Full-depth reclamation strengthens rural roads for heavy-truck traffic.
Drilling for natural gas in the Marcellus shale region of northern Pennsylvania has increased traffic of heavy loads on small rural roads. Because of the depth and nature of the gas-rich shale formation, hydraulic fracturing is being used to release the gas. Each 5-acre drill pad requires about 1,500 trips of 80,000-pound water trucks to open the first well, and 1,000 trips for each additional well. A pad can support up to eight wells.
HEAVY ROAD TRAFFIC
At the Marcellus Center for Outreach and Research, engineers have estimated that one 80,000-pound water truck is the equivalent of 9,500 to 10,000 cars. And in the state with the most annual freeze-thaw cycles, annual maintenance has always been a struggle.
This new, heavy-truck traffic has far exceeded the design of the rural roads, resulting in severe damage, and requiring more than just a new layer of asphalt.
With funding from gas providers like Chesapeake Energy and specifications from PennDOT, the repairs called for full-depth reclamation (FDR) to recycle the existing roads into a stronger base than the original.
FULL-DEPTH RECLAMATION
EJ Breneman (EJB) of West Lawn, Pennsylvania, contacted Stoltz Site Spreaders of Morgantown, Pennsylvania, to put together a fleet of Stoltz truck and trailer spreaders to take on a 300-mile repair project.
All together, enough equipment was fabricated and rented to supply seven crews to run separate FDR jobs, all overseen by John DeMartino and Dean Etchberger of EJB.
In Susquehanna County, Pennsylvania, EJB used a two-step FDR process. First, the old road surface and base were ground and shaped. Second, cement is spread on top of the recycled base. Then the cement and the old road are both ground up again and compacted to form a base for a new 8-inch asphalt surface.
The repairs on small, rural roads due to heavy-truck traffic called for full-depth reclamation (FDR) to recycle the existing roads into a stronger base than the original.
ISSUE OF DUST
Whether the road work was in deep forest or along inhabited areas, dust is the major issue. The Pennsylvania Department of Environmental Protection (DEP) monitors the air and water impacts of the drilling. Airborne cement dust, although intermittent and a moving point source, was the primary issue with the road work. Cement dust was released when filling a spreader from a bulk tanker truck, and while spreading the cement on the old base ahead of the reclaimer.
DEP could, and did, order the removal of spreaders lacking sufficient dust controls. According to John DeMartino of EJB, “Although other contractors were shut down due to excessive dust, the Stoltz spreaders basically became the standard against which other spreaders were measured.”
The Stoltz Site Spreaders used either popup filter bags, or a filter can with keeny tubes to prevent dust while filling from the bulk tankers. Front and rear conveyor chain seals respond to the inload pressure to further seal the hopper.
Dust control while spreading is primarily controlled by heavy-duty dust curtains to control dust splash back and wind drift. In more dust sensitive situations, a spray system is used to suppress fugitive dust.
BENEFICIAL SOLUTION
In a presentation given to the Marcellus Center for Outreach and Research, Tim Ziegler of the Center for Dirt and Gravel Road Studies at Penn State points to additional advantages of FDR. First, the new base is dust free while awaiting paving, and second, the new road is only inches higher than the old base. By not adding height, the new road does not increase the runoff impoundment from heavy rains. ■
Reference: www.marcellus.psu.edu
For More Information:
For more information about Stoltz Mfg., LLC, visit www.stoltzmfg.com. For more information on EJ Breneman LP, visit www.ejbreneman.com.
_________________________________________________________________________
Modern Contractor Solutions, June 2013
Did you enjoy this article?
Subscribe to the FREE Digital Edition of Modern Contractor Solutions magazine.
Overhaulin’ the Roads
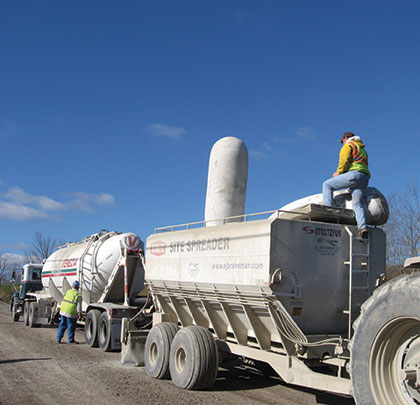