Rope access experts use ropes to safely and efficiently descend, ascend, and perform project tasks on otherwise unreachable jobsites. It’s become a common practice in limited-access areas and at extreme heights—such as in slope stabilization and rockfall mitigation where scaffolding or aerial platforms are not plausible. Rope access, however, is not without risk and not for the unprepared. A detailed safety plan, that includes a site overview, an equipment checklist, training background, and understanding of site hazards, is important before accessing ropes.
EVALUATE AND ASSESS
Understanding the variables of a jobsite allows for a thorough plan that outlines the scope of the work and the best way to undertake the job to ensure any risks to health and safety of the team—and others—are minimized.
In geohazard mitigation work, a proper site evaluation should include a comprehensive slope assessment that outlines both current and potential hazards. It should also note if there are any safety measures required to begin mitigation work—such as scaling to remove loose rocks—and what areas will need to be accessed throughout the process. This will enable the engineering team to create proper mitigation and construction plans, detailing the exact work needed, the equipment that will be necessary for success, and the expertise needed to compose the crew.
TEAM TRAINING, COMPOSITION
Building the best team for the job is the goal for companies across industries. When it comes to rope access work the best team doesn’t just mean the most knowledgeable it requires a team that is appropriately trained, industry certified, and keenly aware.
Crews should follow an industry certification. An example of industry certification is the SPRAT (Society of Professional Rope Access Technicians) certification. It is one of the most advanced technical achievements and internationally recognized standards for rope access work. Training includes comprehensive multi-day courses with extensive time on ropes. Technicians must pass written, oral, and practical tests to confirm skills and safety understanding. Within the SPRAT certifications, there are different levels based on technical understanding, safety skills and number of training hours on ropes. Depending on SPRAT certification levels and rope access experience, companies and contractors can then assemble the most appropriate team to get the job done safety—such as rope access technicians, supervisors, and engineers.
Companies should also maintain a written rope access program that is accessible to all employees, and includes safety specifications, training guidelines, up-to-date regulations, equipment checklist, and certification levels. Personnel should go through regular training to ensure being up to date on current practices in the industry, have a communication system in place while on the ropes, and have the ability and know-how to self-rescue or prompt rescue teammates if the need arises.
INDUSTRY-PROVEN EQUIPMENT
Effective equipment can make or break jobsite success. This is especially the case when it comes to rope access. Anything less than industry-tested, proven and up to date tools and equipment can gravely sacrifice safety. In rope access, proper equipment includes a harness, safety helmets, rope descender and ascender, anchors, connectors, back-up device, and ropes. Each piece of equipment should meet current industry standards, as well as their specific manufacturer guidelines.
Meeting industry standards means more than equipment types or abilities. While expected, wear and tear also must be assessed to ensure safety is never sacrificed. Harnesses should be checked for proper function of the buckles and wear on the waist bands, as well as corrosion on all metal components. Integrity of all anchors, bearings, and connectors should be assessed regularly before every jobsite, and ropes should be checked for exposed core fibers, and inconsistencies in texture. If issues are found with any equipment it must be replaced.
While not required across rope access industries, a two-rope system further decreases risk. In a two-rope system the rope access technician uses two primary ropes. There isn’t a designated main or safety line as both ropes are utilized as the main line. In this case, if something were to happen to one rope the system will continue to progress on the other rope without the need to move to a backup system. This not only provides enhanced safety to the rope access technician it allows work to continue without delays.
LOOK BEFORE YOU LEAP
Once on the jobsite, start every morning with a plan for the day and safety checks. Inspect all pieces of equipment. Confirm the anchors are set appropriately and are capable of holding the loads required for the day’s work. Examine the ropes, check to see if they are passing over any sharp edges. Ensure everyone knows where their teammates will be located throughout the day and what to look out for in potential hazards.
CLOSING THOUGHT
When it comes to rope access, it is imperative that crews are always aware of their surroundings and have detailed safety and communication plans in place. While the work doesn’t come without risk, understanding the intricacies of the jobsite, being trained to industry certifications, and working with industry-proven, up-to-date equipment will significantly enhance safety for those on and off the ropes.
About the Author:
Josh Monroe is the vice president of health, safety and risk management at GeoStabilization International. He leads the safety program for all activities throughout the United States and Canada. For more, visit www.geostabilization.com.
Modern Contractor Solutions, March 2022
Did you enjoy this article?
Subscribe to the FREE Digital Edition of Modern Contractor Solutions magazine.
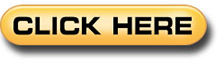