By Jenny Shiner
In a culture that revolves around instant gratification, there is a higher expectation for efficiency than ever before. To ensure the maximum productivity to deliver these results for customers, contractors are focused on enhancing their current efficiency standards with technology. As a part of this effort, businesses are obtaining the optimal productivity from their vehicles and employees by implementing Telematics software. This technology keeps fleets on schedule, automates manual processes, increases technician productivity on the jobsite, and sustains vehicle health through streamlined maintenance management.
ENHANCE ROUTE EFFICIENCY
Utilizing Telematics to manage drivers’ daily routes will increase how quickly vehicles and equipment arrive at each jobsite. And it makes a significant impact on staying on schedule throughout the day.
Contracting businesses ensure their drivers take the best routes by entering the addresses or landmarks associated with jobsite locations into the Telematics software. The technology optimizes the route and then sends it straight to the driver’s smartphone, tablet, or any other smart device with turn-by-turn directions. Utilizing Telematics allows fleet managers to optimize drivers’ daily schedules before they even start the workday.
AUTOMATE MANUAL PROCESSES
The ability to streamline manual processes associated with tracking payroll, fuel expenses, labor costs, billable hours, and job costing saves countless hours. Imagine how much could be accomplished with this time that would have otherwise been spent quantifying data. Telematics reports provide insight into all aspects of fleet expenses and gathering this information at the click of a button drastically increase productivity in the back office.
Tracking costs with a Telematics solution reduces the time required to complete this task, which allows contracting businesses to analyze the results in-depth. It is essential to analyze these fleet expenses to ensure the business is not spending more than necessary on fuel, labor, maintenance, or any other overhead costs.
Also, using Telematics can drastically decrease the number of staff hours it takes to complete International Fuel Tax Agreement (IFTA) reporting, the fuel tax collecting and sharing agreement for the redistribution of fuel taxes paid by interstate commercial carriers. While the reporting is required and overall beneficial, the process of manually gathering information for IFTA paperwork can be a headache to endure. This process can be completely automated with Telematics with a state mileage report. This reporting breaks down the number of miles driven within each state per month, giving contractors all of the necessary IFTA report information is provided without error
MONITOR AND COACH EMPLOYEE PRODUCTIVITY
The number one challenge contracting fleets face without fleet visibility is a lack of employee accountability while in the field. Monitoring fleet activity with Telematics provides fleet managers quantifiable data on employee performance in the field. The ability to monitor and manage how productive employees are with their time helps contractors increase how efficiently they are completing every job.
Fleet managers use Telematics to monitor idle time, miles driven, and time on site to ensure productivity is where it should be. Ensuring drivers are as productive with their time as possible helps complete the maximum number of jobs possible. Fleet managers can receive alerts if vehicles surpass an acceptable threshold of idle time and monitor route efficiency reports to identify when drivers are wasting time and/or driving too far out of their way.
To increase job efficiency, fleet managers can monitor stop detail reports and receive long stops alerts to track how long drivers spend on the jobsite. By using the information gathered from Telematics to coach employees on more efficient practices, your fleet will be able to complete jobs faster and more effectively in the future.
IMPROVE MAINTENANCE MANAGEMENT TO KEEP THE FLEET AT WORK
Staying on top of maintenance can be labor-intensive for contractors without an automated solution in place. Manually tracking odometer readings to stay on top of essential maintenance items doesn’t only result in services being missed. It causes unexpected vehicle downtime. When vehicles are out for repairs unexpectedly, contracting businesses are forced to run with fewer vehicles. Or they may have to postpone jobs if they can’t get a piece of equipment out to a jobsite as scheduled. Using automated maintenance management software, like Telematics, helps to keep the fleet at work and complete more jobs.
Contractors can use Telematics to schedule automated maintenance reminders to notify management and drivers when trucks or equipment are due for services. Maintenance reminders ensure oil changes, tire rotations, emissions testing, and any other type of preventative service are completed when they should be. Scheduled service reports are also available for fleet managers to view on a daily/weekly/monthly basis. These reports include upcoming and overdue services so management can make sure all maintenance is current.
Culy Contracting, a construction service, focusing primarily on the water & sewer industry, commercial, residential, and municipal organizations, uses Telematics in conjunction with Electronic Logging Devices (ELDs) to streamline their maintenance process while staying compliant with the ELD mandate. They are able to use the technology to set their annual inspections, oil changes based on miles driven, and other preventative maintenance.
BOOST PRODUCTIVITY
Telematics makes it possible for contractors to boost productivity throughout their operations, from employees in the field all the way up to fleet management, to be as efficient in their day-to-day operations as possible. Using Telematics increases route efficiency, dispatch responsiveness, ensures technicians are as productive as possible, and keeps fleets at work with improved maintenance management.
CLOSING THOUGHT
While this article outlines several ways to boost productivity for a contracting fleet, the most important takeaway for driving any initiative forward is to go beyond just implementing technology. What needs to occur is strategically aligning the data being collected to challenges happening in the business. That is where a significant boost and productivity will occur, and where contractors will experience the most dramatic results for their business.
About the author
Jenny Shiner is the communications manager for GPS Insight. She graduated from Arizona State University with a Bachelor’s of Communication and is responsible for external marketing communication for all business segments that GPS Insight targets. For more, visit www.gpsinsight.com.
Modern Contractor Solutions, October 2019
Did you enjoy this article?
Subscribe to the FREE Digital Edition of Modern Contractor Solutions magazine.
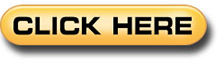