In the business of improving infrastructure, work occurs in high-risk environments where fall hazards are common. In fact, falls have been the leading cause of fatalities within the construction industry for the past decade. According to US Bureau of Labor Statistics, in 2020, more than 1 in 5 workplace deaths occurred in the construction industry, with falls accounting for more than one-third of those fatalities. While OSHA recognizes that falls are typically complex incidents involving various factors, one of the leading causes is faulty or improperly used safety equipment.
MAKE SAFETY A KEY PILLAR
A robust safety program is critical for the health and wellbeing of crews on jobsites. It should include regular training to ensure personnel is up to date on the most current industry practices, a written safety plan that is accessible to all employees, an on-site communication system, and effective safety equipment that meets industry guidelines. For example, OSHA requires fall protection systems be provided at elevations of 6 feet and higher in all construction areas.
But even the most effective safety measures and the best training can go awry if people fail to consistently follow-through with protocols. If workers haven’t had issues before, it’s easy to gain a sense of overconfidence and let guards down. And if safety equipment meets industry standards and has performed properly in the past, it’s easy to fall into the trap of depending on it explicitly. So, while it’s important to be confident in the measures at hand, it’s imperative to remain diligent in safety practices and ensure all safety equipment is good to go.
CHECK AND DOUBLE-CHECK
Just as employees must keep up with industry certifications and training, all fall protection equipment should be rigorously inspected prior to each use. Check to ensure the equipment is set up appropriately and performing as it should be and be diligent in looking for any new wear and tear that could impair the equipment’s efficacy. Incorporate these checks into your jobsite morning routine, so they are never overlooked. If issues arise or if inspection reveals that the equipment no longer serves its function due to damage or wear, the equipment should be taken out of service and replaced immediately. Additionally, with each review, an OSHA and ANSI checklist should be at hand to ensure that equipment is in peak condition and continues to meet industry standards.
DON’T BE AFRAID TO INNOVATE
When it comes to safety equipment, don’t be afraid to make enhancements. The most effective safety equipment will not only meet industry standards and keep crews safe from workplace hazards, but also aid in productivity. And “what has always been done,” should never be accepted as an answer for equipment reliance.
For example, when GeoStabilization International was reevaluating its fall protection perimeter system, the team wanted to know if a better system was possible. Specifically, the team wanted to determine if they could further enhance safety for crew members while increasing jobsite efficiencies—partnering with the Colorado School of Mines to investigate. As part of the engineering program’s capstone project, GeoStabilization tasked student teams to design a perimeter protection system to be used on future remote-site construction projects where fall hazards are common. The system needed to be lightweight, easy to install, durable, and meet OSHA, ANSI, and CSA standards. The goal was for the new system to improve performance in all four of these areas compared to the current system.
Working closely with the GeoStabilization safety team, the student groups took the list of needs and wants and explored a multitude of outside-the-box options to understand the limitations and possibilities of the safety systems. The teams utilized cable lines, strap lines, cargo nets, and stand-alone steep gate systems in the designs presented to GeoStabilization. After a preliminary design review, GeoStabilization incorporated components from multiple concepts to create a final version.
Next, they performed an engineering analysis of the system to ensure its reliability and safety factors. The project’s final phase consisted of creating a 90 ft functional prototype and testing the system over 2 days. Testing is a critical component in determining the system’s reliability, functionality, and safety. And in this instance, it determined that the new system met the company’s goals and has since become the team’s new perimeter system for providing fall protection in remote-site areas. The system is essential to keeping crews safe on jobsites.
CLOSING THOUGHT
While falls are currently the leading cause of injury and death in the construction industry, it doesn’t have to be that way. Repairing critical infrastructure will always come with risks, but a robust safety program will significantly decrease safety incidents. The most successful crews will not only meet industry safety standards but also understand each jobsite’s intricacies, stay up to date on current industry practices and regularly inspect all equipment. And when necessary, they’ll invest in new and innovative safety systems.
About the Author:
Josh Monroe is the vice president of health, safety and risk management at GeoStabilization International. He leads the safety program for all activities throughout the United States and Canada. For more, visit www.geostabilization.com.
Modern Contractor Solutions, February 2023
Did you enjoy this article?
Subscribe to the FREE Digital Edition of Modern Contractor Solutions magazine.
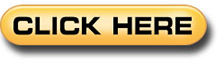