The winters in the northeastern United States are tough and the roads are even tougher. But this isn’t new to the team at Northeast Paving, a division of Eurovia Atlantic Coast. They have been serving the communities throughout New England for more than a century and today operate 11 asphalt plants located across Maine, New Hampshire, Vermont, Massachusetts, and Pennsylvania. It’s safe to say they’ve learned a thing or two about asphalt paving along the way.
MAKING IT WORK
Johnniel Gomez, a project engineer at Northeast Paving, has witnessed these learnings firsthand. He recalls the difference between two projects Northeast Paving completed on I-90 through Blandford, Massachusetts, “The first job we struggled a lot with trucking, finding enough trucks, having that coordination with trucks, getting them staggered in the right locations, trying to do the whole milling and paving in the same shift, and it just didn’t really work out.” What didn’t work was a lack of communication between the field and the asphalt plant throughout shifts, trucks taking detours, and trucks creating inaccurate timecards and reporting information. Northeast Paving needed more accurate information and communication. The solution? Bringing on FleetWatcher’s Material Management System (MMS).
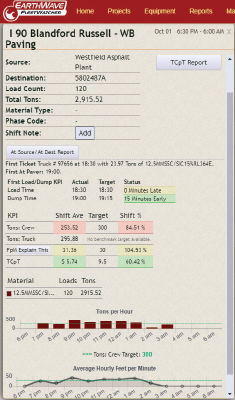
Northeast Paving’s work on I-90, like roughly 60% of their work in Massachusetts, is Department of Transportation (DOT) work. Two of the company’s asphalt plants in the state focus primarily on FOB work while the other two support laydown operations. All of them were involved when Northeast Paving returned to work on the 7-mile, three-lane wide westbound and 4-mile, two-lane eastbound stretch of I-90 the following year.
Gomez and the team came back to I-90 armed with FleetWatcher’s MMS system which utilizes wireless telematics and transponders placed in company and third-party trucks to relay real-time position data, dispatch communications including notifications, Quick Truck Pay, and more, to the entire Northeast Paving team. Receiving information in real time allows the Northeast team to monitor key performance indicators (KPIs) and make corrections in real time. Northeast Paving saw an immediate impact from FleetWatcher on day one. “With using FleetWatcher the first day, we had 25 trucks. We said okay, we’re doing a little better. Let’s see if we can knock off a couple trucks and save a couple bucks.”
REAL-TIME INFO = BONUS
With more eyes and focus on asphalt movement and production, Northeast Paving was able to knock a truck or two off while maintaining a steady pace in the field for the 45,000-ton job. This translated to consistent quality throughout the project, which earned the company a bonus. “We had great quality numbers out there in terms of we didn’t have a lot of stops and starts out in the field, so we minimized the bumps and joints allowed in the road and we ended up getting 99.9% bonus,” Gomez says.
In addition to using FleetWatcher for managing their hauling, Northeast Paving also was able to use it to improve their communication between departments. “The plant guys and the paving foreman were constantly utilizing FleetWatcher and constantly talking back and forth to make sure they have trucks on the way, so the paver can still run at that 35 to 40 feet per minute and get our production,” Gomez says. With this level of communication helping to optimize production, Northeast Paving saw their tonnage on average shifts rise, including a 3,800-ton day during a 10-hour shift.
EASE OF USE
In Gomez’s opinion, part of what has made incorporating FleetWatcher into Northeast Paving’s process has been its ease of use. “Anyone that has access to it [FleetWatcher] can understand what it is, and it’s pretty easy, so someone can see on any given minute, any given time frame, you can see how well the crew’s doing out in the field.” With a mobile app available on mobile, tablet, and desktop devices, the Northeast Paving team can access real-time data in the office or on the go.
KEY PERFORMANCE INDICATORS
Throughout the entire project Northeast Paving was able to track their main KPIs, 90-minute cycle times, paving at 35 FPM, and keeping the plant running at 400 TPH, through FleetWatcher. With easy KPI monitoring showing green (good) or red (not hitting targets), Gomez and his team could easily see at a glance in real time if they were on track or if they needed to make tweaks or adjustments to their trucking. When they added up all the benefits of FleetWatcher’s MMS system, Northeast Paving saw significant savings from the first Blandford project to the second.

E-TICKETING
While Northeast Paving is certainly achieving gains with FleetWatcher, they are still learning to use different aspect of the platform. For instance, Northeast Paving’s work in Massachusetts didn’t require e-ticketing but Gomez predicts more and more e-ticketing requirements for DOT work in the near future. While the company doesn’t currently use FleetWatcher’s e-ticketing system, they are prepared to make the switch when they need to. “The area manager that’s overseeing the whole thing said hey, is this something FleetWatcher can help us with? I said yep, FleetWatcher’s on it,” Gomez says. The milling and paving company is looking forward to exploring how implementing more FleetWatcher features can help push their business forward.
CLOSING THOUGHT
Northeast Paving has been able to utilize FleetWatcher to learn from their previous projects, be more efficient in their current jobs, and be better prepared to navigate the future of the asphalt industry going forward.
About The Author
Earthwave Technologies manufactures construction-specific wireless telematic products which provide complete visibility to all components used within the process. Its industry-leading FleetWatcher Materials Management Solution (MMS) is used by asphalt paving contractors across the U.S. For more, visit www.earthwavetech.com.
Modern Contractor Solutions, June 2021
Did you enjoy this article?
Subscribe to the FREE Digital Edition of Modern Contractor Solutions magazine.
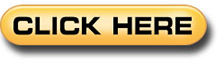