Executives with Zachry Construction Corp. say it didn’t take long to train their crew and hit a good stride with their new Guntert & Zimmerman paver working on a $64 million Interstate project in Columbia, South Carolina.
Zachry recently launched work with the New G&Z S850SL with Dowel Bar Inserter (DBI) by paving sections of 12-inch-thick concrete on Interstate 20 at 18 feet wide. Production in early May was running between 200 and 350 cubic yards of concrete per hour, or between 3,500 and 4,000 feet per day, says project manager Curtis Schwartz.
As a part of the continuing development on the east side of Columbia, the South Carolina Department of Transportation is widening Interstate 20 from two lanes to three on a 6-mile stretch near Interstate 77. First, Zachry will pave an inside lane and shoulder in an 18-foot-wide slab on each side of the four-lane divided highway. Then, in a multi-staged process, the contractor will remove the existing eastbound and westbound lanes and pave two new lanes at 24 feet wide on each side.
VERSATILE AND ACCURATE
The new paver is equipped with both a G&Z DBI and Leica PaveSmart 3D stringless machine control system. The DBI played a major role in Zachry’s decision to buy the new paver, says Zachry’s equipment manager. Originally, Zachry management had planned to pave the I-20 project at 34 feet wide. Management decided to buy the Guntert & Zimmerman machine because of its versatility and the fact that it could be used at desired widths with a dowel bar inserter.
Zachry’s management likes the accuracy of the time tested G&Z DBI design. Tests confirm that the dowel bars meet specification for horizontal, vertical, and skew alignment. Joint spacing is 15 feet for the I-20 project, and the Guntert DBI places the dowel bars right on the money, says Mark Fancella, Zachry’s paving superintendent on the I-20 project.
“I used to be a firm believer in a competing paver,” says Fancella. “But now I’m a Guntert man. I like the side forms on it. You can move them in and move them out. And I like the swing legs. The place where we’re paving now is in really tight quarters. We only had 3 feet on one side, paving up against a median barrier. We just tucked the legs in and we had no problems.”
The AccuSteer System on the Guntert paver permits an operator to turn the tracks 90 degrees and steer the machine sideways. Also, the swing legs can semi-automatically walk into the outboard/transport position to walk the paver directly onto a removable gooseneck trailer. The DBI is equipped with a new patented self-loading system that speeds up the entire loading process.
A FIRST AT ZACHRY
This is Zachry’s first stringless machine control system on a concrete paver. It only took about a week for crews to learn the new Leica system. Thanks to the dowel bar inserter, trucks can dump concrete directly on the grade in front of the S850SL paver with DBI. With the Leica PaveSmart 3D system, Zachry uses three robotic total stations—with two of them active at any time. The Leica system regulates the steering, grade, attack angle, and crossfall of the paver. PaveSmart 3D guides the paver in relation to a digitized 3D model of the highway, running on the onboard machine computer.
The paver is equipped with two, mast-mounted Leica prisms used as tracking targets for the two active robotic total stations. When setting up the robotic total stations, a technician back-sights each of them to five known control points. That fixes the location of the total stations relative to the digital model. The two total stations then follow the movement of the two prisms on the paver and communicate to the machine computer the paver’s precise location via radio link. The machine computer then computes the differences between the paver’s actual location and the digital terrain model. Knowing those differences, the Leica machine computer then instructs the G&Z paver to regulate the steering and grade automatically.
Fancella says it works best to set up the total stations 250 feet in front of the paver. As the machine passes the first total station, the next total station in sequence picks up the paver; this is called “leapfrogging.” The crew moves the first total station around to the front of the paver for the next “leap.” That way the crew and the paver never need to stop—a capability unique to Leica’s technology. Even in traditional stringline paving, stopping the paver is highly undesirable for mainline paving, as it typically introduces a “bump” in the surface, which will count against the ride bonus the contractor is striving to achieve.
It’s absolutely necessary to use an accurate digital model and to calibrate the paver correctly, in order for the stringless control system to work properly, Fancella says. He likes the idea of paving with no stringline. “You can back trucks in directly in front of the paver without worrying about a stringline,” he says. “When you use a stringline, it’s like you’re trapped inside of a room. But with the stringless control system, the paver is out in the open.”
Zachry’s estimators and production personnel considered the investment made for the stringless machine control system, and they see a relatively short return on investment. Far less surveying and staking is required with the stringless control system. Plus, the stringless system is safer—nobody worries about tripping over a stringline or breaking it.
Zachry management visited the G&Z factory, and they were impressed with G&Z’s manufacturing process. “Guntert puts a lot of time and effort into the precision of the machine,” says the equipment manager. “And I just felt like it was going to produce the product that we have to pave today.” ■
For More Information:
For more information about G&Z, visit www.guntert.com.
_________________________________________________________________________
Modern Contractor Solutions, December 2013
Did you enjoy this article?
Subscribe to the FREE Digital Edition of Modern Contractor Solutions magazine.
Paving With Precision
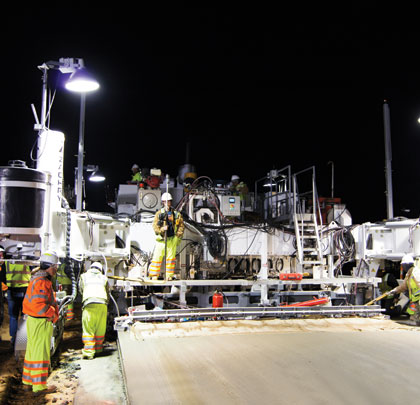