By George Cesarini
Despite advances in technology, fall safety on construction sites continues to be a concern. In 2017 alone, the construction industry suffered more fatalities than any other industry, as evaluated by the Bureau of Labor Statistics. Of the 971 construction fatalities that year, nearly 40 percent were fall-related. In order to reverse this trend, project managers, contractors, and workers alike must recognize their role in mitigating risk at every stage of the construction process. Here are some risk mitigation tips to keep in mind before, during, and after a job is completed.
MITIGATING RISK PROACTIVELY
No matter the size, all construction projects should begin with a Job Hazard Analysis (JHA). JHAs can help anticipate potential exposures, whether fall-related or otherwise. When performing JHAs, safety managers should:
- Develop an overview of the project at hand
- Identify the tasks needed to complete the project
- Make note of any equipment needed to perform these tasks
- Record potential exposures that could result from these tasks
- Establish the measures that will be implemented to mitigate foreseeable risks
If project conditions shift or subsequent work extends beyond the length of a single day, the JHA should be reviewed and/or adjusted as needed.
Mitigating risk requires collaboration among all parties involved. Once the JHA is complete, it is critical for leaders to review findings and the resulting safety procedures with contractors and employees so everyone is well-equipped to comply with safety practices. Leaders should also account for language barriers, as applicable, and provide information in manners accessible to, and understood by, all workers.
SAFE JOBSITE PRACTICES
Identifying risks is only the start of creating a safe worksite. Following this step, the project management team must ensure all safety procedures are executed as planned. Certain technologies can help make sure everyone abides by safety procedures during construction.
For example, commercial small drones, or Unmanned Aircraft Systems (UAS), can offer safety managers and supervisors the ability to review and assess otherwise dangerous environments (e.g., heights or secluded environments) from a safe place, and help perform certain tasks such as:
- Inspecting the construction site
- Complying with safety procedures
- Monitoring construction progress
- Securing evidence for accident investigations
- Security surveillance
- Quality assurance and control
Other safety devices—many of which are relatively new to the market and have limited adoption to-date—can also help keep workers protected on the job. Wearable sensors embedded in clothing, including hard hats, vests, and glasses, can alert workers to potential safety exposures. Similarly, certain devices worn on workers’ wrists can help measure fluctuations in heart rate and body temperature, and can even alert coworkers or medics to dangerous physical conditions.
Additionally, leading edge protection such as guardrail systems should be put in place, as required. Organizations should implement a permit system that only allows controlling contractors (or other qualified individuals) to remove leading edge protection from a site, when appropriate.
Personal Fall Arrest Systems (PFAS) are also extremely important in reducing falls and creating a safe construction site. According to OSHA, the type of PFAS used should match the conditions of the relevant construction site. Hot or cold environments, as well as factors such as the presence of acids, moisture, oil, grease, etc. can influence which system is appropriate for a given location. Regardless of which PFAS is selected, these devices should be inspected before use, and workers should receive training on how to use them properly.
Even as technology begins to play a larger role in mitigating risk on a construction site, field supervision remains key when it comes to protecting workers and mitigating risks on the jobsite. This way, managers can ensure that all workers fully understand, and are compliant with, safety policies.
Proper training is critical to safety as well. Managers should never assume that their workers—no matter their skill or experience level—are ready to begin work without instruction or at least a refresh on proper techniques. Managers should check-in with their employees to make sure they know how to operate relevant machinery and that they are aware of potential fall hazards specific to the project site. To this end, education around the selection, set up and utilization of equipment like ladders and scaffolding must be incorporated into any construction project’s fall management plan.
SAFETY CULTURE
Safety is so much more than a series of suggestions applied to a construction project. Safety is a culture that must be instilled, valued, and promoted. Managers should foster a company culture in which employees feel comfortable raising safety issues that need to be addressed. For example, if workers identify an exposure and feel as though they have not been adequately protected against it, they should be empowered to let their managers know.
Similarly, it is crucial that all workers comply with safety policies put in place by management, when it comes to individual projects as well as at an organizational level. It is a situation in which everybody wins: safety-conscious managers lead to safer employees and safer businesses. In turn, safer businesses tend to see higher growth and fewer losses while attracting more clients and insurers.
CLOSING THOUGHT
Safety is everyone’s responsibility, and contractors, managers, and workers must do everything in their power to prevent falls and mitigate other risks at each stage of the construction process.
This document is advisory in nature and is offered as a resource to be used together with your professional insurance advisors in maintaining a loss prevention program. It is an overview only, and is not intended as a substitute for consultation with your insurance broker, or for legal, engineering, or other professional advice.
About the author
George Cesarini is a senior vice president for Chubb Construction Major Markets. He is responsible for managing the risk engineering services provided across the country to construction clients, ensuring quality and value-added services are being delivered to assist them in their efforts to enhance their safety culture and mitigate potential exposures on their project sites.
Modern Contractor Solutions, December 2019
Did you enjoy this article?
Subscribe to the FREE Digital Edition of Modern Contractor Solutions magazine.
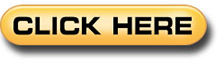