By Jamie Hodges
It’s no secret that contractors are dealing with major material price increases and supply chain bottlenecks that range from skyrocketing pricing to lead times taking 2-3 times what they normally would to procure materials. For example, structural steel, which used to cost 48 cents a pound now costs closer to $1 a pound, while lumber prices continue to remain above average since peaking last spring. The volatility of the market has understandably spooked many contractors into pausing or canceling projects under the assumption that things will improve in 6-12 months’ time.
However, if we’ve learned anything over the past year, it’s that the future simply can’t be predicted, particularly given continuing issues associated with the coronavirus variants and the infrastructure bill. That being said, as a contractor who has worked on a wide variety of industrial projects since the start of the pandemic, there are a number of ways to keep a project moving forward so long as you’re willing to be flexible and innovative. Below are a few key considerations to help fast track your project in today’s ever-changing business environment:
BRAINSTORM WITH CONTRACTORS
The most important tip to get any project off the ground is to brainstorm with your general and subcontractors. We’ve been dealing with many of these issues for well over a year and a half and have tips we can suggest, in addition to being able to evaluate where savings can be gained. This is best done at the beginning of a project since it’s much easier to make changes before plans have been solidified and materials have been ordered. But even if you’re midway through a project, it can still be helpful to bring us in to problem solve as there are usually options available that just haven’t been put to use yet.
ASK QUESTIONS AND SIMPLIFY
Once contractors are brought in, one of the first things we do is ask questions about whether a project can be scaled back or simplified as many projects are over designed from the outset. Taking a step back can help determine whether a design simplification is possible, which can lead to reduced materials, costs and lead time, which can also help the timeline. We recently simplified the design of a platform and changed out the materials on a hydro project, which enabled us to gain significant savings in both cost and time—all from simply asking the right questions at the right time.
MODIFY THE BUILD SEQUENCE
In addition to simplifying, it’s also worth evaluating whether the build sequence can be changed, particularly if it was set to be phased anyway. Doing so can enable you to build using the materials you do have while you wait for additional and/or new materials to arrive. This can also buy you time to evaluate where other savings might be gained, particularly when it comes to design simplification or material swaps.
GET CREATIVE
Swapping out materials is one of the most important changes a contractor can make, particularly given the astronomical prices of many materials today. For example, we’ve been recommending swapping concrete out for structural steel since it’s less expensive and more readily available. This can be done for structural projects all the way down to stairs and handrails.
In this same vein, it’s also important to choose less in-demand shapes and sizes for materials as many sizes are not readily available. This can be as simple as choosing beams instead of steel joists if the project can accommodate that or choosing an 8×15 beam instead of an 8×10 beam, which are difficult to find given their popularity in home design.
DON’T WAIT TO BUY
Once materials have been determined, it’s vital to order them as soon as possible, ideally once the design stage is complete and you have an estimate on the quantity you’ll need. With lead times taking 2-3 times their normal rate, this is a critical step towards ensuring you get what you need when you need it. While this may not completely resolve all your issues, ordering well ahead of time can help speed up the timeline, particularly for materials that are increasingly difficult to procure.
PREFAB, MODULARIZE
While the popularity of prefabrication was already on the rise, it’s increased during the pandemic given the many additional benefits it brings to a project, including its ability to offer cost and time savings since it can be done more efficiently. Unlike at a jobsite where there are a number of uncontrollable variables, prefabrication allows for a portion of a project to be built offsite in a quiet, weather-resistant, controlled environment. This provides for less distractions and less unknowns, helping to keep projects on track.
CLOSING THOUGHT
Regardless of how you approach a project, there are alternatives out there for both project owners and contractors to help ensure that projects start or stay on track. Given the uncertainty of the future, we recommend that stakeholders look at all of the options they have now given the unknowns that may lay ahead, which may be even more challenging than what is currently at play.
About the Author:
Jamie Hodges is executive vice president of Industrial Constructors/Managers, Inc. (ICM), a Colorado-based industrial contractor specializing in steel and concrete structures, heavy moving and rigging, machinery installation, modification and maintenance, and more. For more, visit www.icminc.net.
Modern Contractor Solutions, December 2021
Did you enjoy this article?
Subscribe to the FREE Digital Edition of Modern Contractor Solutions magazine.
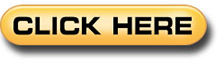