As a construction contractor, you know your machinery is one of the most significant assets in your operation. However, the construction equipment that you rely on daily is not immune to wear and tear, as it is often exposed to harsh conditions that can negatively affect its performance over time. Without proper maintenance, your equipment can become less reliable, less efficient, and more costly to operate.
Inspecting and maintaining equipment regularly helps you get ahead of potential maintenance needs or concerns, avoiding machine downtime in the future. By performing proactive maintenance, you can keep your equipment functioning at its peak, extend machine lifespan, and save money over time.
Let’s explore some benefits of being proactive in your equipment maintenance and what factors you should consider when building a maintenance strategy with your local OEM dealer.
TOP BENEFITS OF PROACTIVE MAINTENANCE
Any construction operation invests heavily in equipment, and protecting that investment is essential for your business’s success. Developing a proactive maintenance strategy is a good way to make sure that your equipment is in top shape and can bring significant benefits, such as lower operating costs, better equipment performance, and higher resale value.
Reduce operating costs: By approaching equipment maintenance in a proactive manner, you can spot potential issues with your equipment before they turn into major problems. Thus, maintenance can be performed quickly, reducing the need for costly repairs and replacements down the road. Regular inspections and preventive maintenance also improve fuel efficiency and reduce equipment wear and tear, lowering overall fuel consumption over time and the costs associated with equipment downtime. As a result, when maintaining equipment in good condition, contractors can cut operating costs and improve their bottom line.
Improve equipment performance & efficiency: Well-maintained equipment runs more efficiently and productively throughout any operation, reducing downtime and maximizing productivity on the jobsite. When performing equipment maintenance, we recommend using genuine OEM parts and fluids along with service performed by trained technicians for optimal equipment functionality.
Increase resale value: Prospective buyers are often willing to pay more for well-maintained equipment, as it indicates that the machine has been well cared for and is less likely to have mechanical issues. Contractors can demonstrate that their equipment has been properly maintained by keeping detailed records of maintenance services, including the dates and type of maintenance performed. This not only protects your equipment investment, but it also has the potential to increase the resale value of your machine.
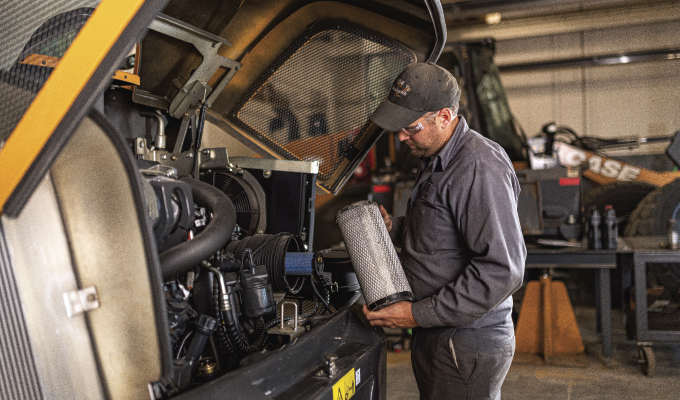
BUILD A PROACTIVE STRATEGY
Building a proactive maintenance strategy for your construction equipment can appear overwhelming, requiring a variety of factors such as maintenance needs, service schedules, and best maintenance practices. So, if you’re not sure where to begin, here are some key steps to consider when developing your maintenance strategy.
Develop a relationship with your equipment dealer: Establishing a strong relationship with your equipment dealer is a critical component of a proactive maintenance strategy. Your dealer is a valuable resource when it comes to expert maintenance advice on schedules and procedures, genuine parts, and certified service. They can assist you in developing a customized maintenance plan that takes into account your specific equipment, usage patterns, and operating conditions while also providing you with the necessary service and support to keep your equipment running smoothly. They can also register your equipment, allowing maintenance information to be tracked in real time, so you never miss a service.
Create a maintenance plan: A maintenance plan, like a CASE PlusCare Planned Maintenance Agreement from your CASE dealer, is a detailed maintenance plan designed to maximize the performance of your equipment. Your maintenance plan will include routine inspections, preventive maintenance, and timely repairs in the event of equipment malfunction. This will help you stay ahead of fluid changes, wear part replacements, and early signs of equipment issues, eliminating the stress of planning and budgeting for your machine maintenance needs. Your maintenance strategy will be tailored to your equipment’s requirements and outcome goals.
Implement a maintenance strategy: The implementation of a proactive maintenance strategy requires planning, execution, and ongoing evaluation. Your maintenance plan will outline the service tasks that need to be performed on your construction machine and the frequency with which they need to be completed. This maintenance plan should be reviewed and updated as needed to ensure that it remains effective and relevant to your equipment’s needs over time.
EQUIPMENT BEST PRACTICES
Beyond building your maintenance plan in partnership with your dealer, it’s important to employ best practices between service visits to keep your equipment running strong.
Train your operators: Proper equipment maintenance reduces wear and tear and prevents breakdowns. Train your operators on proper equipment usage, which includes performing daily inspections, identifying potential issues and reporting them. Ask your dealer for any training assistance for your crew.
Choose quality OEM parts: These parts are specifically designed for your equipment to ensure optimal performance and durability. Use OEM whenever possible, and work with your dealer to source and install them.
Keep accurate records: Create a system to maintain detailed records of all maintenance tasks, inspections, and repairs planned. This is an important step in determining the effectiveness of your maintenance strategy. It also ensures that all necessary maintenance services or inspections are completed on schedule.
Proactive maintenance is a critical part of protecting your construction machinery and making sure your equipment is functioning at its best. By implementing a comprehensive maintenance program, contractors can ensure their equipment is properly maintained and serviced, preventing breakdowns and reducing downtime.
CLOSING THOUGHT
For professional maintenance service and genuine OEM parts, trust the experts at your local dealership to create a successful maintenance plan to protect your equipment investment. For CASE Construction Equipment, we recommend the expertise and commitment of your CASE dealer. With their partnership and investment in your operation’s success, you can ensure that you are always prepared to tackle the next project with confidence.
About the Author:
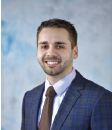
Ryan Schubert is an aftermarket services development manager for CASE Construction Equipment Parts & Service with more than 15 years of experience in the construction and mining equipment industry. Schubert is responsible for developing service solutions to improve customers’ total cost of ownership, reduce downtime, maintain safety, and customer satisfaction on construction products.
Modern Contractor Solutions, July 2023
Did you enjoy this article?
Subscribe to the FREE Digital Edition of Modern Contractor Solutions magazine.
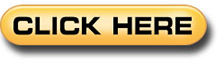