The Rammer range of hydraulic scrap shears are manufactured from HB400 steel and designed to be used in every industrial demolition job involving the cutting and recovery of ferrous materials such as iron sections, pipes, tanks, and more.
For work including excavation, building construction, demolition, crushing and screening, and recycling, the Rammer RSS23R delivers with a smart jaw design with a double guide to avoid materials becoming trapped.
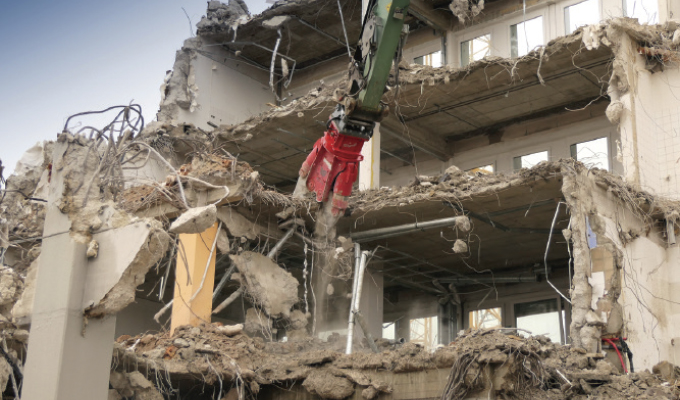
FEATURES AND BENEFITS
The Rammer RSS23R has field replacement wear parts for quick and easy maintenance and shorter working cycles, keeping uptime optimal for productivity. For compatibility, the scrap shears have the same bolt pattern as Rammer hammers. The heavy-duty components of the scrap shears provide durability, which ensures a long life span no matter the application usage. This is due to heat-treated pins and bushings, extending the working life and lowering the owning and operating costs of the shears.
Hydraulic rotation with protection valve: The protected rotation system allows precision tool placement, lowering/reducing owning and operating costs. The rotation is equipped with a relief valve, which limits the force applied to the structure and thus eliminates pressure and high-flow spikes. This increases the lifetime of your equipment (incl. both demolition equipment and excavator).
Upside-down cylinder with rod protection: The Upside-down cylinders with extremely long stroke are protected by the shear frame design. The hydraulic connections run through the piston rod. This high-tech solution minimizes the number of parts and downtime significantly. These state-of-the-art cylinders generate an extremely high force and have longest operating times.
Replaceable piercing tip: A bolt on piercing tip, removes the need for welding and rebuilding which lowers the cost of owning and operation. This essential tool of the scrap shears pierces plate scrap or beams effectively. The optimized shape forces the plate / beam into the jaws for maximized force. The design of the teeth at the front also eliminates wear of the arm structure.
Adjusting system for the cutting jaw: The gap between jaw and frame can be adjusted with the central pin, which enables the operator to maintain the product on the jobsite, keeping the cutting capacity on optimized level.
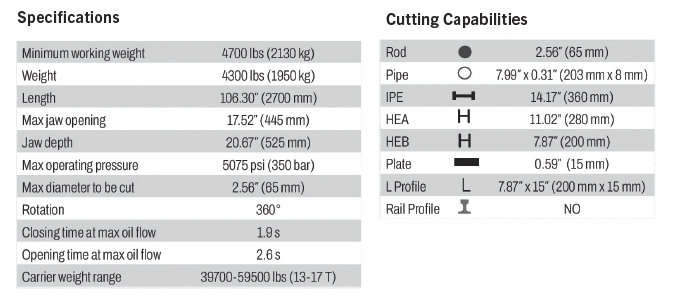
CLOSING THOUGHT
Sandvik acquired Allied Construction Products in 2020. Allied rebranded during 2021, changing the company name to Sandvik Rock Processing Solutions North America and marketing all products under the Rammer brand name.
For More Information:
Developed and tested in the harshest of conditions, the foundations of Rammer products are quality, operational reliability, and maximized productivity. Long working life and durability ensure Sandvik-owned Rammer attachments can be used efficiently and economically no matter the challenge at hand, making Rammer a sustainable choice. For more, visit www.rammer.com.
Modern Contractor Solutions, March 2023
Did you enjoy this article?
Subscribe to the FREE Digital Edition of Modern Contractor Solutions magazine.
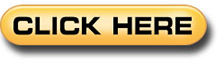