Remote control welding technologies offer welding operators the ability make critical process changes and parameter adjustments at the weld joint versus at the power source. Because many jobsites—from structural steel erection to pipeline construction, refinery projects and more—are often so expansive, the welding can take place hundreds of feet from the power source. Traversing the distance between the weld joint and the machine can pose safety risks, as well as adversely affect productivity.
To address these issues, as well as quality problems that can occur from greater distances between the power source and the weld, remote control welding technologies have been developed to eliminate additional cords and control cables. In some cases, these technologies even allow welding operators to alternate between welding processes remotely by the push of a button.
Today, there are remote control welding technologies available for both traditional and advanced welding processes.
BENEFITS OF REMOTE CONTROL
By allowing welding operators to adjust the welding parameters and/or processes at the weld joint, remote control technologies significantly minimize downtime for traveling back and forth to the machine. That provides for more arc-on time, which leads to a greater number of completed welds, higher overall productivity, and better profitability. It can also help companies avoid costly delays that could affect the ability to meet project deadlines.
Putting the welding controls next to the weld location also encourages proper machine settings and helps ensure better quality. Welding operators don’t have to settle for less than optimal settings or try to adjust their technique to accommodate for less than ideal weld parameters in order to gain good weld quality. Having that benefit is a particularly critical factor when a welding operator is performing the code-quality work.
Most importantly, wireless remote controls increase jobsite safety. By minimizing the need for welding operators to maneuver through an expanse of jobsite obstacles to reach the power source for adjustments, they are simply safer. There is less opportunity for injuries associated with trips and falls, either from the clutter of a work corridor or from cables associated with traditional remote controls.
How big are such safety risks on jobsites, really? In 2011, the Occupational Safety and Health Administration (OSHA) attributed 738 fatalities out of 4,138 (or 17.6 percent) occurring in private industry to construction accidents. Out of those 738 fatalities, the organization cited falls as responsible for 259 deaths (35 percent), putting this type of accident at the top in OSHA’s “Fatal Four” injuries. Fall protection is also cited as the top OSHA standards violation for preventable injuries on construction jobsites (www.osha.gov/oshstats/commonstats.html).
SMAW AND GTAW
Various remote control welding technologies are available for the Shielded Metal Arc Welding (SMAW) and Gas Tungsten Arc Welding (GTAW) processes commonly found in field applications. Wireless remote hand controls are one such technology and are especially prevalent in pipeline construction, structural steel erection, and maintenance and repair operations.
These controls offer the ability to make basic parameter changes at the weld, usually as far as 300 feet away from the power source, without the need for (or the tripping hazard of) a control cable. They include an on/off contact switch that adds to the safety benefits by allowing the welding operator to shut off ,the current output when it is not in use and the ability to adjust output.
Wireless remote hand controls operate by way of a radio signal and can be used to control the output of a variety of compatible machines, including engine drives or plug-in machines. They connect through a remote 14-pin connector and are synced with the receiver directly out of the box, featuring a unique address that ensures they communicate only with each other without crosstalk with other systems.
Wireless remote hand controls typically need to be operated “in the line of sight” of the power source, as the presence of structures or parts can block the radio signal. These remotes represent a percentage of the amperage set at the power source, similar to traditional corded remotes. As an example, if the remote is set at 40, and the machine is set at 300 amps, it indicates the welding operator is welding with 120 amps.
More advanced remote technologies are also available for SMAW and GTAW that provide welding operators with complete control over the welding process and eliminate the line-of-sight issues. They can still operate if a structure blocks the area between the weld and the power source.
These remotes feature the same controls as the power source, and use a weld cable for communication, which again eliminates the control cable and reduces clutter and tripping hazards on the jobsite.
Such advanced remotes can also sense incorrect connections and offer remote polarity reversing, ensuring that the welding operator is welding in the correct polarity for either the SMAW or GTAW process and able to gain the best weld quality. If the cable connection is not properly set up, the welding operator will be alerted by way of an error message, which indicates that the weld cables need to be switched at the weld joint.
These remotes also allow welding operators to set the actual amperage, as opposed to a percentage. As a result, the welding operator has the best weld settings for the application, making it easier to gain good quality and productivity. ■
Look for the conclusion to this article in the next issue of MCS.
About The Author:
Joe Ryan is a marketing segment manager, process pipe welding with Miller Electric Mfg. Co. For more information, visit www.millerwelds.com.
_________________________________________________________________________
Modern Contractor Solutions, January 2014
Did you enjoy this article?
Subscribe to the FREE Digital Edition of Modern Contractor Solutions magazine.
Remote Control Welding Technologies, Part 1
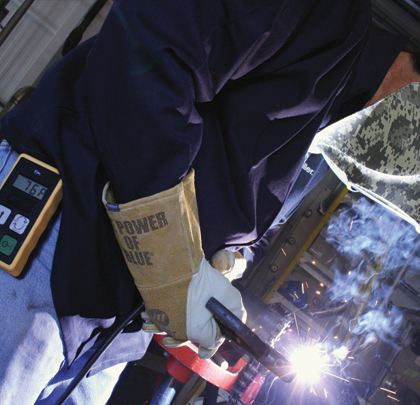