
Furthermore, Evonik’s process additive reduces the migration of organic compounds that are washed out by rain and reach the groundwater. As a study conducted by FABES Forschungs-GmbH on behalf of Evonik has documented, the use of VESTENAMER reduces the overall groundwater burden.
PROCESSING AID FROM THE 70S
VESTENAMER was developed in the late 1970s as a processing aid for the rubber industry. Polyoctenamer, which is produced in the Marl Chemical Park, resolves a number of challenges associated with compounding and processing rubber. It is used to this day because of its positive characteristics in the interaction with other rubbers. In addition to the tire market, the product plays a part in the manufacture of rubber items such as hoses, clutch linings, roller coatings, or molded parts. Since road transportation authorities have long been looking for an improved and more durable material, the High Performance Polymers Business Line of Evonik began to conduct extensive research in this area 10 years ago. Since then, VESTENAMER has gradually become the unifying element of choice in rubber-modified asphalt.
For more information:
Evonik is one of the world leaders in specialty chemicals. Evonik is active in more than 100 countries around the world with more than 36,000 employees. For more information about the products for use in the construction industry, visit www.evonik.com.
Modern Contractor Solutions, February 2019
Did you enjoy this article?
Subscribe to the FREE Digital Edition of Modern Contractor Solutions magazine.
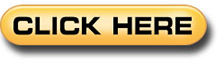