Split slab construction is an efficient way to manage water infiltration in plazas, elevated office patios, planters, and sidewalks. If installed by an experienced specialty contractor, waterproofing between the topping and structural slabs can provide years of protection against damaging moisture. Unfortunately, when waterproofing is not applied correctly using this construction method, leaks can occur, and when they do, the traditional method of repair is costly and disruptive to building owners and their tenants.
TRADITIONAL REPAIR METHOD
Specialty repair contractors encounter many scenarios where a split slab is actively leaking, such as building plazas, elevated office patios, planters, sidewalks, and more. After surveying the damage the leak is causing, the conversation with the building owner inevitably focuses on making repairs. Up until now, the repair process consisted of removing the topping slab and existing waterproofing membrane, then applying a new coating or patching the existing system in place, then finally pouring a new topping slab or installing a different finish, such as paving stones.
FINANCIAL IMPACT
The entire repair process can be complicated and cumbersome, particularly in public spaces with heavy pedestrian and vehicular traffic. In certain applications where the split slab is part of a roof, the repair process becomes extremely difficult and expensive.
In repair areas located in tenant leasable space, the owner may have to negotiate some sort of rent reduction in order to compensate for any inconvenience or loss of revenue that the repair may cause the tenant. In high vehicular traffic areas, a split slab repair may limit or eliminate access to revenue-generating parking areas.
Considering all of the potential, negative financial aspects of a traditional split slab repair, compounded by the noise, disruption, cost, and dust resulting from the actual work, the traditional method is no longer a viable option.
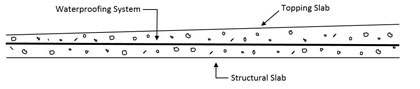
NEW APPROACH TO SPLIT SLAB REPAIRS
Western Specialty Contractors’ new, less invasive repair method eliminates the disruption of a traditional repair. By utilizing a customized plural pump, Western is able to inject Gelacryl Superflex chemical grout from De Neef® between the split slabs to make the repair, without having to remove the topping slab.
Superflex is a unique blend of methacrylic acrylate copolymers that has the low viscosity of traditional acrylate resins with the elongation and adhesion properties typically associated with polyurethane resins. Its low viscosity makes it ideal for injection into split slab applications.
Superflex’s low surface tension also makes it suitable for penetration around existing membranes. It is certified to NSF/ANSI 61 for potable water use, which assures not only drinking water quality, but adherence to strict auditing of manufacturing quality standards. Superflex polymerizes to form a resilient, highly elastomeric gel with elongation greater than 300 percent.
GROUTING PROCESS
The process begins by identifying the repair areas using a flood test, making sure to isolate the areas so as to eliminate certain variables. The repair area is identified by starting at the actual area of the leak and working upwards and out. Recognizing that water will travel via the pan decking, the actual perimeter of the repair area can then be calculated. Once the repair area is identified, additional factors must be determined, such as topping slab thickness and type of existing membrane using a core sample if necessary, and, as always, a pH test of the leaking water. Your local De Neef representative is available to assist with this process. Once these project-specific answers are determined, a comprehensive repair plan can be developed.
Generally, the repair process follows a prescribed path of setting a perimeter around the repair area using De Neef Flex SLVPURe grout to provide containment for the actual Superflex grout. This will ensure that the area in question is covered adequately.
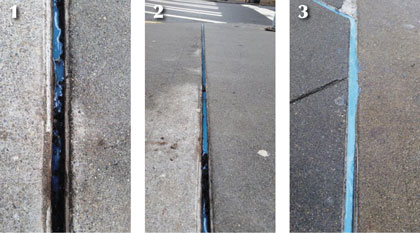
Photo 1 & 2: These images show the Superflex material beginning to travel through the split slab.
Photo 3: This photograph shows the cured Superflex the following day after it had traveled through the split slab and cured.
SLAB INJECTION PROCESS
The slab injection process is similar to a curtain wall injection, only on a horizontal surface using injection ports customized for this process. Prior to the injection process, the team will need to verify that the grout’s catalyst time is equal to the time needed for travel between the topping and structural slabs.
The injection team then moves across the identified repair area in a methodical way to ensure coverage. When injected through port holes drilled in the topping slab, the Superflex grout travels throughout the perimeter of the injection area, filling in any voids between the slabs to adhere, set, and cure.
Once the injection process is complete and after all of the grout has catalyzed, flood tests are performed. This process takes place after 15-20 minutes and can last 20-30 minutes.
If no additional leaks are detected, work begins to patch the port holes using a polymer-modified patching mortar or a product that matches the topping slab materials in color and/or texture.
CONCLUSION
A distinct advantage of the De Neef system is the ability to customize the timing process. Western has been able to mix batches with very short catalyst times, up to several minutes, depending on the project requirements. This timing determines how long the Superflex remains a liquid before it gels, and this is done to determine and verify coverage. Performing cup tests, while timing the grout, is essential to verify that the Superflex will cure within the needed time. Once the project team has verified that the catalyst time is equal to the time needed for travel in between the topping and structural slabs, the simple injection process can begin.
For the building owner, the benefits of Western’s split slab repair technique are clear. With little to no disruption to tenants, pedestrians, and vehicle traffic, and no dust or noise generated during the repair, leaking plazas, patios, planters, sidewalks, and more can now be repaired with ease.
About the Author
David Kimble is a branch manager (Seattle) with Western Specialty Contractors. Family owned and operated for more than 100 years, Western Specialty Contractors is the nation’s largest specialty contractor in masonry and concrete restoration, waterproofing, and specialty roofing. Western is headquartered in St. Louis, Missouri, with more than 30 branch offices nationwide. For more information, visit www.westernspecialtycontractors.com.
_______________________________________________________________________
Modern Contractor Solutions, June 2017
Did you enjoy this article?
Subscribe to the FREE Digital Edition of Modern Contractor Solutions magazine.
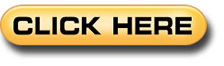