In business there is no substitute for efficiency. Defined by Merriam-Webster as the ability to do or produce something without wasting materials, time, or energy. In large businesses efficiency is an earned commodity. For Uline, North America’s largest distributor of shipping and industrial packaging materials, efficiency is the result of carefully considered, tested, and refined operations involving a complex web of interconnected people, parts, and processes.
NEW DISTRIBUTION CENTER
With more than 22 years in the field and 11 years with Uline, Copenharve recently oversaw construction of a new 1,000,000-square-foot distribution center at Uline’s Wisconsin headquarters. Completed in January 2016, the facility known as W2 is a state-of-the-art distribution center that Copenharve believes is the best organized of all of Uline’s facilities. Since building on past experience is key to efficiency in so many ways, W2 is largely a duplicate of its predecessor W1, including many important design and construction material decisions.
OPEN FLOOR PLAN
One key decision on such a large, open floor plan facility was thermal insulation to guard against Wisconsin’s dramatic annual temperature swings. With summer temperatures reaching into the 90’s and as low minus 40 in the winter, cost-effectively maintaining Uline’s desired working conditions in such a large building relies on premium quality insulation.
“ACH Foam Technologies is one of our customers and we investigated their rigid foam insulation for durability, first-term vs long-term costs, and lifetime R-Value,” continues Copenharve. “We wanted materials that could be installed correctly once and not have to revisit the roof for a long time.”
INSULATION AND R-VALUE
Copenharve notes that ACH Foam Technologies’ Foam-Control PLUS+® and Foam-Control® roof insulation provides a fully warrantied R-value that maintains its effectiveness for 50 years. While other types of insulations may claim higher initial R-values for their products, 3rd party testing has shown that off-gassing occurs over time and reduces the products’ effectiveness. Specifically, polyisocyanurate manufacturers who utilize long-term thermal resistance (LTTR), a weighted average R-value of their product designated over a period of time.
In 2010, Mark Graham, the National Roofing Contractors Association (NRCA) associate executive director of technical services, confirmed that relying on LTTR values for long-term performance may be misleading to designers. “Although the LTTR method of R-value determination and reporting may be appropriate for laboratory analysis, research comparison, and procurement purposes, NRCA does not consider LTTR use to be appropriate for roof system design purposes when actual in-service R-value can be an important aspect of roof system performance.” Expanded polystyrene (EPS) foam insulation, on the other hand, doesn’t suffer from off-gassing and therefore retains the originally specified R-values over the entire life of the product, without change.
LARGEST JOB IN FIRM HISTORY
With high performance expectations established on the W1 project, the task of installing more than 1,000,000 square feet of roofing on W2 fell to SRS Roofing and Sheet Metal of Waterford, Wisconsin.
“SRS is proud to have installed more than 1,000,000 square feet of roofing and received a ‘Perfect’ inspection score from the Carlisle roof inspectors,” declares Tom Bechtel, a commercial estimator at SRS. Founded in 2005, even after 10 years in business, the prospect of taking on the largest job in firm history in a low-bid environment caused some trepidation for SRS.
“You have to streamline crew efficiency to achieve the required production rates, while at the same time making certain that the quality is maintained,” continues Bechtel. “Completing an installation of this size, on schedule, while keeping the quality high enough to earn a perfect inspection score, is impressive.”
Featured Image: The roofing system was put in place section-by-section with all trades being careful not to damage any portion of the roof.
Above: 1,000,000-square-foot distribution center at its Wisconsin headquarters constructed in January 2016.
A MATTER OF LOGISTICS
For the SRS team, streamlining efficiency came down to a matter of logistics. Working closely with general contractor, Mortenson Construction, and other trades to carefully calculate the volume of materials that would be ready at a given time was critical to the project since the building’s envelope was constructed of tilt-up wall panels.
“Logistics played a big role on this project in several ways,” says Bechtel. Determining the right amount of insulation to keep crews moving as quickly as possible was a challenge because there wasn’t room to have a large volume of material stored on site. Fortunately for SRS, they already had an existing relationship with ACH Foam Technologies on previous projects and were able to coordinate a steady flow of insulation to the site with a just-in-time delivery process. To maintain a steady flow of materials, ACH Foam supplied insulation to the Uline jobsite from two of their eight manufacturing locations: Fond du Lac, Wisconsin; and Washingon, Iowa.
PROTECTING THE NEW SURFACE
As the roofing system was put in place section-by-section, the SRS team also had to account for a significant volume of traffic moving across the new surface to reach the other areas still under construction. With 940 skylights installed on the roof, extensive mechanical and electrical equipment, and many other building trades requiring roof access during construction, SRS had to ensure that the newly installed sections were not damaged during construction.
“It was important to avoid even the smallest penetration in the finished roof,” adds Bechtel. “We developed an honor system with subcontractors. If anyone reported damage to the roof, we repaired it immediately for free. If unreported damage was discovered, the costs for the repairs fell to the responsible party.”
ROOFING SUCCESS
With construction completed in January 2016, Uline’s new W2 distribution facility is now fully operational. When it came to building the company’s largest roof to-date, success for both Uline and SRS Roofing and Sheet Metal was the result of careful planning that was efficiently executed. ■
About the Author: Pat Austin is a product specialist with ACH Foam Technologies. For more information about the material used in the roofing project, visit www.achfoam.com.
_________________________________________________________________________
Modern Contractor Solutions – January 2017
Did you enjoy this article?
Subscribe to the FREE Digital Edition of Modern Contractor Solutions magazine.
Performance and Reliability
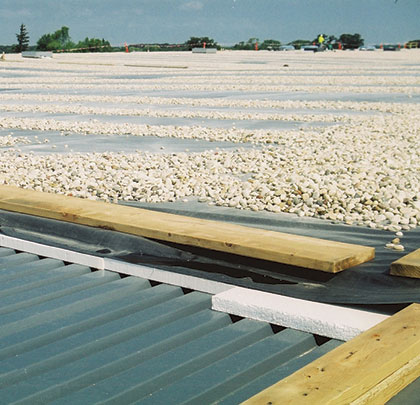