In any hospitality, or multi-unit residential project, the bathrooms are one of the key schedule drivers. As a result, more contractors are recommending a switch from traditional construction methods to modular bathrooms for greater schedule certainty, and to significantly shorten a project’s critical path. For example, “the benefit from using a modular system was equal to about 8 weeks in the overall schedule,” says Ed Kirk, director of construction for SODO Builders, commenting on construction of the 23-story, 393-room L.A. Live Marriott in downtown Los Angeles.
CHALLENGES OF TRADITIONAL CONSTRUCTION
“The bathroom is the most complex part of a hotel room,” notes Greg Steinhaeur, president of Seattle-based developer American Life. “You have many different trade professionals working in a small space, plus lots of materials having to go up the lift, to build them.”
With traditional bathroom construction, general contractors have to sequence 10 construction trades—including electrical, plumbing, and finishing work ranging from painting to mirror hanging—all working in an area of about 50 to 100 square feet. There are huge challenges with coordinating the dependent tasks on the Gantt chart, especially given the limited availability of workers in today’s tight skilled construction labor market.
With so many trades coming and going in a confined area, there’s also substantial risk of damage to previously completed work. As a result, bathroom rework accounts for about 60 percent of the punch-list in most hotel projects, resulting in 4 to 6 weeks of delays. Such bathroom quality problems cost developers hundreds of thousands of dollars in finance fees and lost revenue when they cause projects to open late.
PRE-FABRICATED ALTERNATIVE
In contrast to traditional bathroom construction methods, pre-fab bathroom pods consolidate all the construction trades into one unit. Such modular bathroom units are easy to lift, place, and connect, which helps save time and money, while improving bathroom quality for hotel owners and guests.
Modular bathrooms are built in a factory setting to each project’s specifications, then delivered by truck to the jobsite with all of the finishes and fixtures pre-installed. Construction crews crane the pods to the appropriate floor, then slide them into the structure while the building façade is still open.
A two- or three-person crew then maneuvers each pod into place, anchors it, and connects the electrical systems, hot and cold water hook-ups and waste water disposal. Exterior drywall is installed on the pod as part of finishing the rest of the hotel room. Modular bathrooms are somewhat like a dishwasher, in that they’re slid into place, ready to “plug and play.” Manufacturers like Oldcastle can deliver and install up to 30 modular bathrooms per day.
In the 23-story, 282-room Embassy Suites by Hilton hotel under construction in downtown Seattle, prefabricated bathrooms are saving about 32,000 labor hours. The GC is able to re-deploy those workers to other parts of the building, which he predicts will cut the construction schedule by 8 weeks. “We only see advantages to using modular bathrooms, especially given Seattle’s tight construction labor market,” notes developer American Life’s Greg Steinhaeur.
Featured Image: A crane lifts a modular bathroom to an upper floor of Seattle’s new Embassy Suites hotel.
Above: Bathroom pods await final placement and hook-up by two- to three-person crews.
4 S’S OF PRE-FAB
The benefits of modular bathrooms compared to traditional construction can be summarized with 4 S’s: speed, simplicity, superior quality, and safety.
Speed. The 8 weeks of schedule savings for the L.A. Live Marriott and Seattle Embassy Suites projects discussed previously are typical for large hotels with a few hundred rooms. With modular bathrooms, “the flow of the job went faster and smoother,” notes Dan Medeiros, designer and detailer for Pan Pacific Mechanical, the mechanical contractor for the L.A. Marriott job. “The framer was able to get the walls built faster, and we were able to move to the next floor level much quicker.”
Simplicity. Installing one unit is much more streamlined than juggling nearly a dozen trades on site; plus, modular bathrooms come as one pre-inspected quality-controlled unit with standardized documentation. “I typically write 110 requests for information (RFIs) per project,” says Pan Pacific Mechanical’s Dan Medeiros. “I only wrote 33 RFIs [for the L.A. Live Marriott].”
Superior quality. Modular bathrooms can be built to any level of finish, including for luxury hotels. Once installed, the bathrooms are indistinguishable from ones built on site, so can meet the needs of the most discerning hotel owner and guest. Pre-fabricated bathrooms have been installed in dozens of buildings throughout the U.S. ranging from the Prospect Plaza housing development in New York City to the five-star Broadmoor Resort in Colorado Springs, Colorado.
Safety. Constructing bathroom pods in a factory vs. building bathrooms on site improves worker safety by eliminating the dangers of poor weather conditions and reducing the risks of working at heights. Removing bathroom construction from the site reduces workers comp rates, decreases the risk of OSHA violations, and has the potential to reduce general liability insurance.
Crews use a hand truck to maneuver a bathroom pod into place.
CONCLUSION
Cities such as New York, Los Angeles, and Seattle are strong examples of places where pre-fab is worth considering. Each is experiencing a building boom, while facing skilled labor shortages. And, their complex downtown environments add to the logistical difficulties of coordinating building bathrooms on site.
Developers and contractors naturally wonder about the costs of modular bathrooms compared to building on site. Modular bathrooms are cost neutral in an average construction cost market, such as where the RS Means index is around 100. In markets where the cost of construction is above that, bathroom pods typically cost less than traditional construction. The challenge is to scope the pods properly and find receptive sub-contractors to bid their work properly in conjunction with the pods. ■
About the Author: Bill Seery is director of business development for Oldcastle SurePods modular bathrooms. Seery has specialized in the building prefabrication industry for more than 10 years, with responsibilities for both management and operations. Contact Seery at bill.seery@oldcastle.com.
_________________________________________________________________________
Modern Contractor Solutions, February 2017
Did you enjoy this article?
Subscribe to the FREE Digital Edition of Modern Contractor Solutions magazine.
Why it Might be Time to Flush Your Old Way of Building Bathrooms
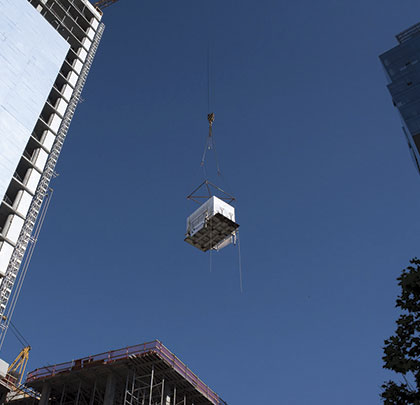