What’s next” is a question the design and construction industry will never tire of asking, and one the industry’s leading product manufactures will never tire of answering. New and different often begins with the basics: aesthetics, functionality, or technological advances. To be implementable on a wide scale, however, product innovations must also be achievable for the builder from a cost, constructability, and schedule perspective. To be truly successful, products must stand the test of time and deliver a reliable lifecycle based on durable quality and knowable upkeep. When it comes to decorative flooring, putting it all into a single solution that betters what’s already available isn’t merely about the latest technology, but the craftsmanship applied every step of the way.
DECORATIVE CONCRETE
“Bomanite’s Renaissance Deep Grind is a high-end, readily customized decorative concrete that really bring designs to life,” says Dan Kroesen, a vice president with Musselman & Hall, a Bomanite licensed contractor serving the Kansas City market since 1914. A legacy builder, Musselman & Hall’s divisions developed in response to changing market conditions over a hundred and four-year history include structural concrete, asphalt, railroad, and decorative concrete. “Even though decorative concrete is our newest division of some 25 years now, it has become what we are most well-known for. Renaissance Deep Grind is one of the innovations we’re proud to bring to our market.”
The Renaissance Deep Grind polished concrete system represents a custom mix of individually sourced aggregates, sands, and added integral colors that can be installed as a slab on grade or unbonded overlay. Once the concrete sets, it is milled, ground, and finally polished to produce a beautiful, solid surface that looks and wears very similar to terrazzo. The finished product also represents about the lowest possible lifecycle cost per square foot of any flooring type and far superior wear resistance over conventional polished concrete.
“This highly decorative surface competes favorably with the more expensive traditional epoxy terrazzo floor in beauty and durability,” continues Kroesen. The system’s customization capacities are virtually limitless. Musselman & Hall and other Bomanite licensed contractors around the country work with designers and owners to hand-select natural aggregates like limestone, granite, or river rock, often from a source close to the project. Local references are frequently blended with hand-seeded aggregates such as new or reclaimed glass chosen specifically by the owner or designer to emphasize a particular color or design reference or add durability in high-wear situations.
Local aggregates and sands add a familiar feel to the floor’s finish, but sourcing is also important because the selected aggregates must be available to supply the entire project. Kroesen admits it often take his team a series of sample iterations to dial in on a particular client’s tastes in the finished look and having Bomanite’s high-level technical support is critical to getting the mix exactly right. “The Renaissance system checks a lot of boxes—tremendous design flexibility, first-cost savings, and it is even cheaper to maintain than regular concrete.”
LONG-TERM COST POSITIVES
While every type of flooring requires regular maintenance, one of the advantages of the Renaissance Deep Grind process is the long-term cost positives. Because the floor is treated with chemical hardeners that reduce porosity, while still allowing it to breath, fully-exposed hard aggregates are the predominate wear surface rather than an applied sealer or coating. Correctly selecting aggregates by size, type, and color allows the floor to wear naturally while supporting superior stain resistance to traditional concrete because no film-forming agents are required to maintain a Renaissance floor.
Kroesen estimates that the annual cost of maintaining Renaissance concrete is about fifty-five to sixty cents a square foot, which is typically within a few cents of maintenance costs for terrazzo floors. Compare that to a VTC floor at approximately $1.75 per square foot for maintenance costs, and lower first-costs are quickly absolved by long-term lifecycle costs. Factor in the likelihood of having to completely replace VCT at about 15 years of use verses a 50-year surface with concrete and cost calculations reveal the high-performance, aesthetically superior Renaissance system is a wise investment.
PRE-PLANNING CRITICAL TO SUCCESS
Asked what designers, clients, and general contractors need to know about working with the Renaissance Deep Grind system and Kroesen is quick to answer that pre-planning is critical to success.
“There are a lot of variables that go much deeper than just the finished aesthetics,” says Kroesen. He believes the Renaissance system is ideal in new construction situations, where the building requires a structural concrete slab to be topped with whatever flooring material is specified. Since the structural slab and finished floor become one with the Renaissance system, costs for possibly many different materials are merged into a single line item wherever it is used.
Using it as a complete system, however, does necessitate different thinking on traditional construction sequencing. Typically, a structural slab is poured early in construction before the building is erected above it. It is used and then topped with a finished surface (or polished in the case of decorative solutions) once the threat of construction damage has passed. Pouring the Renaissance system before the building is largely complete leaves the finely composed mix of aggregate concrete vulnerable to heavy equipment scuffs, chemical or gas spills, paint splatter, and other abrasive realities of construction.
“The earlier we can be involved with the designers and owners the better,” says Kroesen. When developing a complete slab and floor solution, the design elevations should account for the finished floor height of all flooring on a level plane and how the concrete slab aligns with the building’s walls. Kroesen shares that often a recessed mud slab is poured, compacted, and used throughout construction as a durable, short-term surface. After the building is erected, the structural/floor slab is poured on top and then polished with Bomanite’s deep grind technique.
“The clients that choose the Renaissance Deep Grind system are making an investment in long-lasting beauty for the benefit of their community for generations to come,” says Kroesen proudly. “This isn’t just work, this is placemaking.”
About the author:
Sean O’Keefe has more than 18 years of experience articulating the complexities, challenges, and camaraderie of construction and design. He writes Built Environment stories for owners, architects, contractors, and product manufacturers and can be reached at sean@sokpr.com.
Modern Contractor Solutions, January 2019
Did you enjoy this article?
Subscribe to the FREE Digital Edition of Modern Contractor Solutions magazine.
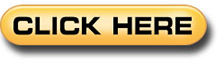