The Chicago Transit Authority (CTA) provides service to Chicago and 40 surrounding suburbs. The CTA’s 1,190 train cars operate over eight routes and 222 miles of track. Its trains provide about 750,000 customer trips each weekday and serve 144 stations in Chicago. During the summer of 2012, three concrete bridges in Evanston, Illinois, in use by CTA, needed widespread repair due to extensive freeze-thaw damage and prolonged stress conditions. The Dempster, Greenleaf, and Grove Avenue bridges are part of the extensive elevated transit system used by Chicago commuters. All three bridges totaled approximately 10,000 square feet. Upon examination, it was found that the existing bridges were beyond repair and they were demolished.
REPAIR PROCESS
Each of the replacement bridges was preassembled at street level and the waterproofing was then applied after the deck plates were in place. On the new bridges, the decks were first sandblasted then primed with D.S. Brown’s Deckguard primer using the squeegee and spray method. The Deckguard membrane was then applied in two passes, ensuring a nominal membrane thickness of 80 mils. The CTA had worked with D.S. Brown and their other products in the past, but this was their first experience using Deckguard.
D.S. Brown’s Deckguard membrane is a 100-percent, two-component, bridge-grade elastomeric coating used to waterproof both steel and concrete bridge decks. Deckguard provides a seamless, flexible, extremely durable barrier against water penetration and stray current. It is specifically engineered for use on highway and railway bridge decks, abutments, pier caps, tunnels, and pedestrian walkways. Deckguard can be used on intermodal and LRT rail bridges with or without protection board, providing fast turnaround for demanding schedules.
Deckguard has the highest tested resistance for crack-bridging, having been tested to 40 cycles for 1/8-inch at -15° F to ensure watertightness under extreme deck movement. It is the first membrane system to use IR fingerprinting during manufacture and to provide individual batch IR printouts with each shipment guaranteeing material shipped meets all published test data. This membrane provides maximum protection against stray current, making it ideally suited for use on cantenary and live third rail LRT bridges for protection of embedded steel reinforcement and steel decks.
During the bridge construction, the crew had several trials to face. Sandblasting in a commercial area required the dust to be contained. Added safety considerations were required during all phases of the Deckguard Waterproofing System installation due to the bridges’ 30-foot elevation. With deck temperatures in excess of 110° F and windy, the jobsite conditions were challenging. Additionally, there were several scheduling pressures as the Chicago Transit Authority would levy a charge of several thousand dollars per hour if the bridges were not in service by a specific time. To ensure all of these challenges were met, a D.S. Brown representative stayed onsite throughout the process.
FINAL RESULTS
The challenges on the jobsite required quick thinking on the part of D.S. Brown. The traditional method of using a squeegee did not work well with the excessive temperatures and affected the cure rate of the primer. Therefore, a modification was made to use a sprayer instead. It was a success.
“The Deckguard membrane was installed flawlessly. The consistency of the color from batch to batch showed significant attention was paid to the quality control during manufacture. All quality assurance testing was completed showing the Deckguard surpassing the specification in all aspects,” says Bill Kudrenski, waterproofing consultant.
The outcome of using Deckguard on these new bridges was that the bridge decks are completely protected from corrosion. The expected service life is more than 50 years. The membrane should last indefinitely provided there is no severe trauma on the membrane. Minor local repairs can be done as needed. ■
For More Information:
Founded in 1890, The D.S. Brown Company is a leading worldwide designer, supplier, and manufacturer of engineered products for the airport, bridge, and highway industries. D.S. Brown’s home office and manufacturing facilities are located in North Baltimore, Ohio. For more information, visit www.dsbrown.com.
_________________________________________________________________________
Modern Contractor Solutions, March 2013
Did you enjoy this article?
Subscribe to the FREE Digital Edition of Modern Contractor Solutions magazine.
Preserved For A Lifetime
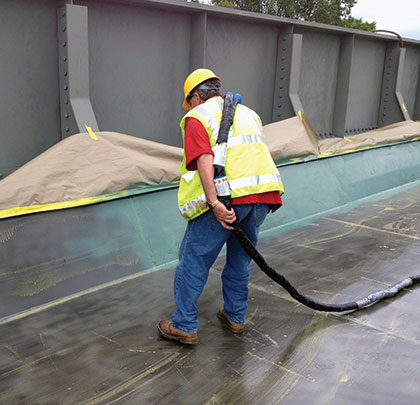