How caring properly for mobile elevated work platforms pays off over time
By Rafael Nuñez and William Dovey
When contractors need to work for extended periods of time in high, hard-to-reach places, they turn to mobile elevated work platforms, or MEWPs. Over the years, two of the most popular MEWPs—scissor lifts and boom lifts—have earned reputations for being invaluable on jobsites worldwide.
Scissor lifts are uniquely suited for jobs that require vertical ascent and descent. When contractors need to access high places but there is an obstacle in the way, or they’re working at even higher elevations, boom lifts are the best choice. Like scissor lifts, boom lifts are also most commonly used for construction and maintenance tasks. However, boom lifts are supported by a hydraulically-actuated arm that can maneuver around obstacles and extend to higher elevations.
While scissor lifts and boom lifts have their similarities and their differences, both machines are available in different models based on the work environment in which they’ll be used. There are rough-terrain scissor lifts that go on all types of outdoor jobsites, as well as “slab” scissor lifts that are intended for operation on flat, level surfaces. The same goes for boom lifts.
Some boom lifts are built for the rough terrain commonly found on construction sites and powered by diesel, gas, or propane. Others are battery-powered, electric slab models that work well on smoother, less rugged surfaces.
DAILY INSPECTIONS
Like all heavy equipment, scissor and boom lifts require periodic maintenance and inspections to ensure equipment is running efficiently, helping operators maintain productivity. Scissor lifts and boom lifts should be inspected before use every day, at shift changes, and any time a new operator takes over the machine. A machine’s typical working environment also has an impact on how often it should be inspected.
Inspections are the most significant element of maintaining a scissor or boom lift. Inspections should occur more frequently if operators are using their machines over multiple shifts every day, or if they are using them in a hostile environment, like those where welding or sandblasting are occurring. Making sure a machine is in good working condition before operating it will make it far less likely to experience any type of problem or failure—a must for operator safety.
Inspection points will vary based on machine type, so it’s important that operators and owners refer to their machines’ service manuals to determine exactly what to check. However, during the daily pre-start inspection, users should always check machines for any visible leakages (oil, fuel, or battery fluid) or foreign objects. They should also keep an eye out for dents, weld or parent metal cracks, or other damage. The machine’s decals and placards should be clean and legible.
A walkaround inspection of the machine is primarily a series of visual checks. The checkpoints in this inspection will vary slightly depending on the machine type (scissor or boom lift) and its powertrain (combustion or electric). On JLG’s 430LRT combustion-engine-powered scissor lift, for example, the daily walkaround inspection includes 24 different checkpoints, including the machine’s scissor arms, centering link, and sliding wear pads. Meanwhile, the company’s E450A electric-powered boom lift has 16 different daily checkpoints, including its boom sections, uprights, and the turntable that allows the boom to swing 360 degrees.
On boom lifts, the turntable bearing needs to be greased; JLG has integrated greaseless bushings in most of the pins.
After completing the walkaround inspection, operators should check the machine’s battery, add fuel, if necessary (combustion engines only), and add water to the battery (electric models only).
Operators should then check hydraulic oil levels and ensure the hydraulic system is clean—the most important factor for ensuring the machine’s system stays in top working condition. Nearly all MEWPs have hydraulic systems, and keeping those systems as clean as possible is key for a longer, more productive machine life. Operators and maintenance technicians should even clean the area around the filter before they change the filter to avoid possibly contaminating the hydraulic system. They should also always use the hydraulic oil type recommended by the machine’s manufacturer, keeping the reservoir clean and full.
Next, operators should perform a function check of all systems in an area free of overhead and ground-level obstructions. Any accessories or attachments should also be examined before operating the machine. This includes ensuring the machine’s platform gate latches properly and looking under the machine’s chassis to check for conditions like loose or missing parts that could cause extensive machine damage during operation.
A machine that displays issues during the inspection should never be operated. The scissor or boom lift should be shut down, red-tagged, and repaired at the earliest opportunity.
MAINTENANCE MUSTS
While daily inspections and walkarounds are imperative, scissor lifts and boom lifts also require other regular inspections based on the number of hours they’ve been in operation. A qualified equipment mechanic should inspect the machines every 3 months or 150 hours, whichever comes first. Machines that have been out of service for more than 3 months or purchased used should also be inspected prior to use.
The machine’s service manual should include a preventive maintenance schedule specific to each machine, including proper servicing and maintenance procedures for the various parts of the machine. Inspection frequency should increase if the working environment is harsh or the severity and frequency of use changes.
Most manufacturers recommend scissor and boom lifts be inspected annually (at least every 13 months). Often, manufacturers recommend this task be performed by a factory-trained service technician with extensive knowledge of that manufacturer’s equipment.
Residual benefits
Scissor and boom lifts that have been well maintained over their lifetime can often end up in a manufacturer’s remanufacturing or reconditioning program. For example, JLG’s reconditioning program closely inspects each machine, makes any necessary updates and repairs, gives them new paint jobs and performs other cosmetic upgrades until machines are in like-new condition. After another thorough inspection, these machines can continue performing out in the field, with the potential to rack up thousands of additional service hours.
When it comes to scissor and boom lift maintenance, don’t be “penny wise” and “dollar foolish.” Do the proper inspections and maintenance to keep the machine in perfect operating condition, and it will reward you with higher productivity, lower cost of ownership, and higher value at resale.
About the authors
Rafael Nuñezis a senior product manager for scissors and vertical lifts, JLG Industries, Inc.; and William Dovey is a senior product manager, JLG Industries, Inc. For more information about JLG equipment, visit www.jlg.com
Modern Contractor Solutions, June 2019
Did you enjoy this article?
Subscribe to the FREE Digital Edition of Modern Contractor Solutions magazine.
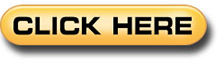