The desire to recycle in the world is no longer a debate, but rather a commonplace necessity. Recycling has become a way of life for the average American. What most people do not realize is that asphalt is one of the most recycled products in the world. The future is here, and the asphalt plants are using recycled product as it becomes more and more costly to produce it. For some asphalt professionals, recycling and reclaiming are thought to be the same … they are not.
THE CHALLENGE
The cost of the base materials that make up new asphalt have continually risen in recent years and will rise at an even greater rate in the coming years. The cost of asphalt cement (AC) and the petroleum-based products that are a part of its essential ingredients are constantly on the rise and it has become nearly impossible to find the quality, perfect sized aggregate that provides the best compaction, which only a few years ago was thought to be in endless supply. This does not even address the costs associated with disposing of used asphalt (RAP) in yards across the nation that the landfills and dumps will no longer take, even if it somehow remained wise to dispose of RAP in the past, it is now “black gold.”
Additionally, what most asphalt contractors quickly realize in this competitive market is that if they recycle or reclaim, they have asphalt when the plants have closed for the season. They not only keep working, as long as the weather allows, but they also get jobs that the other guy can’t even bid on.
The only question that remains is the correct process to get the job done. In recent years, the process of reclaiming and recycling has become confused due in part to manufacturers making claims that just aren’t realistic.
Reclaiming asphalt: The process of reheating asphalt, plant mix, or properly stored plant mix that has not been compacted, back to its original temperature of 350 degrees F by means of a heat source in a static hot box. This works well for virgin asphalt mix, but is unacceptable for compacted chunked, pulverized, or milled asphalt. When it comes to hot box reclaimers, “junk in, junk out.” The process of reclaiming can be maximized when contractors properly bulk-store asphalt mix for later use. You can effectively “reclaim” in a static hot box.
Recycling asphalt: Taking previously “junk” material, whether it was ever compacted or not, including saw cut, chunked, pulverized, or milled asphalt, and return it to its original state, back to its original temperature of 350 degrees F, and back to its original consistency. This is accomplished by means of a heat source, while agitating, folding, and recoating the aggregate and by adding new AC into the mix. This works well for all forms of asphalt and is the only way to truly recycle.
Asphalt cement: Manufactured from a process in which crude petroleum is separated into its various fractions through a distillation process at the oil refinery. After separation, these fractions are further refined into other products, which include asphalt, paraffin, gasoline, naphtha, lubricating oil, kerosene, and diesel oil. Since asphalt is the base or heavy constituent of crude petroleum, it does not evaporate or boil off during the distillation process. Asphalt is essentially the heavy residue of the oil refining process.
Whether it is chunked, pulverized, or milled asphalt product, in order for asphalt to be recycled, there must be a method to efficiently and effectively reintroduce AC. This is the binding agent for asphalt. This critical component must be evenly distributed to the aggregate in the agitation cycle of the process.
The AC must be uniformly introduced especially where RAP has been significantly oxidized from heat, sun, weather, and chemicals.
There are very few in the asphalt industry that will claim that true recycling can be accomplished in a static “hot box” or “hot box reclaimer” where there is no agitation, folding, or mixing action of the recycler. Without agitation, folding, and mixing, the AC cannot effectively coat the RAP material, and likewise, the RAP will not break down into a form that makes it usable (i.e., spreadable). Additionally, by avoiding the folding or mixing process, RAP will not effectively or efficiently release the moisture that makes the introduction of AC much less effective. Without steam or moisture boil off, RAP will retain moisture, especially during the temperate and wet months of winter, which will make it a significantly inferior, and hence ineffective, product.
THE SOLUTION
KM International manufactures “hot box reclaimers.” They are a significant and important tool for its customers that wish to reclaim plant mix or excess asphalt.
It is used to reheat asphalt or to keep product warm while being stored or transported. The hot box reclaimer can, in most cases, keep hot-mix asphalt (HMA) hot for up to 72 hours depending on the AC content. However, after many years of testing, it became obvious that you cannot truly “recycle” asphalt back to its original form unless it is agitated, heated thoroughly, and uniformly and sufficiently coated with AC. The final product must be in a form that can be used effectively and efficiently. It must be just like plant mix if it is to be considered recycled, to be usable. The development of the KM International T-2 Recycler was done with the cost and quality of the asphalt produced as the most important factors.
Quality asphalt is the most integral ingredient of any quality asphalt repair. The asphalt produced from the T-2 using a KM International formula is as good as, or in many instances, better than new.
It is very important that every contractor know what solution best suits their needs. In order to make informed decisions, honest and accurate information is an absolute necessity. Unrealistic promises bordering on dishonesty about product capabilities only cause future headaches. ■
For More Information:
KM International manufactures high-quality asphalt maintenance equipment. For more information, call 800.492.1757, or visit www.kminb.com.
_________________________________________________________________________
Modern Contractor Solutions, August 2013
Did you enjoy this article?
Subscribe to the FREE Digital Edition of Modern Contractor Solutions magazine.
Recycle or Reclaim: The Difference is Very Clear
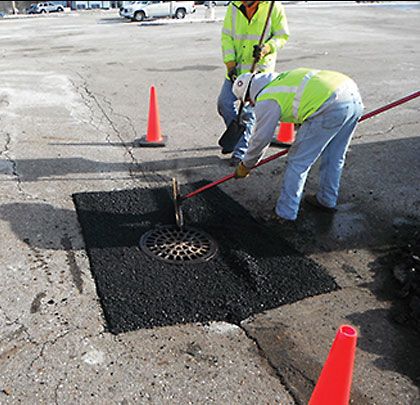