Managing a construction business is difficult and getting harder by the day. Projects are becoming more complex; attracting, hiring and retaining employees is increasingly cumbersome; and there are more details to manage than ever before—from both a project and business perspective.
Many contractors have adopted technology solutions to manage the complexity that’s inherent to construction, yet many of these systems don’t integrate or talk to one another, causing decisions to be made using outdated or incomplete data. On a macro scale, this can paint a false picture of where a project or the business stands in real time, leading to rework, diminished productivity, and profit fade.
This is where interoperability can be beneficial, which is when information flows automatically between two different data systems, ensuring all stakeholders are working with the same accurate and timely information in their system(s) of choice. Data integration is one means to achieve interoperability, typically by physically connecting data from two different software systems so that they can automatically share information with another—either at the project or company level.
Given the variety of software systems used by contractors, integrating project-specific data has increasingly become the holy grail of interoperability as it has the power to greatly enhance project visibility and streamline communication among stakeholders, ensuring that everyone is working off of the same information in real time. Because when everyone is using accurate, real-time data, projects can be kept on track and on budget, enabling contractors not only to maintain, but grow their profits.
INTEGRATING DATA
While the benefits of interoperability are simple and straightforward, the act of integrating data across multiple computer systems and software solutions built by completely different developers is complex. Each stakeholder in the project workflow has their own tech stack built to suit their specific needs, and each project has several stakeholders, including owners, designers, contractors, field staff, and office personnel.
In addition, each software system is built in a silo by a unique development team, which leads to differences in field-level validation logic such as rounding discrepancies. Users also often build in user-defined fields and workflow parameters that don’t translate well across different systems.
While it can be difficult to imagine a world where all technology systems automatically connect and exchange data, it’s being accomplished at the project and company level because the benefits far surpass the challenges that come with systems integration. Because a truly connected jobsite and organization translates to more streamlined workflows and enhanced efficiency, leading to better, more profitable projects and an overall stronger business environment.
REAL-WORLD EXAMPLE
Yates Construction, a family-owned commercial and industrial contractor based in Mississippi, knows the challenges of disconnected data all too well. As the company grew and began taking on bigger projects, the complexity of the construction process grew, too, with each owner, architect, engineer and contractor wanting to use their own project management system.
Given that Yates has hundreds of projects happening at any given time, it became an overwhelming task to manage different project management systems, particularly since each system had its own unique software requirements, which stakeholders had to learn to use.
“At the time, we were trying to find a way to simplify the process for ourselves and for our project stakeholders, who each had their own favorite project management software they wanted to work with,” says Benjamin Crosby, site manager for Yates. “We had to find a solution to make everyone’s data seamlessly talk to one another; otherwise, we wouldn’t be able to finish the projects we’d taken on, much less bid on bigger or even more complex jobs.”
Yates began working with platform-as-a-service provider (iPaaS) Data Xchange (formerly known as Ryvit), who helped connect their primary project management software to their accounting platform, creating a seamless flow of information and improving accountability for change. They also connected their primary project management software to other project management systems that Yates’ project owners and subcontractors frequently used, unifying systems and more importantly, the efforts of people behind the systems.
The integrations increased the efficiency of Yates’ projects and fundamentally changed how the company worked with and communicated with its stakeholders—from giving specialty contractors visibility into the progress of their change orders, to providing immediate updates to project owners about the status of work performed.
“Getting our project management system to talk to our ERP and other project management systems was a game changer for us,” says Crosby. “Now instead of having to guesstimate where things were or why something had changed, there was visibility and communication surrounding issues, linking people together and lessening frustrations.”
CLOSING THOUGHT
As the world continues to digitize, contractors need to have their data and their systems connected in order to stay competitive in today’s ever-changing environment. The world is simply moving too fast for them to continue to rely on disconnected systems that can’t talk with one another. This is particularly acute when it comes to project details, which are becoming more onerous and complex by the day. In contrast, when contractors integrate their technology systems, they can more easily see the project and the business at a glance, as well as the details in motion, enabling contractors to do what they do best, which is build better projects.
About the Author:
Tom Stemm is vice president and category GM of Construction Integrations at Trimble, where he helps Trimble and the larger construction ecosystem build connections between commonly used applications and data sources.
Modern Contractor Solutions, December 2023
Did you enjoy this article?
Subscribe to the FREE Digital Edition of Modern Contractor Solutions magazine.
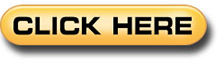