The ever-evolving construction industry landscape forces contractors, design-build firms, and design professionals to seek innovative ways to enhance efficiency, reduce costs, and remain competitive in a global marketplace. One strategy that has gained significant traction in recent years is the outsourcing of design, manufacture, and fabrication services to foreign firms. This approach offers the promise of cost savings, access to specialized expertise, and accelerated project timelines. However, the complex web of risks, rewards, and dangers for outsourcing demands careful consideration.
PROMISE OF OUTSOURCING
Outsourcing holds a tantalizing promise for construction professionals, with cost savings often the primary factor. Overseas firms can offer competitive pricing due to lower labor and operational costs, making it an attractive proposition for those looking to optimize budgets. Moreover, outsourcing provides access to specialized expertise that may not be readily available domestically. This expertise can range from architectural design and engineering to cutting-edge fabrication technologies. Another compelling advantage is the potential for accelerated project timelines. By leveraging a work cycle that global outsourcing facilitates, construction firms can significantly reduce project duration. However, these promises do not come without risk. The decision to outsource carries with it a complex set of challenges and potential pitfalls that, if not navigated carefully, can lead to adverse consequences.
PERILS OF OUTSOURCING
One of the foremost concerns when outsourcing design and fabrication services is integrity of process. Construction projects in the United States are governed by numerous regulations, codes, and standards that ensure safety, quality, and compliance with local laws. When outsourcing to foreign firms, there is a legitimate concern about adherence to U.S. construction standards. Failure to do so can result in subpar workmanship, safety hazards, and even legal liabilities. To address this risk, construction professionals must engage in rigorous due diligence before entering into outsourcing agreements. This includes thoroughly vetting overseas firms, verifying their track record, and ensuring they possess the requisite expertise and commitment to adhere to U.S. standards. Additionally, robust quality control processes and ongoing monitoring of overseas partners are essential to maintaining the integrity of the construction process.
CONFIDENTIALITY/OWNERSHIP
The confidentiality of project data and security of intellectual property is another critical concern when outsourcing design and fabrication services. Construction projects often involve proprietary designs, innovative technologies, and sensitive client information. The risk of this information being compromised during outsourcing can have severe consequences, including damage to reputation and legal disputes. To mitigate this danger, construction professionals must establish clear contractual agreements that explicitly address confidentiality and intellectual property rights. These agreements should define the scope of confidentiality, outline penalties for breaches, and establish mechanisms for dispute resolution. Moreover, it is advisable to work with legal counsel experienced in international construction contracts to ensure robust protection of intellectual property.
The ownership of design and fabrication documents created by foreign firms can become a complex legal quagmire. Determining who owns these documents and whether they can be used for subsequent projects or modifications can be a source of disputes. It is crucial to address this issue explicitly in outsourcing contracts to avoid ambiguity. Construction firms must establish clear terms regarding ownership, usage rights, and the transfer of intellectual property in their contracts with foreign partners.
SUPPLY CHAIN DISRUPTIONS
Recent global crises, such as the COVID-19 pandemic, have highlighted the vulnerabilities of supply chains in the construction industry. When relying on overseas suppliers and fabricators, construction professionals expose themselves to the risk of disruptions caused by political instability, natural disasters, or unforeseen global events. To counter this danger, it is advisable to diversify the supply chain by sourcing critical components or materials from multiple suppliers or regions. Additionally, construction firms should have contingency plans in place to respond swiftly to supply chain disruptions, ensuring that projects can continue without significant delays.
MITIGATING RISK
The cornerstone of any successful outsourcing venture in construction is comprehensive due diligence. Before entering into agreements with foreign firms, construction professionals must conduct extensive research and evaluation, a process which should include thoroughly vetting potential overseas partners to assess their financial stability, track record, and reputation within the industry, contacting previous clients and projects of the foreign firm to gain insights into their performance, adherence to standards, and ability to meet project deadlines, and, if possible, visiting the facilities of potential overseas partners to evaluate their capabilities, quality control processes, and commitment to safety. Legal counsel should be involved to draft and review any agreements put into place, and local lawyers in the foreign trade partner country may need to be consulted.
Once an outsourcing agreement is in place, construction professionals must implement robust quality control processes and continuous monitoring to maintain the integrity of the construction process. This includes developing comprehensive quality assurance plans that outline the specific standards, testing procedures, and inspections required at various project stages, engaging third-party inspection firms with expertise in the relevant industry to conduct independent assessments and verify compliance with U.S. standards, and performing regular audits of the overseas partner’s facilities and processes to identify and address any deviations or deficiencies promptly.
At the heart of most construction issues, good communication is essential. Establishing open and transparent communication channels with foreign partners to facilitate the rapid resolution of any issues that may arise is essential. To protect against contingencies, construction professionals should consider evaluating insurance options, including professional liability insurance, to provide financial protection in the event of disputes or liabilities stemming from outsourcing arrangements. Legal options for seeking recourse in the event of contractual breaches, intellectual property theft, or other legal disputes, both domestically and internationally, should be in place, so they do not have to be spun up in an emergency.
CLOSING THOUGHT
In conclusion, the perils of outsourcing in the construction industry should not deter professionals from realizing its benefits. Instead, they should serve as a call to action for meticulous planning, due diligence, and the implementation of risk mitigation strategies. By diligently selecting partners, crafting ironclad contracts, instituting rigorous quality control, and proactively addressing legal and insurance matters, construction professionals can navigate these perils and unlock the true potential of outsourcing.
About the Author:
William Thomas is a principal at Gausnell, O’Keefe & Thomas, LLC in St. Louis, where he focuses his practice on construction claims and loss prevention. He is an AAA Panel Arbitrator, Fellow with the Construction Lawyers Society of America, and member of the International Association of Defense Counsel, serving on its Construction Law Committee. He also is a member of the ABA Forum on Construction, AIA, and ASCE. He can be reached at wthomas@gotlawstl.com.
Modern Contractor Solutions, December 2023
Did you enjoy this article?
Subscribe to the FREE Digital Edition of Modern Contractor Solutions magazine.
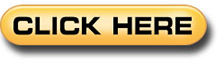