By Rick Farrell
Construction is a noisy business. The average noise levels measured for various construction-related tasks range from almost 96 dbA for installing trench conduit to more than 102 for chipping concrete. And, the maximum measured noise exposure for many such tasks can be as high as 120 dbA. This creates at least two sets of problems: potential issues in terms of worker safety from direct exposure to unhealthy noise levels and difficulty in communication—which creates ripple effects in terms of additional sets of issues, including indirect reinforcement of other risks to worker safety.
DIRECT THREATS TO SAFETY
The Center for Disease Control warns that damage to hearing can occur after just 2 hours experiencing anything above 80-85 decibels. At 100 decibels the critical window for safety falls to only 15 minutes. And the threshold for pain and injury is 120 dbA. This means that even the lowest noise levels associated with various construction tasks can cause hearing impairment, or worse. Of course, ear plugs and other hearing protective devices (HPDs) are effective in reducing the potential for hearing problems. But workers resist wearing these for a variety of reasons, as we’ll discuss shortly.
COMMUNICATION CHALLENGES
The second set of problems relates to difficulty in communicating. Collaboration is critical for many reasons on any project, and there is no collaboration without clear communication. In the planning and design phases, collaboration is made far easier by increasingly sophisticated technology, ranging from BIM software to augmented reality. But while these technologies also have a role on the site itself, there is no substitute for direct person-to-person interaction when and where the work is being done, especially when unanticipated situations require adjustments on the fly. Yet noise is a huge hindrance to communicating. And in a physically challenging environment like a construction site where the potential for injury is high—loads can slip, seemingly stable footing can suddenly become unstable—a missed warning could lead to a serious injury.
The irony here is that, in the eyes of many workers, the solution to the first problem often makes the second problem worse. Just as surely as the noise levels on a typical site create communication problems, wearing HPDs can make it difficult to hear fellow workers or supervisors. Collaboration remains hindered. Meanwhile, the benefits of preserving one’s hearing may pale in comparison to the potential for a more serious injury thanks to the lingering inability to communicate. As a result, many construction workers resist wearing hearing protection.
HEADSET SYSTEMS
In fact, construction employment doesn’t mean a worker has to make trade-offs between the risks of hearing damage on the one hand and the potential for an even more debilitating injury on the other.
The solution to many of these challenges lies in use of staff communication systems. These are built around two core components, headsets and transceivers, that enable the wearers to overcome barriers to communication—not only the ambient noise of a construction site, but distance as well. The elimination of this latter barrier can be particularly important in avoiding injuries. The sudden emergence of a potentially dangerous situation or even the immediate threat of an accident is often clearer to those viewing the scene from a distance. An operator sitting high up in the cab of an excavator, for example, can take in the whole picture in a way the people comprising that picture cannot. And when everyone is equipped with headsets and receivers, he can warn of rapidly encroaching threat at least as quickly as a co-worker standing shoulder-to-shoulder with the person in danger.
CLOSING THOUGHT
Some of the drawbacks of impaired communication are direct and obvious, and others are the result of ripple effects and perhaps less obvious. None would deny that clear communication is critical in any job taken on by two or more individuals, at minimum for simple reasons of efficiency. Yet while injury prevention may not come to mind as a primary benefit of communication for most people, it’s top-of-mind for many who are regularly exposed to the risk of injury. Their embrace of a technology to address their concerns will determine whether or not that technology is ultimately adopted and successful. A staff communication system is more than likely a solution the large majority will embrace.
About The Author
Rick Farrell, president, Plant-Tours.com, is North America’s foremost expert in improving manufacturing group communication, education, training, and group hospitality processes. He has more than 40 years of group hospitality experience, most recently serving as president of plant-tours.com for the last 18 years. He has provided consulting services with the majority of Fortune 500 industrial corporations improving group communication dynamics of all types in manufacturing environments. Plant-tours.com manufactures the most reliable, easy to use, highest quality headset communication systems for the manufacturing, industrial, and institution markets.
Modern Contractor Solutions, May 2021
Did you enjoy this article?
Subscribe to the FREE Digital Edition of Modern Contractor Solutions magazine.
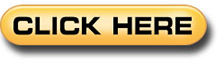