Near the Kansas City International Airport lies a well-traveled stretch of road that connects NE Cookingham Drive to I-435. A 20-mile jaunt separates the airport from downtown Kansas City, and while some drivers might make their way via the direct I-29 route, others choose the I-435 route that might take a little longer but sees less traffic.
If drivers happened to take the Cookingham/I-435 route during late summer 2019, they may have caught a glimpse of an impressive road construction project and some never-before-seen equipment. The construction site was home to a 24-foot-wide, 1,000-pound rolling tube of steel. And a real head-turner it was.
THE PROBLEM
The onramp that connects Cookingham Drive to I-435 appears to the naked eye to be a standard ramp, but the positioning of the onramp and the surrounding area were causing headaches for the Missouri Department of Transportation (MoDOT). A field that runs parallel to the ramp often produces significant rainwater runoff that makes its way onto the onramp. In a usual case, rainwater and subsequent runoff don’t pose huge issues for highways and ramps, but this was a different story.
Sedimentary dirt and debris filled the south side of the ditch and the onramp. As the ditch filled up with sediment and dirt carried by the runoff, the material would spill over onto the south lane of the onramp. This presented slippery, dangerous situations for drivers heading for the interstate at 55-60 mph. To combat the issue, MoDOT maintenance crews used heavy-duty equipment to tackle the buildup, closing the onramp every few years to clear the ditch and roadway with skid steers, track hoes, and several haul trucks. Last time they cleaned it, they shut down the onramp for 2 days to complete the cleaning. This method solved the problem temporarily but created headaches for drivers and a lot of unnecessary work for crews.
MoDOT tried incorporating pre-shaped paved flumes to carry the rainwater, but the flumes filled up just as quickly as the unpaved ditch and required just as much cleaning. MoDOT contemplated installing a rock-based lining, but research showed the quickly accumulating rainwater would likely carry the rocks away.
MoDOT continued to search for a viable solution to address the maintenance problem and finally found a permanent answer as part of a large concrete patching job on the roadway.
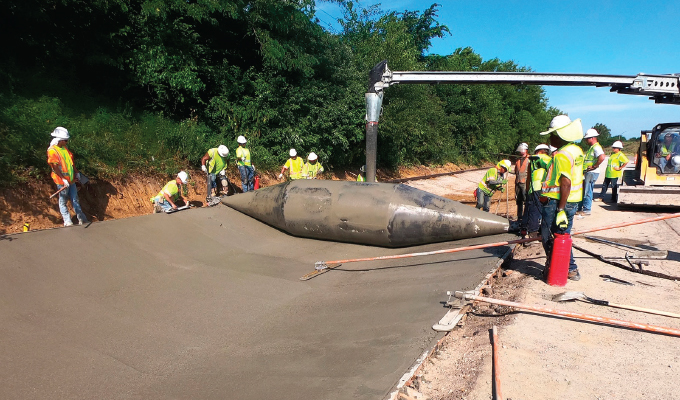
UNIQUE SOLUTION
In the early summer of 2019, Realm Construction was subcontracted to patch the concrete on Cookingham Drive and the onramp to I-435. Manager of Field Operations Russ Stark and his team specialize in concrete patchwork. They completed that portion of the job and then sat down to find a way to tackle the ditch liner, which was a concrete project they were less familiar with.
Stark, who has worked for Realm for more than 11 years, needed to find a solution that would stay within the budget and the assigned timeframe. The mission was to essentially line the ditch with concrete, and Stark initially only knew of one conventional method to accomplish it.
That method was to form the ditch in a sectional approach. This could be done either by pouring the bottom concrete and pulling a tube or screed up by hand, or pouring it transverse—coming down the slope to the bottom and then back up. Crews would pour one 20-foot bay, skip a 20-foot area, pour another 20-foot bay and so on. The next day, after the bays dried, crews could fill in the alternating empty areas. While this method is inexpensive and proven, it is time consuming and physically taxing.
“If we approached this project the conventional way, we’d only be able to pour about four bays a day, which is 80 feet of ditch liner a day,” Stark says. “At that rate, the project would have taken us 15-20 days. I knew we could do it quicker than that.”
Stark’s ultimate solution would include an approach that might end up with a higher initial equipment cost. But could that additional investment in equipment end up saving him time and money?
Stark proposed commissioning a large metal flume drum from Curb Roller Manufacturing. The company is known for their hydraulic- and battery-powered concrete roller screeds, but also manufactures custom-sized rolling drums. The drums are commonly used for pouring streets, medians, v-gutters or flumes, and while the company prides itself on creating custom solutions, this drum exceeded the size of any created in the past.
