Contractors need to pay extreme attention to detail in the construction of cold storage facilities. The buildings are unique, and the smallest error or lapse in judgment or workmanship can result in spoiled food—and a serious problem for the business owner.
Tippmann Innovation, one of the national leaders in the construction of cold storage facilities, completed construction of a new facility in June 2018 for Dick Cold Storage in Columbus, Ohio. The new facility includes the state-of-the-art equipment, including the latest in fire protection technology. Dick Cold Storage contracted to work with Tippmann Innovation after a fire destroyed the previous DCS building in 2016.
“We were surprised at how quickly the team at Tippmann Innovation was able to meet with us after the fire,’’ Company President Don Dick says. “Their combined expertise and experience allowed us to immediately begin making plans to replace our warehouse. The upgraded technologies in the new facility allow us to have peace of mind about the future growth and safety of the warehouse.”
A BUILDING DESTROYED
Don Dick remembers watching the blaze rip through the building. The fire started around 9 p.m.—no cause has been determined—and firefighters were on the scene within minutes. “At that time, you’re completely lost,’’ Dick says. “You have no idea what will happen to your business.”
More than 400 firefighters fought the raging blaze. There was very little, however, that they could do. The building did not include rooftop smoke vents, which made fire containment efforts perilous. Firefighters could do little more than watch the fire burn itself out, which did not occur for another 18 hours.
“Two of the biggest challenges we face in fighting any fire are heat and smoke,’’ says Steve Martin, Battalion Chief for the Columbus Fire Department. “The heat of the fire radiates on everything surrounding it, causing the flames to spread and rapid degradation of structural elements.”
Smoke vents may not have prevented the fire. They would have, however, allowed firefighters to aggressively tackle the blaze. Some portions of the structure might have been saved if smoke vents had been in place. If firefighters had been able to discover the origin of the fire, they could have been aggressive in their containment efforts.
“Buildings that do not lend themselves to ventilation, such as cold storage buildings, are especially dangerous to firefighters. If there is no known life-safety issue, firefighters will retreat to a defensive position and fight the fire from outside the building instead of going inside,’’ Martin says.
The fire destroyed the building. Shortly afterwards, the Dick business leadership contracted with Tippmann Innovation to build a new facility.
ENHANCED FIRE PROTECTION
Tippmann Innovation worked with Dick’s team to install more fire safeguards in the new structure. They include fire access doors, horns, strobes, pull stations at doors and linear heat detection in freezers. The new building also includes automatic smoke vents.
“It was essential for us that we have fire protection throughout the building,’’ Dick says. “That was one of the key considerations for us in our new building.”
Dick Cold Storage executives included smoke vents in its new building. Manufactured by The BILCO Company, the custom-made vents measure 7-feet by 18-feet and include a quad leaf design. Tippmann Innovation worked with Spohn Associates to procure 18 custom-made smoke vents. The vents allow for the escape of smoke, heat, and gasses in a burning building.
The vents include a Thermolatch® II positive hold/release mechanism that ensures reliable operation when a fire occurs. It also automatically releases vent covers upon the melting of a 165 degrees Fahrenheit fusible link. Gas spring operators are designed to open the covers against snow and wind loads and include integral dampers to assure that the covers open at a controlled rate of speed.
The size of a building, among other factors, determines the number and size of vents required for a building. The vented space must comply with fire codes.
“Vents will allow for the removal of heat and smoke will potentially slow the spread of fire,’’ Martin says. “They will also permit firefighters to see and enter the building, to possibly extinguish the fire early, preventing the entire building from becoming a loss.”
ROOFING COMPONENTS
The smoke vents are part of a sophisticated and elaborate roofing system to ensure protection within the building.
Cold storage facilities are used for keeping food products and other perishables for distribution to supermarkets and other retail outlets that sell to consumers. Dick Cold Storage’s Columbus location serves customers in a 550-mile radius, covering a geographic area that reaches Wisconsin, Alabama, and New York and a population of more than 138 million people.
Improper or inefficient roofing materials can have disastrous consequences for cold storage buildings. Side effects could include structural damage from ice buildup on walls and slabs, higher utility costs, safety issues for workers, and equipment that may require more maintenance or not reach its expected lifespan. The most important objective was constructing a vapor-tight barrier.
Tippmann used a single-ply roofing system with 45-mil and 60-mil TPO. Single-ply systems minimize air leaks, which can lead to thermal loss and excess moisture.
SPACIOUS SURROUNDINGS
The new facility includes 50-foot clear ceilings, six million cubic square feet of storage space and seven multi-temperature storage rooms. The building can accommodate 15,000 pallets.
“In the cold storage industry, it’s not so much about square feet as it is about cubic space,’’ says Rob Adams, a partner at Tippmann Innovation who helped design the new building. “It’s about getting pallet positions. You want to maximize square footage, so you generally build higher instead of vertical. You’re refrigerating the same footprint. It’s significantly more costly to build a refrigerated building.”
The new facility includes LED lighting, frozen, cooler and dry storage, and the most energy-efficient refrigeration equipment. Adams said there are seven rooms that can be used for either refrigerated or frozen storage.
For the Dick family, the most important aspect was to get back to business as usual. With the new building and upgraded fire protection, Dick feels the business is in a strong position to serve its clients for years to come. “Tippmann Innovation’s experience and reputation in cold storage building are well-known and respected,’’ Dick says. “We’re confident that our new facility will be at the cutting edge of cold storage innovation.”
About the author:
Thomas Renner writes frequently on building, construction, and manufacturing for United States trade publications.
Modern Contractor Solutions, December 2018
Did you enjoy this article?
Subscribe to the FREE Digital Edition of Modern Contractor Solutions magazine.
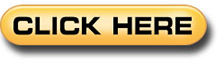