Finding and retaining quality operators has become a prominent point of concern throughout the construction industry. The next generation of operator is arriving, and these operators typically have a greater understanding of technology, but a lower level of patience with learning complicated machine operating systems.
Equipment manufacturers are implementing controls and technologies well suited for the next generation of operator to make machines easier to operate, more comfortable, and overall, more enjoyable. The interesting contrast being: in order for the controls and operator experience to become easier, the technology must advance.
CONTROLLING THE FUTURE
It’s no secret that technology has evolved leaps and bounds through the years, but many operators are creatures of habit and resistant to change. But the latest generation of equipment controls is more intuitive, easier to learn, and offers increased productivity.
Moving away from the old days of mechanical controls, manufacturers are implementing joystick, or electro-hydraulic, controls into their machines (but often offering the more traditional “stick” or “wheel” controls for operators who still prefer them). Offering a range of settings and adjustments, joystick controls make the machine easier to operate with increased feel and precision—often reacting in unison with the movement of the operator, making machine performance more fluid and precise.
The joystick offers very little physical resistance, while mechanical controls are more labor-intensive: the more response needed, the further the operator has to push or pull levers resulting in operator fatigue. With a more ergonomic placement, joystick controls are more comfortable for the operator.
One of the most popular features of electro-hydraulic controls is the ability to change the control pattern with the flip of a switch. With mechanical controls, the operator isn’t able to change the pattern. With the new controls, operators can push down on a switch for a few seconds and be in an entirely different control pattern. This increases productivity, accuracy, and operator satisfaction by allowing them to operate in the pattern they are most comfortable with. This also helps simplify training and operator retention; an operator is more likely to stick with a task if they feel comfortable with it and feel like it’s a function they can master.
Joystick controls often offer preset control settings. For example, CASE Construction Equipment offers EZ-EH controls on its skid steer loaders and industry exclusive feel points in the control handles, which allows the operator to feather control more easily. These systems use electronics and hydraulics to control machine function, and feature nine preset control settings—combinations of three for speed and three for control. Most equipment features a number of settings that, with the push of a button, tailor machine performance to the work at hand.
In the end, the latest generation of controls offers more versatility to meet the demands of operators and customers.
Joystick controls are more popular with younger generations of operators.
OPTIMAL COMFORT
One of the most important things manufacturers take into account when designing new machines is operator comfort. Because operators sit for long periods of time—up to 8 to 12 hours a day—ergonomical features are huge.
Operator comfort starts at the seat. Most machines feature air ride seats with adjustable armrests and customizable settings to increase operator comfort. Some machines offer heated seats with a potential for even further customizable advances in the future.
As mentioned previously, joystick controls reduce operator fatigue through limited wrist movement. But the location of the controls, switches, and buttons throughout the cab also provides additional comfort for the operator. Putting controls in easy-to-access locations helps limit operator movement and stress.
Many manufacturers have started producing machines with bigger cabs—the bigger, the better—while still fitting in the same footprint. With the added room, operators enjoy a more comfortable work environment without being confined to a small space.
Another important advancement in equipment design is sealing gaps throughout the cab in order to create a positive pressure environment. Pressurized cabs block out dust and other particles from entering the cab, keeping the operator more comfortable throughout the day.
Also, noise reduction improvements help to create an extra quiet environment. The quieter the cab, the more productive operators can be on the jobsite.
Recent advancements in cab technologies have also resulted in updated control panels and color displays. Monitors are conveniently located for easy access to important operational information, as well as controls for speed, frequency, fuel usage, and more.
WORKING MORE PRODUCTIVELY
Technology has the ability to keep equipment running smoothly and operating as productively as possible, resulting in cost savings and faster project completion times. Telematics and machine control are two systems that add significant benefits to machine operation.
Telematics integrates telecommunications and machine operating information so users can monitor the location, movements, status, and health of equipment and vehicles. Owners are able to access all the information from their office, with the machine communicating important information via web-connected devices.
Telematics data allows owners to identify machine performance trends, operator efficiencies and training requirements. With its ability to track the habits of operators, telematics helps them become more productive and exhibit more efficient practices.
Machine control technology makes it possible to finish projects faster, at a lower cost and with much higher accuracy.
Dozers and motor graders are among the more difficult machines to find and train qualified operators for. Machine control technology helps shorten the training window and allows less experienced operators to achieve similar quality work as those with more field experience.
The technological advancement of controls and systems will continue to advance—but in doing so, it will simplify ownership and operation. It’s important for manufacturers to continue to tailor their machine designs to today’s technologically savvy operator. With its ability to increase the productivity of the machine and the operator, make operation easier, and make operators more comfortable, there’s no reason to doubt technology’s power. ■
About the Authors Warren Anderson and John Bauer are brand marketing managers with CASE Construction Equipment.
Modern Contractor Solutions, August 2014
Did you enjoy this article?
Subscribe to the FREE Digital Edition of Modern Contractor Solutions Magazine!
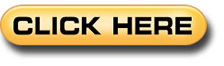