Though many 4-year degrees now come with mountains of student debt, one of the most in-demand career paths doesn’t require one at all. The construction and manufacturing industries are growing at promising rates, and skilled trades rely on skilled workers, who gain technical skills and certifications with vocational training rather than academic studies. However, because younger generations aren’t flocking to these industries or choosing to pursue technical skills, up to 2 million open manufacturing jobs will go unfilled by 2020. In fact, the Bureau of Labor Statistics predicts that another 1.6 million construction jobs will be empty by 2022.
Meanwhile, simple business growth will create 700,000 new manufacturing jobs over the next decade according to the Manufacturing Institute, and another 2.7 million jobs will be vacated by retiring baby boomers. The global gap between demand and skills is widening in construction too, as the struggle to find workers with more than a decade of skilled construction experience becomes even more challenging. Of course, 4-year degrees often result in more debt and less job stability than the skilled certifications that would allow more people to fill these positions.
Fortunately, as supervisors and contractors reevaluate their management methods, many are embracing an approach known as lean construction. This business practice revolves around productivity and efficiency. As we work to close the skills gap from all directions, it’s important to understand lean construction and how it can help.
WHAT IS LEAN CONSTRUCTION?
By 2020, PriceWaterhouseCoopers predicts that construction will make up 13 percent of the world’s economy. However, this industry has seen a decline in productivity for the past 4 decades, largely due to poor project management. Fortunately, lean construction takes a different approach to project management.
Lean construction practices are designed to maximize value and minimize waste, while improving effectiveness and efficiency. There are five main principles of lean construction, according to the Alexandria Engineering Journal, that have the potential to transform construction management methods.
Specify value: What is the value of each activity on your construction site? Any activity that generates value for the end product—whether it’s a property, service, or both—should be identified, and its value should be quantifiable. The client, customer, or project manager might define value differently, so it’s important to understand what matters the most, such as meeting a deadline or quality standard.
Identify the value stream: Once you’ve identified the value of each activity in your project, it’s easy to spot wasteful activities. If anything takes away from the overall value or doesn’t contribute to it, stop that part of the project. For example, overproduction is wasteful, but so is inefficient movement of the workforce. Is transportation planned carefully, and are you only storing the necessary amount of materials?
Ensure flow: It’s the project manager’s job to focus on the supply chain. Instead of looking at the end product, prioritize the smooth flow of the entire production process. From planning and manufacturing to building and finishing, every step and activity should be efficient and productive. For example, Global Construction explored simulation technologies and 3D printers as new ways to plan and manage construction projects.
Pull, don’t push: One key principle of lean construction is that pulling is better than pushing. Instead of up-selling to increase value or adding time to your schedule, make the process as efficient as possible while continuing to accommodate the customer’s needs. Be prepared to produce what your client requests, but don’t over-produce before the request comes in.
Aim for perfection: Perfect condition should be the only acceptable standard. The goal of lean construction is to exceed or meet expectations on schedule, without mistakes or defects. Communication with the client and all members of the construction team is vital, because it ensures that the customer’s expectations are understood and the staff has the necessary time, materials, and knowledge to meet them.
OVERCOMING THE GAP
Will more efficient management strategies really be enough to overcome the skilled labor gap? Lean construction actually calls for contractors to consider every resource and expense, so it could be one of the wisest ways to maximize current manpower. With the skilled labor shortage expected to grow, no skilled workers’ time should be wasted.
A MATTER OF TIME
While it’s still important for students to embrace technical skills and choose career in a skilled trade, fewer skilled workers still means we have more to do in less time. With so many shortages in construction and manufacturing, lean construction is an approach worth considering because it places the focus firmly on doing everything right the first time around.
BREAKING DOWN BARRIERS
Of course, eliminating all waste and streamlining projects will require some sacrifices, and everyone may not be on board. However, outdated and inefficient construction practices won’t become obsolete until most people accept that current trends are wasteful and we need a more efficient approach. As one McGraw-Hill Construction Report found, among contractors who aren’t familiar with lean construction, more than half don’t think there’s a need for change at all.
Lean construction has the potential to transform construction economically and technologically, but it will require a philosophical transformation first. Those who try lean construction overwhelmingly acknowledge that current practices are often inefficient. Managers must prioritize flexibility and quality while minimizing the potential for waste, whether that means ordering fewer materials or maximizing current manpower. Ultimately, efficiency will become increasingly important as baby boomers retire and less young people are trained to take their place.
CONSTRUCTING A LEAN FUTURE
Lean construction offers new opportunities not only for construction veterans, but also for newcomers to the industry. As efficient management becomes a more valuable construction skill, younger generations may seek out problem-solving construction project roles and the technologies they incorporate.
Looking to the future, lean construction could prevent a labor shortage from crumbling the foundation of the construction industry. By maximizing value and minimizing waste, lean construction could be the key to productivity and efficiency that construction professionals have been looking for. ■
About the Author: Carla Williams works in customer and media relations for the Williams Brothers Corporation of America. WBCA is a leading manufacturer of access doors and a family owned business. For more, visit www.wbdoors.com.
_________________________________________________________________________
Modern Contractor Solutions – August 2016
Did you enjoy this article?
Subscribe to the FREE Digital Edition of Modern Contractor Solutions magazine.
Putting Lean Construction to Work
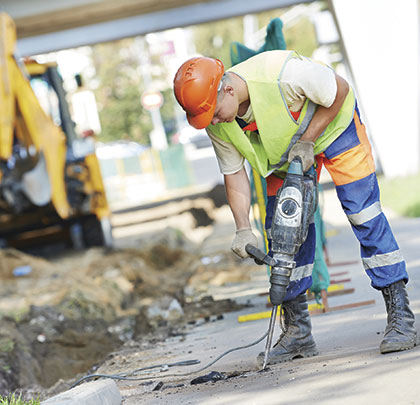