With projects in high gear, transporting equipment from jobsite to jobsite needs to be done efficiently, effectively, and safely. GC’s need to know the right trailer to use and how best to secure the load. Here’s insight from Troy Geiser, vice president of sales and marketing with Talbert Manufacturing.
MCS: Safe heavy-haul loading starts with selecting an appropriate trailer for the intended equipment. How do operators spec a heavy haul trailer?
GEISLER: Trailer capacity should be an operator’s first concern in spec’ing a trailer. Start by figuring out the total weight of the haul, including all equipment and attachments.
With this number in mind, it’s time to compare trailer capacities since not all 55-ton lowboys are created equal. While they might all be capable of hauling 55-tons, some will need the entire deck length to haul that weight safely. Others might only need half the deck length for the same weight. Since loads are rarely uniform, having a trailer rated in half deck capacity gives operators a more realistic indication of what the trailer will be able to handle without structural failure.
Bigger doesn’t necessarily mean better when it comes to hauling. Using a trailer with a much higher capacity than the intended load can also lead to complications. For example, using a 55-ton trailer for a 35-ton haul can work, but the light load might mean the trailer has a higher deck height than when it is fully loaded. This could require an operator to alter the intended route if the higher load can’t fit under overhead obstacles. It may also result in a load that is considered oversized. In the U.S., generally, this is anything over 13 ft, 6 inches tall; 8 ft, 6 inches wide; 48 ft long; and more than 80,000 lbs gross weight (including truck, trailer, and payload). If a load exceeds in one of these areas, it may require a permit.
Working with knowledgeable dealers and manufacturers can provide a trailer that not only has the necessary capacity, but one that limits permit costs when hauling oversize equipment. Telescopic trailers—trailers with dual kingpin settings that can be operated empty without a permit in states with a 43-ft kingpin law—as well as flip up and removable axle attachments are just a few examples of versatile designs available from select manufacturers.
Additionally, some equipment will require special considerations. For example, when hauling paving or low-clearance equipment, selecting a trailer with a low load angle is important for safe loading. When hauling an excavator, operators need to consider where the boom will sit on the trailer and how it will be cradled. A low position of the boom is critical for keeping the load within height restrictions. Some top-tier manufacturers offer customizations such as a rear bridge design that eliminates interference with boom placement and makes transportation safer and easier.
Taking these things into account—capacity, load concentration, permits, and special equipment considerations—operators can spec the right trailer for the haul.
MCS: Once an appropriate trailer is selected, are there any general tips operators can use to ensure safe, smooth loading?
GEISLER: When it’s time to start loading or unloading equipment, the first thing to do is make sure there is plenty of room to operate the equipment, trailer, and tractor safely. This can be challenging on crowded jobsites, but taking shortcuts like side loading are highly dangerous and strongly discouraged. Side loading, aside from increasing the risk of tipping equipment, can also cause premature damage to the trailer, decreasing overall efficiency.
There should be enough space around the equipment and trailer to provide a clear line of sight to the operator in the machine. A spotter is recommended, especially when loading equipment with restricted lines of sight directly in front of their tracks or tires.
It goes without saying that familiarity with the equipment being loaded, as well as the trailer, makes for a smoother, safer operation. Arrange for a qualified individual to be on hand, whether they are from in-house or a member of the site crew.
As equipment maneuvers onto the trailer, there are a couple safety considerations to keep in mind. First, a smooth transition from surface to surface is imperative. Any bumps between the ground and the deck or the deck and the rear bridge can make loading more difficult and dangerous since it forces equipment operators to increase power to clear the obstacle.
Operators should also be aware of a particular trailer’s breaking point and use caution when loading and unloading to minimize lifting axles off the ground. The magnified stress on the axles as the trailer comes back down can cause damage and premature wear. Quality trailers with high safety ratings offer some advantage here. The safety rating is an indicator of how much stress a trailer can safely handle. It encompasses factors such as the strength of the raw materials used in the trailer’s construction and how the beams and cross members are configured. A trailer with a safety margin of 2.5 to 1 is designed to better handle momentary increases in payload, even those that occur during loading and unloading.
Once the equipment is safely loaded, a thorough pre-trip inspection is recommended. Ensure the load is secured with well-maintained, properly rated equipment. Inspect chains, binders, straps, or other tie downs, looking for cracks, fraying, weak links or other signs of wear that might require replacement. A visual inspection of the trailer is also recommended to ensure no damage has occurred during loading. Issues that weren’t apparent when the trailer was empty might also be evident at this point, so be sure to check the trailer body and systems. This includes breaks, tires, suspension, electrical and cylinders, as well as the deck, gooseneck and other components.
Next, ensure tires are properly inflated to the right psi. Finally, a discussion on safe loading practices would be remiss if it didn’t mention overloading. This practice is highly discouraged by trailer manufacturers. A single overload might not cause the trailer to fail, but it is another unsafe shortcut that puts the operator and public at risk. It puts unnecessary stress on the trailer components, increasing the likelihood of future failure.
MCS: Austin Talbert pioneered the removable gooseneck for safer heavy-haul loading and it has since become an industry standard. How does this design improve loading safety?
GEISLER: A construction boom in the 1930s resulted in huge changes to the industry, specifically in the size of equipment that now needed to be moved quickly and efficiently from one job to the next. At the time, loading excavators, cranes trenchers and other heavy equipment required several people per job using planks and blocks to hoist equipment up and over the tires and axles, before easing it back down onto the trailer bed. This was cumbersome, and the risk of potential injury and equipment damage was high. Fatal accidents were common. During that time, Austin Talbert was hauling large equipment for local contractors, and was determined to find a safter solution for his crew and his customers.
In 1938 he introduced the first-ever 60-ton fixed gooseneck trailer with removable rear suspension that allowed users to remove the rear axles, set the trailer’s back end on the ground, and maneuver equipment onto the deck of the trailer without having to hoist it over the tires and axles. The fixed gooseneck trailer saved time and lives. Even so, equipment continued to get taller, longer, wider and heavier, so in 1947 Talbert patented the removable gooseneck to safely load even larger machines. This feature eliminated the need to use wood block ramps to drive and lift equipment up and over the axles, forever changing the heavy-haul industry. Removable goosenecks save users substantial time, hassle and cost, meaning contractors can be more productive and profitable. What used to take hours to load and off load can now be done in a matter of minutes with a removable gooseneck.
Today, the majority of heavy-haul trailers feature a removable gooseneck. It’s simply the safest, most efficient way to load large equipment. Unlike rear loading trailers that employ long ramps to achieve a reasonable load angle, removable goosenecks only need short ramps to provide an acceptable approach. This eliminates the need to raise and lower heavy ramps, often by hand, which can lead to injury. It also means operators driving equipment onto the trailer ever lose sight of deck in front of them, reducing the risk of tipping or driving equipment off the ramps. Since equipment doesn’t have to go up and over the rear axle, there is less strain on this component as well, which can lead to a longer service life.
CLOSING THOUGHT
When hauling an excavator, operators need to consider where the boom will sit on the trailer and how it will be cradled. A low position of the boom is critical for keeping the load within height restrictions.
About the Author:
Troy Geisler is the vice president of sales and marketing for Talbert Manufacturing. He has more than 15 years of experience in trailer sales, including more than 5 years with Talbert. For more, visit www.talbertmfg.com.
Modern Contractor Solutions, August 2021
Did you enjoy this article?
Subscribe to the FREE Digital Edition of Modern Contractor Solutions magazine.
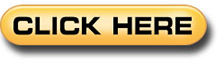