“I had seen a ditch liner drum on a different project a year prior and asked the contractor—Clarkson Construction—who made it,” Stark says. “It was only about 14 feet wide and I knew we’d need something nearly double that size. But I thought it could work.”
Curb Roller Manufacturing, based out of Fairview, Kansas, has been serving all industries from landscapers to government entities for more than 10 years. When Realm Construction approached them with the custom request, they were eager to engineer a solution.
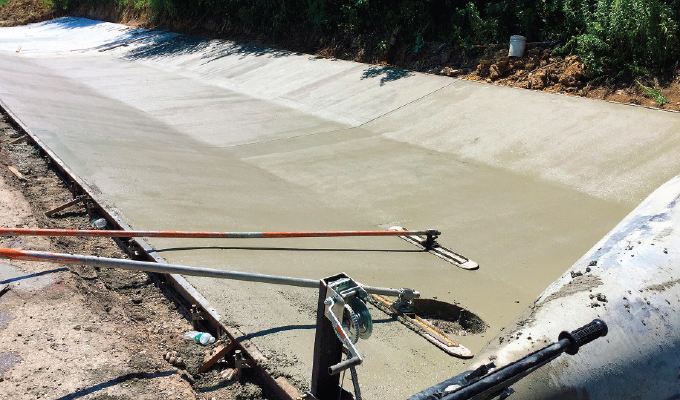
PROJECT STIPULATION
The contractors were also ready to begin the project, but delivering an oversized custom drum to a jobsite had its obstacles. First, Stark had to get approval from MoDOT to implement this unique equipment and process. He presented his case, highlighting the potential for a better finished product and a significantly improved timeline.
Matt Daulton, MoDOT resident engineer for the project, reviewed Stark’s proposal and approved with one stipulation—using the Curb Roller couldn’t increase the overall cost of the project.
“We try to encourage innovation on every project,” Daulton says. “I had never seen something like this, but our contractors and manufacturers in the industry often have new ideas and the best answers. So, we were open to it.”
After gaining clearance from MoDOT, Stark and his team had to work with the grading and excavation subcontractor who was preparing the ditch. The original design of the ditch, before implementing the Curb Roller idea, included varying widths and a flat bottom. This approach would save grading and excavating costs on a traditional concrete project, but the Curb Roller method would require a consistent width to successfully lay concrete. Stark was convinced that the extra cost in grading and excavating would make up for itself in the time savings down the line.
“I knew that this would create a more uniform product, which would be easier for MoDOT maintenance to clean out,” Stark says. “The original cross section of the ditch had varying slope widths and lengths through the entire 1,600-foot-long ditch liner. So, we had to get the grading team to adjust and create a consistent canvas for the concrete.”
While the grading and excavating teams prepared the base, Stark worked with Curb Roller Manufacturing to design and craft the perfect flume drum.
HERE COMES THE DRUM
Kraig Pyle, general manager of Curb Roller Manufacturing, worked with Stark throughout the planning process. While the company specializes in custom drums, they’d never designed something of this magnitude before.
“We had designed drums as long and as large in diameter, but never with this kind of combination,” Pyle says. “This was so impressive because it had such a large pan and slope wings. We know the capabilities of our product and we were confident taking on this challenge. We knew that with a few adjustments and alterations, we could pull this off and save the contractor time and labor.”
Stark officially submitted his order to Curb Roller Manufacturing: a 24-foot wide, 1,000-pound hollow rolling flume drum. He calculated the required slope of the sides of the ditch according to MoDOT requirements. Each wing section of the drum was 8 feet wide, with an 8-foot flat pan section in the middle. The drum was 52 inches in diameter with 4:1 backslopes. Since the ditch liner itself is 2 feet deep, they achieved a 25-degree rise by implementing a 1-foot drop for every 4-foot run.
CLOSING THOUGHT
Pyle sent Stark a design of the product, which he promptly approved. The company delivered the drum to the jobsite just 5 days later. Look for part 2 of this article in the next issue of MCS as the project unfolds and the savings are discovered.
For more information:
Curb Roller Manufacturing has been the world leader in shaped concrete roller screeds for more than 10 years. With high-quality products for everyday concrete work, Curb Roller’s ergonomic machines make it easy to shape standard curb, gutter, and sidewalks, flume, v-gutter, swale, and other unique shapes. For more, visit www.curbroller.com.
Modern Contractor Solutions, August 2020
Did you enjoy this article?
Subscribe to the FREE Digital Edition of Modern Contractor Solutions magazine.
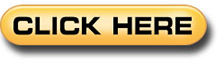