By Rick Smith
Construction site safety should always be top of mind and should be made a priority each and every day. Training is one of the best ways to promote safety on your job site. But, many people—and companies—do not understand the training requirements or each individual’s responsibilities for MEWPs (Mobile Elevating Work Platforms) outlined in the most current ANSI A92 and CSA B354 standards. So, how do you know what type of training (if any) that you need?
There isn’t a one-size-fits-all answer to this question. The industry standards impact both end users and dealers, and the reality is that the type of training you need will depend on what you are doing on (and around) a jobsite. And, if you have more than one role on site, it is likely you will need more than one type of training. Below is an outline of the type of training mandated by the access industry for different roles and responsibilities.
EQUIPMENT OPERATORS
A MEWP can only be operated by persons who have been trained, familiarized, and authorized to use the specific machine, before they use it. And, MEWP operators must also be able to prove that they are physically and mentally capable of operating the machine safely. Also, all operators must be able to prove that the training they receive meets the most current published standards.
What does all of this mean? It means that if you are a MEWP operator, you are responsible for completing training that delivers the skills you need to properly operate the equipment.
Proper MEWP operator training is comprised of two components: Theory Training (can be done online or in-person in a classroom setting) and Practical Training (hands-on training and evaluation), per the guidelines stated in the A92.24 Training Standard. It is important to know that both components must be completed in order to fulfill industry training requirements.
There are many reputable industry organizations, as well as equipment manufacturers like JLG, that offer industry-certified training programs to help you meet these obligations. For instance, JLG offers several different, easily-accessible training options for you to take advantage of, including classes through JLG University, the company’s training center and proving grounds and AccessReady.
Once you complete an industry-complaint training course with a JLG qualified training provider, you will receive a certificate of completion. You also have the option to purchase an operator card that becomes your proof of training from the training entity.
OTHERS TO BE TRAINED
In addition to mandated operator training, the updated ANSI and CSA standards also now require training for anyone who comes in contact with a MEWP on the jobsite, including Supervisors, Occupants, and Maintenance & Repair Personnel. There are also specific training guidelines outlined for Equipment Dealers.
These roles are defined as:
- Supervisors: People who directly supervise MEWP operators (ANSI only)
- Occupants: People in the MEWP platform who are not considered operators (ANSI & CSA)
- Maintenance & Repair Personnel: People servicing MEWPs (CSA only)
- Equipment Dealers: Includes rental companies (ANSI & CSA)
SUPERVISORS (ANSI ONLY)
The updated ANSI A92 standards for the access industry state that anyone who directly supervises MEWP operators is considered a “Supervisor” and is required to complete supervisor-specific compliance training. Supervisor training can be completed online or in-person.
OCCUPANTS (ANSI & CSA)
It is specifically noted in the current aerial industry standards that MEWP operators must provide instructions and/or make sure all occupants in the machine have a basic level of knowledge to work safely on the MEWP. The standards also state that at least one occupant must be taught how to operate the MEWP controls in case of an emergency where the operator becomes incapacitated. This is important to understand as the standards only give the occupant the authority to operate the MEWP in an emergency. Occupant training should be conducted on site, in person, by the operator prior to machine use.
MAINTENANCE & REPAIR PERSONNEL (CSA ONLY)
According to current industry standards, only a qualified person should inspect and maintain Mobile Elevating Work Platforms (MEWPs) in accordance with the manufacturer’s recommendations. This means that to effectively work on, repair and maintain MEWPs, service technicians and other maintenance and repair personnel working on a jobsite need to have a deep understanding of the construction, operation, and maintenance of this type of equipment—especially as it relates to the new machine design standards.
EQUIPMENT DEALERS
Under the updated ANSI A92 and CSA B354 standards, dealers (which includes rental companies) are now required to offer training and familiarization to anyone who rents, leases, or buys equipment. If requested, as an equipment dealer, you must provide training or advise the renter on where to get operator training, as well as offer familiarization to the person designated to receive the MEWP. You must also ensure that your maintenance technicians, as well as your customers’ service techs, are all trained on new features and marking standards for proper MEWP servicing.
CLOSING THOUGHT
As you can see, there is a significant level of importance associated with training in the current aerial industry standards. This is because proper training significantly reduces jobsite hazards related to accidents or incompetence. If your jobsite regularly uses MEWPs, it is crucial that you make the investment in training—not only to be in compliance but also to take advantage of having access to all of the knowledge and expertise available through proven MEWP training, like that offered through JLG.
About The Author
Rick Smith is a senior director of global training with JLG. For more information about training requirements in the ANSI A92 and CSA B354 standards, visit www.jlg.com/en/destination/ansi/training.
Modern Contractor Solutions, April 2021
Did you enjoy this article?
Subscribe to the FREE Digital Edition of Modern Contractor Solutions magazine.
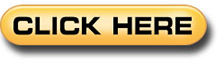