Our recent Global Capital Project Outlook (GCPO), launched earlier in June, found that the construction industry is responding to recent inflation, supply chain volatility, and labor costs by doubling down on digital transformation to improve project certainty. The industry is increasingly adopting digital best practices such as harnessing historic data to fuel smarter plans and forecasts, and there’s been a substantial improvement in project certainty, especially in delivering on or ahead of schedule. Yet, there is evidence that improved performance on some project metrics is coming at the expense of others, with average overspend also increasing, especially among those that stay on time the most.
A factor contributing to this, is that often delivery models and contractual arrangements can encourage contractors to consider time, cost, and scope in silos—or even prioritize some metrics over others. Perhaps unsurprising, as traditionally, projects have gone through very finite stages, one after the other.
First define the scope and requirements, then perform the design, then carry out the construction. This “waterfall” approach does not lend itself to the kind of collaboration that can lead to predictable outcomes across all metrics. Contributing to this issue, traditional delivery models such as Design-Bid-Build also involve an uneven distribution of risk among stakeholders which can mean that project performance is monitored individually rather than holistically.
All of these factors create an environment where different stakeholders are inclined, even incentivized, to protect their own self-interests (legally and otherwise). In turn, this fosters a mentality that sounds something like “collaboration is great, but only to the degree that we are contractually obligated.”
WINDS OF CHANGE
Now for some good news. The industry is facing a massive labor shortage. Supply chain disruptions and inflation are battering project costs and schedules. Demand for construction is increasing faster than the industry’s ability to deliver. That’s the good news? Yes, because these factors, among others, are creating winds of change that are driving a significant transformation of the industry.
In our recent industry survey, respondents stated that the most preferred project delivery models are now Integrated Project Delivery and Design-Build, both of which prescribe a more collaborative, more iterative process, improving visibility and predictability across all project metrics.
Certainly, the desire for more collaboration correlates precisely with the desire for more predictability in project outcomes. But there’s also an intense need to drive efficiency and improve productivity—a notion that has transitioned from a worthy ambition to a matter of survival as organizations face the reality of having to do more with less.
TECHNOLOGY REVOLUTION
While this desire for project certainty and increased productivity is nothing new, it’s now being enabled by a technology revolution that is finally transforming it into a tangible reality. The key is harnessing technology to enable more collaboration and therefore integration of project performance management across all project stages, stakeholders, and targets.
Construction 4.0 technologies such as connected data and automation are now also allowing time, scope, and cost to be centrally monitored and managed in a unified way. Today’s digital project management platforms can now monitor EVM performance across all metrics to highlight the interplay between them, such as when accelerated project delivery can cause rising costs. This can help highlight trade-offs. For example, where projects stay on time by spending more on headcount or equipment, or by de-scoping the project.
Construction-specific solutions that run in the cloud and take advantage of mobile devices inherently remove bottlenecks to timely collaboration. The valuable information these systems capture—and make easily accessible—is helping to achieve lofty goals like making crews more productive, reducing time wasted searching for (and sharing) information, and eliminating re-work resulting from poor communication. Further, such systems enable project data to continually feed an organization’s knowledge library, becoming a valuable source of information for those planning future projects. In fact, the GCPO report found benchmarks and/or historic project data are now being used almost half of the time to improve project predictability.
INTO THE FUTURE
But that’s just the beginning. Looking into the future, it’s not hard to envision a massive transformation occurring in the physical construction environment much like the one that has already happened in the virtual environment. Think about it: in the past couple of decades, design for construction projects has transitioned from 2D to 3D, meaning the design for a building is no longer represented by a series of lines in a drawing, but rather is now made up of thousands of objects, such as pilings, columns, and pipe spools. The real benefit in that transition is that all of those objects have intelligence baked into them. Meaning a pipe spool in a 3D model very likely knows what its dimensions are, what its material spec is, and so on.
In the 2D world, getting any sort of intelligence out of design drawings required all sorts of human analysis—even just getting quantities required manually tracing over and measuring the drawings. In contrast, the “smart” objects now regularly found inside 3D models not only help automate the quantity take-off and construction planning process, but more importantly set the stage to automate the tracking of project progress itself.
Today, if you want your 3D model to show the planned work in comparison to the actual work that has been accomplished, someone at the project site has to manually monitor, measure, and record the work that has been performed, then manually update that information into an as-built version of the 3D model to show the progress. After a lot of effort, the appropriate pilings and columns and pipe spools in the model light up and you can see the progress.
BEING SMART
But what would happen if we made the actual physical components smart, just like their virtual avatars in the 3D models? What if you could embed many of the constructed components at a jobsite with the innate ability to communicate information about themselves, so that they can participate in the as-built 3D model automatically? One of the largest semiconductor companies in the U.S. is already well down the road toward producing smart “stickers” that can be applied to just about anything, with the ability to communicate through the cloud using the same tech your mobile phone uses (but with years of battery life rather than hours).
Whether applied during fabrication for objects like pipe spools, or at the point of construction for cast in place components like pilings or foundations, you could end up with a smart jobsite composed of objects with intelligence baked into them. That intelligence starts in the 3D model but would carry on into the physical world. It could lead to projects that continuously and autonomously report key information that is central to controlling cost, scope, and schedule targets. Smart physical objects could not only help communicate as-built progress information back to the 3D model during construction, but could also provide valuable information post-construction, during the maintenance and operations stages of the building.
CLOSING THOUGHT
While this future vision will soon be technologically possible, it’s not yet practical. In the meantime, the amount of data relative to a construction project continues to grow immensely. Modern cloud-based, integrated construction management solutions will be the conduits to share—and make sense of—all that information, to drive the visibility necessary to support the more iterative project delivery models to which the industry is moving. And for an industry that must find new ways to increase efficiency just to keep up with demand, construction is only at the beginning of its digital transformation. These changes are positioning the industry for a successful, more collaborative, and more predictable, future.
About the Author:
Brad Barth is chief product officer at InEight. For more, visit ineight.com.
Modern Contractor Solutions, August 2023
Did you enjoy this article?
Subscribe to the FREE Digital Edition of Modern Contractor Solutions magazine.
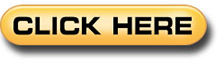