In the congested South Boston area, streets are small and space is tight. Long known for its hardworking Irish residents, South Boston is now experiencing an influx of young professionals and subsequent development boom. As a result, parking has become a significant challenge. One example of a creative solution to the South Boston parking challenge is found in the Gate of Heaven Condos project.
Formerly the Gate of Heaven Elementary School owned by the Gate of Heaven Parish, the building is being redeveloped into a high-end condominium building. The parking solution for the condos was found within the footprint of the building by creating a parking structure underneath the existing building rather than finding another property or tearing down an existing structure to make space. Hoffman Concrete Construction of Dracut, Massachusetts, was contracted for the concrete portion of the project, and work began in early 2013.
Lead Photo: Hoffman Concrete crew makes last minute adjustments prior to the initial footing pour. You can see that the excavation is 6+ feet below the existing granite slab foundation and the concrete pump lines along the ground. The image also shows that the initial plan only allowed for the undermining of 6 to 8 feet of the existing foundation.
Above Photo: The one-sided formwork is in place with the soldier beam bracing system secured to the footing.
CHALLENGING ONE-SIDED POUR
The foundation wall for the underground parking was formed for a “one-sided” pour. In addition, underpinning was required, increasing the project’s technical challenge.
The building’s existing granite block foundation extended 6 to 8 feet underground. To obtain enough head room for parking below the ground-level floor, crews not only had to excavate 8 feet, they had to excavate another 6 to 10 feet below, totaling 18 feet. When crews reached the 18-foot depth, there was no structural support for the building. As such, the new one-sided concrete wall serves a twofold purpose: to shore up the existing foundation and to support the new steel framework required to accommodate the retrofit. Hoffman Concrete brought in A.H. Harris & Sons to provide service, solutions, design, and materials for forming, anchoring, and reinforcing the project.
SPECIAL MATERIALS REQUIRED
A.H. Harris provided a variety of specialized materials for the project, as well as engineering and on-site service for the pour. Before the one-sided walls were poured, A.H. Harris supplied a MiraDRAIN drainage board to be installed behind the new foundation. The drainage board will collect and divert any groundwater that might present itself after concrete was poured.
Next, A.H. Harris provided solutions for streamlining the assembly and movement of equipment necessary for the underpinning and one-sided pour. A gang-form system comprised of Harris Ply hand-set forms, adjustable Soldier Beam bracing, and epoxy anchors met the project’s needs. After examining the drawings and existing conditions, A.H. Harris engineered a forming system that allowed Hoffman Concrete Construction to set up the wall and pour it safely, while minimizing the amount of components necessary.
The gang-form system allowed the contractor to move quickly, minimizing manual labor and time required for the project. With this system, Hoffman’s crews stripped 12 to 24 feet of wall at one time and reset without dismantling all the components. The A.H. Harris-designed no-tie anchor system and components allowed the contractor to anchor to newly poured footings and to capture and stabilize the loads the formwork created. Because one-sided pours generate heavy liquid and directional loads, the smallest shift could create dangerous conditions or destroy the formwork. A.H. Harris’ engineers reviewed the loads, carefully considered safety, and designed the system to prevent any movement or shifting from occurring.
A pour is finished and the formwork is in place for the next pour. This is a 24-foot long by 14-foot high section of wall that was able to be stripped in one piece and moved into place with equipment.
ON-SITE SUCCESS
When the project was underway, careful coordination among all team members was critical to the project’s success. A.H. Harris’ worked closely with Hoffman’s crews to facilitate safety and efficiency. On-site guidance was provided by local A.H. Harris forming and shoring representative Mark Fernandes, who worked hand-in-hand with Hoffman’s crews. Crews poured more than 900 cubic yards of concrete with a trailer pump, which remained outside the building, and pump lines were laid inside the building to reach the pour area. A.H. Harris provided and fabricated more than 15 tons of rebar for the project.
Once the project was underway, work moved quickly and Hoffman realized they could move faster than they anticipated due to the forms’ performance. Original plans called for pours to be 6- to 8-feet long by 16-feet high. After the first two pours, Hoffman expanded to pouring 12- to 18-foot-lengths by 16-feet high. As the general contractor saw that Hoffman’s work was moving faster than expected, they were able to excavate ahead more quickly. A.H. Harris supplied more formwork to the project to accelerate the progress. More than 20 concrete placements were made over 2½ months.
Further expediting the project was the nearby location of A.H. Harris’ South Boston facility, a couple miles from the Gate of Heaven Condo project. With the close proximity of the materials supplier, A.H. Harris stored additional materials at their location and provided same-day delivery as needed. A.H. Harris delivered the materials in the early morning to avoid traffic. As such, the contractor didn’t have to hire police traffic details for loading and unloading.
Developers anticipate completion of the Gate of Heaven Condos by early 2014 or sooner. With the revitalization of South Boston expected to continue in the coming years, in part because available land still remains along the highly desirable waterfront, more developments may rely on the underground, one-sided pour under existing buildings to meet the growing demand for parking. ■
About the Author:
Dan Clark is an account manager with A.H. Harris & Sons, Inc., a construction products distributor founded in 1916 with more than 40 locations in the New England, Mid-Atlantic, and Southeast Regions. A.H. Harris serves the heavy and highway, commercial, industrial and residential markets, specializing in areas of concrete formwork and accessories, rebar fabrication, concrete repair and restoration, geotextiles, and erosion control. For more information, visit www.ahharris.com.
_________________________________________________________________________
Modern Contractor Solutions, January 2014
Did you enjoy this article?
Subscribe to the FREE Digital Edition of Modern Contractor Solutions magazine.
One-sided Pour Creates Parking Under Existing Building
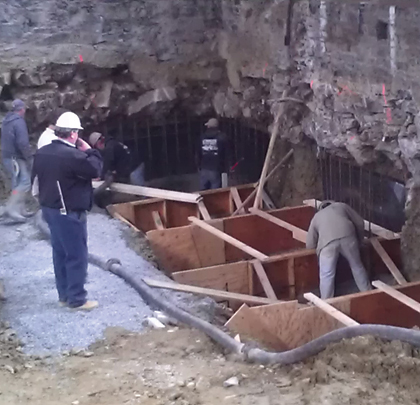