By Debra Hilmerson
Two-by-four and lightweight steel construction safety guardrails are gradually becoming things of the past as more general contractors adopt more durable systems that are simpler to use, inventory, store, and transport; easier on the environment and have an impressive ROI.
The future belongs to reinvented guardrails that solve many chronic problems. Wood rails take time to build, are challenging to make OSHA-compliant, and get tossed at the end of the job. Lightweight steel rails bend, crack, and rust. People on jobsites love the more durable reusable guardrails because of the gained efficiencies. They are safer, faster, and simpler to install.
Industry people kept asking for a better solution but options were limited. So, we spent 2-½ years talking with industry-leading contractors, foremen and tradespeople to determine what would keep the industry happy, OSHA happy, and save lives.
With the field’s help, I wanted to create a construction grade guardrail system that would come as a kit. It would contain all the necessary components for easy rollout, faster installation, maneuverability, stacking and storing, inventorying, and be efficient and economical to ship from one project to the next.
Three years ago, we introduced the construction-grade, rapid-install Hilmerson Safety Rail System. Today, leading general contractors including Mortenson, JE Dunn, Turner, Gilbane, DPR Construction, and Ryan Companies use this patented, American-made system for high-profile projects across the country such as Allegiant aka Raiders Stadium in Las Vegas and the new West End MLS Stadium currently being built in Cincinnati, Ohio.
General contractors want better performance and more control over their bottom line
The trend toward using these more efficient systems is based on a variety of challenges. Safety is number one priority but it’s not always easy. In my conversations with the industry, it was clear they wanted something easier, more robust and faster to install, and they wanted it in kits. Other pain points included:
- Minimizing wasted time. Lean has become a big focus among contractors in thepast several years. Downtime costs contractors time and money, and impacts the project schedule. You can be more competitive if you limit down time. With 2 x 4s, for example, contractors must wait for the lumber to arrive onsite. Once delivered, it takes two to three carpenters to build them. Our reusable system installs 60 percent faster (as fast as 10 feet per minute), which is an immediate labor savings. It gives contractors more control over timetables and their labor force.
- Minimizing wasted materials. Two by fours get tossed at the end of projects. Lightweight powder-coated steel corrodes, rusts, and bends. Cast iron bases crack. Our 13-gauge hot-dipped galvanized plate steel is robust and made with the same material used to construct heavy-duty scaffolding. It is coated with zinc inside and out to prevent rust. It has a 15+ year lifespan. And, for every 10-foot of guardrail panel sold, we plant a tree in a U.S. national forest on behalf of the contractor who bought it.
- Safety railing that is cost effective. Reusable systems have a life expectancy of 15 years, at just two to three times the cost of railing for just one job. General contractors appreciate the ability to create a new company revenue stream by bringing the equipment cost in house. They buy the Hilmerson Safety Rail System as an asset just as they would buy a forklift, and rent it repeatedly to their construction projects. If purchasing the Hilmerson Safety Rail System doesn’t fit their business model, they can rent from various rental houses. For example, Sunbelt Rentals’ Scaffold Division now stocks our system. That is another good indication that the industry is trending this direction.
- Safety railing that is safer to install. A non-engineered system is only as good as the carpenter building it. There are risks of lacerations and other injuries associated with job-built wood railings, in part due to the number of people and tools involved in constructing them. Our weighted base system requires zero tools. Our anchored base system requires a hammer drill and socket. It’s also tougher for crews to cut corners. We’ve seen systems that have 4-5 anchor holes but only 2 or 3 anchors are intact. People aren’t complying. So, we designed and engineered a system that requires a single anchor. It’s either secured or it’s not. Plus, because of the design you can visually see if the system is connected, which provides an added safety feature.
- Better ways to transport, position and store railing. The last thing anyone wants is material being dropped onto workers below during hoisting operations or material being dislodged during traversing throughout the jobsite. We’ve minimized shipping and handling risks by creating a kit system. Each kit contains the necessary components to install and secure 200 linear feet of leading edge fall protection. The kits simplify stacking, storing, shipping and inventorying. They also reduce the footprint on jobsites, and can store 400 linear feet in 40 square feet, which comes in handy when space is tight.
- A more professional-looking jobsite. A disheveled site not only looks unprofessional, but it may contain several safety hazards. When you consistently have jobsites that look professional, with materials that are installed, stacked and stored properly, you look like an industry leader and a role model for others to follow.
- Safety railing that meets or exceeds OSHA requirements. OSHA loves engineered systems. I’ve had several OSHA reps ask me where to find our system because they were majorly impressed. As long as our system is installed properly, there will never be a problem.
This is the direction the industry is going. Contractors realize the old way of doing business needs to change. Using 2 x 4s is wasteful and time consuming. You don’t get money back by throwing 2 x 4s away, and you certainly aren’t making money spending wasteful time building them.
about the author
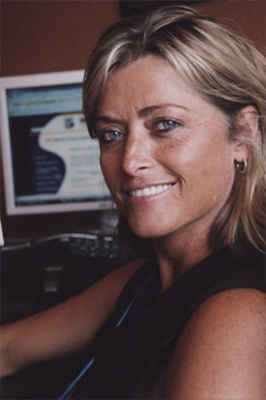
Changing a mindset takes a mountain of grit, something that describes Deb Hilmerson perfectly, from her hard hat to her steel toe boots. Her 30 years in construction as a field laborer, safety director, and consultant at companies like 3M Worldwide and Mortenson landed her in the right place at the right time to transform archaic equipment practices on construction sites as president/CEO of Hilmerson Safety. For more, visit hilmersonsafety.com/rail-system.