The costs of adhering to new and changing safety regulations, maintaining up-to-date protective equipment, and covering employee injuries is increasingly burdensome for many companies. This isn’t to say that injury prevention is not extremely important, but instead many businesses are taking the wrong, and often more expensive, approach.
Employees in construction and refractory can be exposed to safety hazards and long-term health risks at their jobsites. The cost of protecting employees—especially those new to the industry—in potentially hazardous situations can add up quickly. Shotcrete and gunite work is no exception. A recent initiative, Prevention through Design, is working to reduce injuries, improve worker safety, and lower long-term costs before machinery ever hits the market.
UNDERSTANDING PtD
Prevention through Design, or PtD, considers all hazards that could put workers at risk, including carelessness, distractions, and inexperience. Those considerations take place before the equipment is built, and then the safety features are tested before the product ever goes to market. When applied properly, PtD results in substantial savings for contractors through lower employee turnover and fewer injuries.
Manufacturers implementing PtD do so by emphasizing worker safety throughout the entire design and manufacturing process for new and updated equipment. Engineers, managers, and assembly workers are all encouraged to speak up if they spot a potential safety hazard.
With high-pressure shotcrete and gunite machinery, fast-moving materials, powerful pumps, and hydraulic systems present potential hazards on a daily basis while, at the same time, noise, heavy lifting, and air contaminants can result in long-term health problems if not properly addressed in the design stages.
While safety regulations are in place to protect workers and provide standards with which manufacturers must comply, manufacturers choosing to embrace PtD go above and beyond industry standards. In many cases, this prevents injuries and adverse long-term health complications. Rather than relying on personal protective equipment to bridge gaps between equipment functionality and safety regulations, some manufacturers take things a step further, factoring in functionality, operating expenses and customer preferences to design safe, user-friendly equipment. At times this even involves engineers working hands-on with equipment at jobsites, gaining end-user perspectives that can help advance product designs.
Fewer injuries, and in many cases the elimination of high-priced PPE, can add up to huge savings over the life of a new machine—leading more and more companies to take a close look at manufacturers that implement PtD.
PtD CONSIDERS “ALL THE LITTLE THINGS”
Prevention through Design leads manufacturers to make minor alterations to designs that, collectively, result in equipment that is both safer and more user-friendly.
While automatic shut-off switches on pumps are now a standard safety feature, they become ineffective when aging switches begin to malfunction or when material buildup interferes with proper operation. Malfunctioning switches force operators to manually reset and restart the mixer-pump. In some cases, operators simply bypass the old contact switches altogether, eliminating any safety benefits. Some manufacturers have addressed this problem by using non-contact limit switches. These switches, even with material buildup, stop and start everything with the opening and closing of the grating.
Another regulation that equipment manufacturers can make less burdensome for contractors is noise. By designing equipment that is compliant with noise regulations for 8-hour shifts, workers are able to limit their use of noise-reducing headgear. That PtD feature prevents hearing loss claims from employees who don’t follow proper PPE standards.
PtD extends beyond the equipment, too. Many third-party trailers aren’t designed specifically for mixing and pumping applications and the corresponding safety considerations. Some shotcrete and gunite machine manufacturers produce their own trailers as a means of cutting manufacturing costs, while others design and produce their own to ensure each trailer is perfectly suited for its pump. The latter provides an opportunity to include reinforcements wherever necessary, reducing the likelihood of the trailer not being sufficiently sturdy. Manufacturers choosing this route are also more likely to choose heavy-duty steel, use durable welds and incorporate a sturdy axle that is properly aligned and balanced. Contractors need equipment that can be safely and conveniently transported at highway speeds, and having a well-constructed trailer with an axle rated for highway use reduces the odds of a dangerous incident.
A well-built machine also will have minimal sharp edges, rough surfaces, pinch points, and potential fall hazards to reduce the risk of cuts, abrasions, burns, and head injuries. When it comes to sawing, welding, and fabricating equipment parts, a little extra attention on the manufacturer’s part can eliminate sharp, abrasive edges and surfaces. Designs should also take into account worker heights to minimize strain; not all workers are 5-foot-10 inches, and machines shouldn’t be designed as if they are.
Machines with adequate platforms and wide walkways provide room for workers to move freely, and in some cases, have space for multiple people. High-quality diamond plate grating, sturdy ladders, and ample railings can also go a long way toward enhancing safety. When equipment is being manufactured, many of these factors can be overlooked or simply ignored to keep the process moving forward without causing delays and adding costs. Not with PtD.
CONCLUSION
Reducing hazards through smart designs is one of the most effective solutions for preventing injuries, reducing the need for protective gear and staying one—if not two or three—steps ahead of regulatory standards. Cautions, warnings, yellow paint, and protective equipment are standard with most industrial equipment, however designing out hazards is becoming an equally popular—and more effective—method for reducing the risk of injury. Over time, this makes equipment less expensive to own and operate.
Ultimately, it’s tough to argue with equipment that’s designed to protect workers by preventing safety hazards. Saving money is just an added bonus.
About the author:
Tripp Farrell is president of Blastcrete Equipment Company, a manufacturer of safe, reliable and user-friendly solutions for the refractory and shotcrete industries for more than 60 years. With a complete product line that consists of concrete mixers, pumps and related products, the company serves the commercial and residential construction, ICF and SCIP building systems, refractory and underground markets. For more information, visit www.blastcrete.com.
Modern Contractor Solutions, December 2018
Did you enjoy this article?
Subscribe to the FREE Digital Edition of Modern Contractor Solutions magazine.
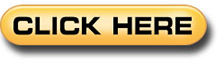