A summary of OSHA regulations governing concrete construction
Concrete and masonry construction is covered under the Occupational Safety and Health Act (OSHA) under what is known as Subpart Q (29 CFR §1926.70 – §1926.706). These regulations set forth the requirements for employers to protect their employees from accidents and injuries that can result from the variety of hazards that can accompany concrete work.
GENERAL REQUIREMENTS
The general requirements for masonry and concrete construction address a wide variety of issues. For example, a construction load may only be placed on a concrete structure where the employer has determined that the structure is capable of supporting the load, based on information received from a person qualified in structural design. In addition, OSHA requires that any protruding portion of the reinforcing steel be guarded to eliminate impalement if an employee were to fall onto it. Unguarded protruding steel rebar is a frequent subject of OSHA accident investigations and citations with regard to concrete construction. The general requirements also prohibit nonessential employees from being present in the hazard zone surrounding post tensioning operations and require signs and barriers limiting access to the work zone.
The general requirements in Subpart Q also address the need for personal protective equipment as well as proper use and maintenance of tools and equipment associated with the work. Working around cement, sand and water, particularly applied through a pneumatic hose, requires the use of protective head and face equipment, including goggles and hardhats. Concrete mixers must be equipped with mechanical devices to clear skip as well as guardrails on each side of the skip, and power concrete trowels are required to be equipped with automatic control switches that shut off power when hands are removed. Specific equipment and operation requirements are included for tremie sections, boat floats, and masonry saws, as are lockout/tagout procedures governing the use of all powered equipment. Additionally, the general requirements address the necessary components of bulk cement storage, requiring conical and tapered bottoms for bins, containers, and silos as well as mechanical and pneumatic means for control of flow of the material. Procedures are also outlined for bulk cement storage, requiring lockout/tagout of ejection systems prior to entry.
CAST-IN-PLACE CONCRETE
Subpart Q requires that form work be capable of supporting without failure all vertical and lateral loads that might be applied to it. Drawings and plans for all aspects of the formwork must be available at the jobsite, and all shoring equipment must be inspected prior to erection to confirm that the equipment meets the requirements in those formal drawings. Damaged shoring equipment must not be used and shoring equipment, once erected, must be inspected immediately before, during, and after concrete placement. In order to meet OSHA’s requirements, all baseplates, shore heads, extension devices, and adjustment screws in a shoring system must be in firm contact and secured when necessary, with the foundation and form. No single post shores to raise formwork may be adjusted after the placement of concrete. If vertical slip forms are used, they must be provided with automatic holding devices. Finally, forms and shores must not be removed until an employer has determined that concrete has gained sufficient strength to stand without them.
PRECAST CONCRETE
Among OSHA’s requirements for precast concrete is the necessity that all precast concrete members and units must be adequately supported to prevent overturning. In the case of tilt-up precast concrete members, any lifting inserts to tilt the member must be capable of supporting at least two times the maximum intended load. All concrete members other than tilt-up members must have lifting inserts capable of supporting at least four times the maximum intended load, and lifting hardware must be capable of supporting at least five times the maximum load. An employer’s precast work safety plan must ensure that no employees are permitted under precast concrete members being tilted or lifted in position, other than employees who are required for the erection of those members. Those employees who are engaged in the erection of precast members who are 6 feet or more above lower levels must also be protected by fall protection devices.
LIFT-SLAB OPERATIONS
OSHA requires lift-slab operations to be designed by a registered professional engineer. The plans and designs from such an engineer, in order to be implemented by the employer, must include detailed instructions as well as sketches indicating the method of erection. Jack or lifting units need to be marked to indicate a rating capacity and need to be loaded within that capacity, with controls located in a central location attended by a competent person who has experience in operating such controls. Other than essential personnel, employees should not be permitted in the building or structure while jacking operations are taking place.
MASONRY
Because of the hazards involved in lift-slab operations, a limited access zone must be established prior to the start of construction that is equal to the height of the wall plus 4 feet. It should be located on the scaffold side of the wall, restricted to entry by employees constructing the wall, and needs to remain in place until the wall is adequately supported.
CONCLUSION
Subpart Q contains an exhaustive array of safety regulations as to concrete construction that must be kept in mind when planning and completing such work. Although many of the general requirements seem to be guided by common sense, almost to the extent that a responsible contractor might think the regulatory requirement was unnecessary, even these requirements are important to keep in mind in preparing and training on a safety program and planning for work. Although prohibiting employees from riding in concrete buckets might seem self-evident to those with experience in concrete work, the issue of employee injury as the result of riding in concrete buckets was significant enough that OSHA included it in Subpart Q as a particular prohibition. A sufficient safety program under Subpart Q will contain specific prohibitions, training, and monitoring of all relevant portions of Subpart Q, even these seemingly self-evident issues.
About the author:
Thomas More Buckley is a partner in the Raleigh, North Carolina, office of Goldberg Segalla (www.goldbergsegalla.com). He represents businesses in complex commercial litigation matters including construction and safety as well as a wide variety of tort claims and contractual disputes. He is chair of the Construction Law and Litigation Committee of the International Association of Defense Counsel and is OSHA 30 certified. Buckley can be reached at tbuckley@goldbergsegalla.com.
Modern Contractor Solutions, April 2019
Did you enjoy this article?
Subscribe to the FREE Digital Edition of Modern Contractor Solutions magazine.
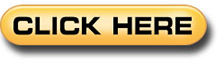