how to ensure clean, quality diesel exhaust fluid
By John Cleary
There’s no denying that Tier IV regulations have begun to impact the equipment industry. As new Tier IV-compliant equipment rolls into equipment fleets, it’s important to consider how the strategies engine manufacturers use to meet Tier IV emission requirements impact the needs of customers on the jobsite.
Tier IV engines and their requirement of diesel exhaust fluid (DEF) present their own set of challenges. The risk of contamination and fluid freezing are concerns presented to both rental branches and contractors. But there are ways to combat these issues, and with the right storage solutions, contractors can find safe and efficient options.
ENSURING THE FLEET IS READY
The first way new DEF requirements affect contractors is right on the yard in prepping equipment to be ready. With an already long checklist of maintenance and prep tasks for equipment use, ensuring DEF tanks are filled before that gear is ready to go adds one more box to check. Currently, many contractors are purchasing their DEF in cardboard boxes filled with 2 1/2-gallon jugs. The boxes are stored inside, and jugs are manually hauled and poured into the appropriate equipment. Because DEF is very sensitive to contaminants, this process presents many hazards and opportunity for contamination.
As the number of Tier IV units on the yard grows and the need for DEF expands, contractors are looking for safer and more efficient ways to handle the DEF challenges on their yard. Already familiar with incorporating larger stationary fuel tanks at the branch for fueling needs, many contractors have looked for similar solutions for DEF—storage tanks that can sit next to their fuel tanks and seamlessly integrate into their fleet.
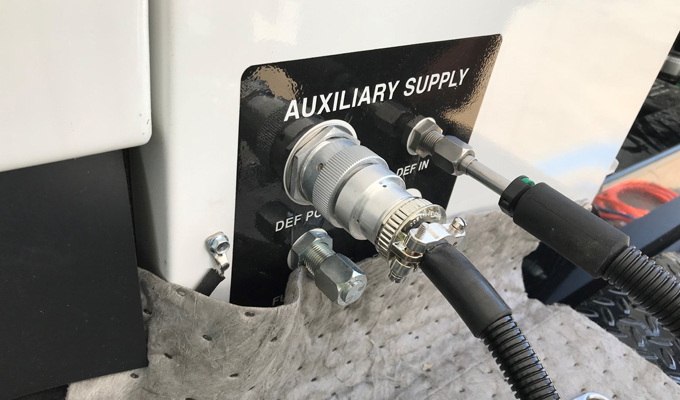
DEF storage tanks diminish the risk of contamination by providing a sealed connection for filling the tank and a faster method for transferring the fluid to equipment tanks. With a specially designed dispensing system to fill the fluid in the equipment’s tank, operators decrease the chance for contamination of product. It also eliminates the opportunity for contaminants to be picked up on the boxes during storage or on the cap of the jug. Bulk fuel and fluid distributors deliver quality fluid to the customer and are equipped with specialty connectors to ensure no contamination enters the fluid in the transfer process. The distributor also ensures the fluid is always supplied without the service manager having to consistently track and buy boxes or jugs of material.
To further decrease the chance of contamination, crews must be trained on the contamination issues and how to limit exposure to contaminants. This should include making sure the cover of the equipment tank is clean before opening and avoiding filling the tank in windy, dusty conditions. Even the smallest particles can damage the entire tank of fluid.
Contamination isn’t the only concern. DEF is also sensitive to cold temperatures and susceptible to freezing at 12-degrees Fahrenheit (-11 Celsius). Although freezing won’t destroy the chemical composition of the fluid, it will render it useless until it thaws out, which could have devastating effects on equipment utilization and customer relations. DEF storage and pumping solutions offer optional heating systems to ensure the fluid is always at ideal operating temperatures.
Tank options on the market range from 400 gallons to 1300 gallons, allowing contractors to choose a tank size to match their fleet. Estimating the exact need can be difficult and requires careful consideration not just of the fleet today, but of expected changes in the fleet over the next three to five years. By understanding the size of the fleet with DEF requirements, the additional plans for equipment acquisition and a general understanding of the overall utilization of this equipment, contractors can evaluate and decide on the tank size that best matches their needs.
The challenges of DEF extend beyond preparing the fleet to be ready for action. As full-service solution providers, many contractors are looking to provide DEF solutions on the jobsite, especially in remote, continuous-run applications.
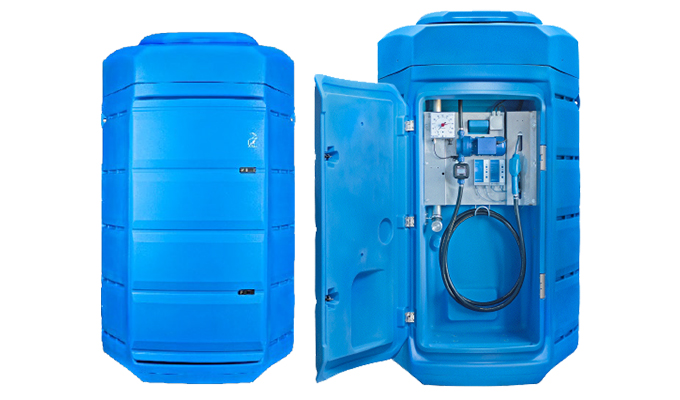
ADDING AUXILIARY DEF STORAGE
More equipment with DEF requirements in the fleet means more DEF requirements on the jobsite. This is especially true in applications with continuous run-requirements, like generators, pumps, compressors and heaters.
Portable fuel tanks have long been a profitable and necessary accompaniment to generator usage—especially in remote locations. But the simplicity of integration and operation of fuel storage tanks does not hold true for DEF solutions. With auxiliary fueling solutions, the engine draws fuel directly from the auxiliary fuel tank, completely bypassing the onboard fuel tank. With DEF, the engine always consumes the fluid via its own onboard tank, which is then continually refilled by the auxiliary DEF storage tank. This requires communication between the equipment being refilled and the auxiliary DEF storage tank, resulting in the need for a control system integrated into the generator, pump, compressor, etc.
Working to meet the needs of customers, rental branches and contractors have been instrumental in bringing generator and tank manufacturers together to develop and standardize connection panels and control systems to provide an easy and seamless integration system. The design incorporates sensors in the generator to trigger the auxiliary DEF tank when the equipment’s onboard tank reaches low level. The auxiliary DEF tank’s pump then kicks in to refill the generator’s onboard tank until the set capacity is reached, at which point the equipment’s sensors trigger the pump to turn off. This fully contained filling system also prevents contamination of the fluid.
Because of the 2 to 3 percent consumption rate of DEF to fuel, a 100-gallon DEF tank often provides plenty of supply for a continuous-run generator, extending the fill time to weekly, which matches the fueling requirements.
Currently, there are standardized connections and control systems on Generac, Cummins, and Doosan generators. Western Global, a manufacturer of fuel and fluid storage solutions, engineered a DEF tank, the TransCube DEF, designed around that standardization providing a simple solution for extended-run operations.
CLOSING THOUGHT
The future impact of EPA emissions regulations or even the long-term outlook for DEF systems is unknown, but contractors are faced with finding solutions to serve customers in today’s working environment. Systems do exist to seamlessly integrate both on the yard and on the jobsite and a few simple considerations make tackling this challenge relatively easy.
about the author:
John Cleary is vice president of sales & distribution development with Western Global. For more, visit www.western-global.com.
Modern Contractor Solutions, February 2020
Did you enjoy this article?
Subscribe to the FREE Digital Edition of Modern Contractor Solutions magazine.
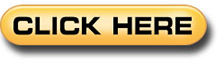