When it comes to today’s construction material options, the key phrase is low impact. Focus should be on the design and production of a construction sequence that will have the lowest effect and offer a shorter construction process that helps mitigate labor costs and results in time savings across the board.
It’s a well-known secret that precast offers a more efficient process than cast-in-place, for multiple reasons:
- Time is money, and precast products are more easily and quickly installed, saving time and money on the jobsite.
- When it comes to labor, less is more, and with an ongoing labor shortage across the construction industry, using a smaller crew on-site saves money.
- In most cases, weather doesn’t delay production of precast products the way it would on-site.
- A shorter install time equals a smaller budget.
- Choosing precast concrete products means no product waste left over for disposal, and less mess on the jobsite.
Let’s take an in-depth look at the precast process from start to finish.
STAGE ONE: ENGINEERING
The precast process begins with engineering. Proper precast should be concepted using the latest design tools, to include a computer-aided design process and detailed drawings. Approved design drawings make their way to the factory floor and are referenced to monitor proper production parameters.
STAGE TWO: MANUFACTURING THE REINFORCEMENT CAGE
When assembling the rebar cage, the first step of the process is the cutting and bending of the steel reinforcement. The correct rebar is selected, shaken down off the storage rack, then cut and bent to meet the exact specifications and requirements of the product. Next, the bars are assembled and tied together to form the reinforcement cage. Rebar wheelchairs helps position the cage within the form and to ensure proper clearance of reinforcing.
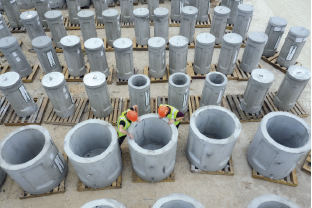
STAGE THREE: FORM PREPARATION AND PRE-POUR INSPECTION
Once the cage assembly is complete, it’s time to prepare and clean the form. Good precast construction uses proper forms in order to create a product that will stand the test of time.
At this point, all openings, cutouts, or embedded items are secured to the form. A form release is applied to each surface to ensure that the final product can be easily lifted from the form. Now that the form is prepared, an overhead crane is used to pick and place the cage onto the core of the form. Care should be taken to ensure that the reinforcing cage is stable for transport to the form.
A certified quality control technician should pre-pour inspection to ensure compliance with the original shop drawing. Once approval from the technician has been gained, it’s time to move to the next step: pouring concrete.
STAGE FOUR: CONCRETE PLACEMENT
At Oldcastle Infrastructure, a variety of certified raw materials are used, to include cement, coarse aggregates, sand, and chemical add mixtures. Each ingredient is carefully selected and mixed according to specific design requirements.
Each Oldcastle Infrastructure precast factory has a concrete laboratory used to conduct routine raw material testing and control exact quantities for each batch. This is especially important when using high-flow, self-consolidating concrete: the lab collects sample cylinders used to check compression strength and verify quality of each batch.
Once the materials are properly mixed, the self-consolidating concrete undergoes a variety of additional tests, to include a spread test to verify the mix has the proper flow and no segregation of the aggregate. The approved batch is then transported in a bucket via overhead crane to the product form on the production floor. Concrete is placed into the form and care is taken to allow the concrete to float without entrapping air voids.
Once the form is filled, the specified finish is applied and the curing process begins.
STAGE FIVE: CURING AND STRIPPING
Curing might include tarping the product overnight to capture the heat from the hydration process. The controlled environment of a precast factory enables the product to properly cure and reach the full design strength.
Once the quality control technician confirms that the product has reached the desired strip strength of 2500-3000 psi, then the stripping process may begin.
Stripping involves opening the outer jacket, collapsing the inner core, attaching the lifting devices, and removing the product from the form. Once the product has been removed, it is then cleaned, and the post-pour inspection is conducted.
STAGE SIX: POST-POUR
If all design dimensions have been maintained and no visual defects are noted, the quality control technician will sign off on the product. The final product is then labeled and transported to the yard. Care is taken to make sure it is stored on proper dunnage as it awaits customer demand.
When the customer is ready to receive the order, the product is loaded on a truck and properly tied down for shipment and delivery to the project site.
MANHOLE SHORT STORY
Several years ago, a jobsite in California required—per the local county—some 350 cast-in-place A-4 cleanouts. During the project, the contractor learned that if he converted 250 of the cast-in-place cleanouts to precast, during the short period of construction he could save 2.5 days off the total length of the build schedule. Primarily because choosing precast would allow for the digging and plating of multiple holes, with the crew returning the next day to clean each site, rock each site, set the cleanouts, stack out risers, and finish grade.
This example illustrates the many benefits again—schedule savings, time savings, labor savings, and so much more—that are realized when precast is specified for a jobsite.
CLOSING THOUGHT
Oldcastle Infrastructure leverages decades of experience and a passion for improving the infrastructure products of today. A nationwide network of precast facilities means that precast products may be used in a number of markets and the precast products needed are most likely close at hand. For minimal impact and maximum satisfaction, it’s tough to beat precast.
About the Author:
John O’Rourke is general manager with Oldcastle Infrastructure. For more, visit oldcastleinfrastructure.com.
Modern Contractor Solutions, October 2023
Did you enjoy this article?
Subscribe to the FREE Digital Edition of Modern Contractor Solutions magazine.
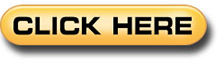