Upgrade as technologies advance for safety monitoring
By Chris Holbert
Workplace injuries are the enemy of productivity and employee satisfaction. If a worker is forced to miss days of work due to injuries on-the-job less work is getting done, the company risks increased insurance rates and potentially missed deadlines as well. According to the National Safety Council, construction workers are at high risk for workplace injuries. This industry is among the top five for occupations with the highest number of workplace injuries resulting in days away from work. Lone workers who execute their duties outside line of sight and beyond hearing range of coworkers and supervisors are not only at risk for injury, they could be placed in a situation where their injury and need for help may go unnoticed for an extended period of time.
TECH TO MONITOR
In recent years many construction businesses have begun to use wearables and mobile technologies to monitor worker location, health indicators, and environmental conditions. Everything from hard hats to safety vests have been infused with technologies that can alert a supervisor or safety manager when an accident occurs or working conditions are putting workers’ health at risk. Workers have also been supplied with a technology similar to that which has been relied on for years to ensure the safety of senior citizens, Mobile Personal Emergency Response Systems. These devices, also known as SOS or panic buttons, can be activated with the press of a single button or an alert can be triggered by a fall. They function as two-way speaker phones and can directly connect workers with emergency response. In many situations they can be a lifeline for workers and help mitigate the repercussions of an incident.
INFRASTRUCTURE UPGRADE
The value of these personal safety monitoring technologies is priceless. However, the technology could become unreliable as telecommunication companies upgrade cellular networks from older 2G and 3G technologies to accommodate next-generation 5G services.
Many panic buttons were designed using 3G or even 2G technologies because the data being transferred by the device is light and doesn’t require the higher speeds of a 4G network, let alone 5G. As networks are upgraded 2G and 3G devices could lose coverage and become unreliable. This is because telecom companies will be trading out the 2G and 3G technologies on cell phone towers for faster 4G and 5G technologies. Panic buttons operating on 2G or 3G networks will not be compatible with the new network speeds and their functionality could experience drops in coverage in areas where 2G and 3G coverage no longer exists.
DEVICES TO MEET DEMAND
Ericsson, an information communication technology company that installs 5G technologies on cell phone towers, predicts that by 2023, 20 percent of the world’s population will have 5G coverage. While this will infinitely speed up heavy data transfers like streaming video, the problem that exists for the mPERS industry and end users is that 4G devices have yet to be introduced to the mass market, let alone 5G.
The basic functionality of panic button devices has not required rapid advancement of the technology that powers their operation. This and other factors affecting the mPERS industry have resulted in a device drought. There hasn’t been a lot of hype about upgrading mPERS devices in the past because more advanced 4G models have simply not been available to sell. Now, manufacturers are forced to catch up with changing networking standards in order to continue to provide the safety and peace-of-mind customers rely on from their devices.
UPGRADE, TEST REGULARLY
Individuals who rely on mPERS devices to ensure their safety and well-being need to know their devices will become unreliable as network upgrades are made. This can be accomplished by contacting the device manufacturer or the company providing monitoring services for the device. If a construction company discovers its devices are operating on 2G or 3G networks, it would be wise to upgrade the panic buttons as soon as possible. Discuss options with service providers to turn in existing devices for 4G/LTE models. Construction companies that have panic buttons in the field may also want to consider implementing a regular testing schedule to ensure the devices are operational and have coverage at all jobsites. Each time a project begins at a new site, one device could be triggered to ensure that SOS messages are being transmitted. This simple test would only take a few seconds and would quickly determine if backup safety measures need to be taken or if the panic buttons can be relied on at that location. Companies may find that jobsites in more rural areas will continue to have 2G or 3G coverage, while jobsites in urban areas will lose coverage sooner. This is simply because of the tendency for telecom companies to upgrade towers in urban areas with dense populations and large business centers first.
Transitioning from 2G or 3G panic buttons to 4G/LTE devices could come with an added cost. But it is an essential upgrade to ensure ongoing protection for employees. Upgrading devices could also give employers access to new device features that will make it even easier to monitor employee safety.
CLOSING THOUGHT
In order to continue to provide employees with a safe working environment, employers will need to investigate what networks the panic buttons already issued to workers operate on and if necessary, upgrade them. Upgrading to a 4G/LTE mPERS device will guarantee that coverage is available for workers anywhere there are cell towers. 4G devices will be backwards compatible, so even in areas where 2G and 3G have not yet been upgraded to 4G or 5G coverage will still be complete. Making sure that employees have the latest safety technologies available to them will help construction companies maximize productivity while illustrating to workers that they are valued by their employer.
About the author:
Chris Holbert is the CEO of SecuraTrac. As the CEO, he is responsible for leading the company’s vision of developing, marketing, and selling a suite of mobile health and safety solutions that bring families closer together and improve employee safety through state-of-the-art location-based services and mobile health technology. For more, visit www.securatrac.com.
Modern Contractor Solutions, February 2020
Did you enjoy this article?
Subscribe to the FREE Digital Edition of Modern Contractor Solutions magazine.
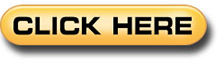