The Construction and Engineering (C&E) sector has been on a stop-start journey throughout the pandemic; the initial lockdown delayed projects and brought tough times for C&E employment. But as infrastructure and housing projects have now begun ramping-up, the scenario has reversed, there is now a concerning human capital shortage to execute these ambitious recovery plans.
HUMAN CAPITAL SHORTAGE
These rapid investments and demands come at a time when the industry is facing a shortage of both materials and human capital. While supply chain shocks have been well-documented across almost every major industry, it’s the shortage of workers that is hitting the C&E sector the most. There are three clear areas where I see new technologies and business models helping close the workforce gap.
1. MODULAR CONSTRUCTION
One of the most innovative ways to ease the pressure of the skills shortage while boosting productivity is adopting an offsite and modular construction model. This trend of building modules or components in a manufacturing facility, and then shipping them to the construction site to be assembled, is increasing in pace and we are seeing many new modular and offsite manufacturing plants being built.
Fundamentally, the rise in this construction model is the result of innovations in the industry. As the trifecta of new materials, more informative data, and technologies become more readily available, they are being applied to improve the quality of these offsite assets—while still gaining the benefits of lower cost, speedier construction, and crucially, less reliance on a large workforce. During the pandemic, it also allowed continued operation of construction companies in a safe, secure, and controlled way.
It’s for these reasons that, at IFS, we expect offsite to become the new normal over the next 10 years. In fact, the U.S. Modular Building Institute agrees this will help balance the need to ramp-up new projects amid workforce pressures. It states, “The modular industry can offer more predictable work locations and hours, less labor-intensive work, a higher degree of technology integration in the workplace, and much safer working conditions. We can serve as a catalyst for the major rebirth of the U.S. manufacturing base, creating thousands of new jobs while addressing our own massive infrastructure needs.”
2. DIGITIZING THE DETAILS
Modular or offsite constructions starts from the ground up and must be executed smoothly not just from design to installation, but also, through to aftercare services. It is in these aftercare services where C&E organizations can boost revenue through continued maintenance or service-based contracts. Enter Building Information Modeling (BIM).
The ultimate end goal of BIM is better information management, which gives project owners a structured set of data they can use to manage a build over its lifecycle. From the request for proposals, to the contract through design revisions, right down to serial numbers on every piece of capital equipment and the size of the bulb for the exit sign, asset data should be structured and well organized. BIM requires that the software underpinning construction projects be data-driven rather than document-driven, so structured data about the asset can flow directly into the systems used to build and manage that asset. This means taking project and operational data out of spreadsheets and into a central, structured environment. The end result is a more connected project environment.
The results are clear to see. The Center for Integrated Facilities Engineering (CIFE) at Stanford University conducted a survey of 32 BIM-assisted projects, and found that the use of BIM technology resulted in: an 80% decrease in the time required to generate an expenditure quote, up to 40% reduction of unbudgeted project changes, savings amounting to up to 10% of the contract value due to timely clash detections, time savings of up to 7%, and cost estimation accuracy within 3%. All of these benefits will be crucial to mitigate the impact of human capital shortages.
3. AUGMENTING HUMAN CAPITAL
There are some positive signs of change in the C&E workforce dynamic. A HBI construction market labor report in fall 2021 found half of payroll workers in construction earn more than $50,460 annually and the top 25% make at least $71,000. In comparison, the U.S. median wage is $49,150, while the top quartile (top 25%) makes at least $67,410. The report also found women make up a growing share of the construction workforce, up to 10.9% in 2020 from the 10.3% in 2019.
The HBI labor report also found the median age of construction workers is currently 41, but digging deeper due to aging trends, the share of construction workers aged 25 to 54 dipped from 72.2% in 2015 to 69.0% in 2019. The industry needs to prioritize change management to encourage younger, more digitally savvy entrants into the sector.
Younger, more innovative C-suite executives are coming, and they should look to technology-led change to see how they can benefit all employees and the future workforce. The technological improvements are ready and available to optimize jobsites with devices such as ring scanners and virtual or augmented reality. BIM principles can incorporate 3D design and there are enterprise solutions available to connect every C&E worker, from the procurement team right through to site managers.
CLOSING THOUGHT
There is opportunity for real and positive change in the current C&E climate, as projects ramp-up due to a once in a lifetime infrastructure and housing demand. But C&E organizations need to address their workforce dynamics in order to capitalize on this revenue potential. Business and technological change is required to continue to close the human capital shortage gap and set C&E organizations up for continued success. The first out of the gate to address human capital will reap big rewards.
About the Author:
Kenny Ingram is VP of C&E with IFS, a world-leading provider of business software for project and asset lifecycle management. Kenny is regarded as one of the top specialists in project-based business systems and has been heavily involved in driving the IFS strategy for nearly two decades. For more, visit www.ifs.com.
Modern Contractor Solutions, May 2022
Did you enjoy this article?
Subscribe to the FREE Digital Edition of Modern Contractor Solutions magazine.
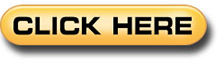