Personal protective equipment (PPE) is as vital in keeping construction workers safe at a jobsite as proper vehicle and equipment maintenance, but ensuring PPE integrity can be tricky.
Unfortunately, poorly maintained PPE increases both the likelihood and the severity of workplace injuries, which can have ripple effects throughout the organization, including workers’ compensation fees, productivity and profitability loss, lawsuits, and reputational damage—the latter of which can negatively impact bid win rates and the ability to attract new employees and contractors.
Keeping workers safe on the job should come in at number one on the priority list for businesses. By using customizable, digital inspections, managers can track and monitor PPE conditions to ensure no faulty PPE leaves the building.
PPE IN CONSTRUCTION
The construction industry is a high-risk environment to work in, and employers have to account for all possible job hazards when assessing what PPE to provide for their crews. Whether employer-provided or employee-provided, it is the employer’s responsibility to ensure any and all PPE used is effective, properly maintained, and sanitized.
“Contractors and employers can be liable when equipment fails or is never issued, but also for […] failing to inspect safety equipment regularly, and failing to repair or replace any safety measure that has been reported as faulty,” explains law firm Hofmann & Schweitzer.
According to the Bureau of Labor Statistics, “The number of DJTR (days of job transfer or restriction) cases in the private construction sector increased 10.4% in 2021 to 35,200 cases.”
Law firm Cooney & Conway cite PPE failure as one of the top causes of construction industry injuries that can range in severity, from minor to DJTR and even death, including fall, struck-by, and electrocution injuries.
MAINTENANCE & HISTORY
Reusable PPE needs regular maintenance and upkeep, including proper storage and sanitation, for maximum efficacy. Because different PPE has different maintenance requirements, it can be difficult and a bit tedious to effectively track and monitor each piece, especially when using manual tracking methods like spreadsheets and paper forms. Construction organizations can use cloud-based, automated software with a native mobile app, such as fleet management software (FMS), to customize digital inspections for all types of PPE. Workers can complete inspections using their mobile device. Results from digital inspection submissions are uploaded in real time, and failed inspection items automatically alert management to the problem so corrective action can be taken quickly to ensure maximum safety compliance.
Since a large part of PPE maintenance is knowing the signs of wear and tear, damage, and equipment faults, managers should clearly communicate these signs and what to look for with their crews so they can perform inspections with the knowledge and understanding of what to inspect and why. Managers can even provide instructions for any inspection task, and employees can attach images and documents or leave comments within inspections, improving communication around maintenance and faulty PPE. Custom inspections can include such items as rips, tears, fraying, breakage, sun damage, loose stitching/thread, cracking in plastic components, sharp edges on plastic components or metal fasteners, severity level of natural wear and tear, and more.
An added benefit of using FMS to manage PPE is inventory logs. By adding PPE to the fleet’s parts inventory, companies can easily see what PPE is available and what has been purchased, as well as evaluate replacement and procurement needs. PPE inventory logs provide key management data, such as:
- In-use and backup PPE inventory counts
- When specific pieces of PPE were purchased
- How much and/or how often specific PPE has been used over a certain timespan
- To whom specific PPE is assigned
This information improves accountability among crews and can help companies develop a PPE management program based on historical insights.
BENEFICIAL HISTORY DATA
Cloud-based FMS with automation features and a high level of customizability allows fleets to track and manage any fleet asset, from vehicles and heavy equipment to tools, trade supplies, and PPE. FMS automatically collects, consolidates, and aggregates data to provide real-time insights and reduce data overload.
One of the key benefits of its use is automated, configurable reporting based on current and historical data, which allows companies to easily see PPE trends over time, such as:
- Usage
- High-fail items
- Low- and high-performing brands/products
- Cost trends
- Inspection compliance rates, including overdue inspections
PPE can also be assigned to specific employees or vehicles to maximize accountability and reduce instances of lost or misplaced PPE. On the topic of lost and misplaced PPE, by adding PPE to the company’s parts inventory, appropriate storage locations can be assigned so everyone knows exactly where each piece of PPE is supposed to go.
CLOSING THOUGHT
Using customizable, digital inspections and PPE assignments in FMS provides increased accountability and clean historical data for improved insights into types of PPE failures, failure rates, replacement time frames, procurement needs, product/brand quality, and preventive maintenance compliance rates. Using this data, fleets can determine if, and what, changes they need to make to improve safety compliance, reduce PPE-related expenses, and help ensure all crew members end the day the way they started—uninjured and in one piece.
About the Author:
Rachael Plant is a content marketing specialist for Fleetio, a fleet management software company that helps organizations track, analyze, and improve their fleet operations. For more, visit www.fleetio.com.
Modern Contractor Solutions, September 2023
Did you enjoy this article?
Subscribe to the FREE Digital Edition of Modern Contractor Solutions magazine.
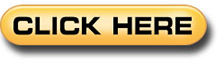