By Mike Merrill
Given everything the construction industry has faced this year, it should come as no surprise companies are exploring different ways to trim costs. And while adopting leaner practices can be good for the bottom line, cutting corners simply isn’t a possibility when the safety of customers and employees is on the line. That’s why more and more construction leaders are investing in technology––they know making the switch will save them money in the long run, whether from labor tracking or, more significantly, employee safety.
According to the National Safety Council (NSC), the average medically inspected injury costs $42,000. Work-related injuries cost the construction industry $170.8 billion in 2018. More than $57.6 billion of that is administrative, while $12.8 billion comes from uninsurable losses, including writing up injury reports, the loss of time from non-injured employees and the cost to investigate injuries. That’s $70.4 billion in losses that aren’t covered by insurance every year, with an average of $17,220 of uninsurable costs per medically examined injury.
As a construction leader, those numbers can’t be ignored. Fortunately, live field safety data can increase the safety of your employees onsite while helping your company save on the unrecoverable costs mentioned above. Here’s how:
INSTANTANEOUS REPORTING AND PROMPTS REDUCE UNSEEN SAFETY RISKS
On today’s jobsites, things change quickly; fortunately, live safety tracking allows managers to require that workers fill out questionnaires at the beginning of a shift to track their activity from task to task and on clock in or clock out. Safety managers can use the same app to share safety training videos from OSHA or the CDC as well as toolbox talks right after they clock in or before they clock out for the day. This technology also gives safety managers the flexibility to automatically prompt all employees, or only specific employees, to report their work conditions, watch a video or fill out a form. In addition, they can receive the time, date, GPS Location stamps and signatures for proper documentation for their safety programs.
Instant communication between management and the boots on the ground allows construction companies to respond to any situation as quickly as possible, limiting the jobsite’s exposure to risk, problems, or errors. Instant responses will keep employees safer and, in turn, decrease the risk and costs associated with an injury. Only 34 percent of contractors surveyed report receiving their safety reports in real time. Unfortunately, 69 percent of all companies under 1,000 employees lack access to live field safety data collection, exposing the most vulnerable companies to the increased risk of injury and job site shutdowns, according to the Live Field Data Usage report.
REQUIRING SAFETY FORMS AT CLOCK IN OR OUT INCREASES WORKER ENGAGEMENT
Construction managers need insights into their jobsites to monitor heavy equipment usage, personal protective equipment (PPE) implementation, site conditions, and employee health. Still, up until now, they’ve found it difficult for employees to consistently share this data in an actionable way. New technology finally allows for live safety data to be recorded and tracked from an employee’s smartphone. Resource management apps can even provide businesses with an all-in-one location for safety screenings and labor tracking as well as other functions such as equipment tracking, job progress tracking, and job cost tracking. Live safety apps built with integrated workflows trigger screening forms to pop up when employees clock in on their mobile apps. This ensures that contractors achieve total compliance from employees on jobsites. The data takes only seconds to record and can be automatically emailed to anyone who needs it immediately.
Live field data allows contractors to assess the collected information as it comes in so they can respond to any safety issues or violations, decreasing the chances of accidents and potential fines. GPS tracking of employees in a resource management solution also assists in identifying the location of a situation or breach of protocol so that they can avoid similar circumstances in the future. Employee location tracking has been a critical solution during the COVID-19 pandemic, giving management the ability to manage social distancing and trace any possible exposures if an employee is found to have COVID-19.
REMOTE SAFETY TRAINING WITH VIDEOS ON MOBILE FORMS CREATES THE MOST EDUCATED WORKFORCE
A study by the American Journal of Independent Medicine determined that toolbox talks are crucial teaching elements on the jobsite. The study proved that toolbox talks were an effective way to share critical safety and project-based updates. The study also revealed that the more relevant and personal the information was, the more effective it became. Cloud-based solutions provide an agile platform to quickly deploy new toolbox talks, effectively training their employees on new safety procedures and other safety training information without requiring large coordinated meetings. It’s never been easier for construction employees to create high quality toolbox talk training videos to share best practices by making a video with their smartphone. They don’t have to be professionally produced or take weeks to make. Additionally, after employees complete a video or training, safety managers and supervisors will receive documentation with time-stamped employee signatures.
With video links embedded in a form that is prompted by clock in actions, management can be confident in their safety training acknowledgements because the forms can capture signatures with time and date stamps from employees. This instant feedback helps to maintain OSHA compliance, and the best part is that it can be completed immediately as soon as the new video or document is uploaded.
IMPROVE EMPLOYEE SAFETY WITH LIVE FIELD DATA FOR EQUIPMENT TRACKING
With COVID-19 at the forefront of everyone’s mind, contractors have been increasing their use of safety checklists on mobile forms to make sure employees are properly disinfecting equipment and taking photos of the current state of their equipment. Once we enter post-COVID jobsites, contractors can continue to collect equipment safety checklists from employees as they clock into a job requiring equipment usage. As soon as the equipment safety checklist is completed, it can automatically be emailed to the equipment manager. Standard maintenance is also tracked through the same app, extending the equipment lifecycle and keeping tabs on any signs of wear. For example, if an employee notices excess wear and tear on bulldozer tires, they can immediately share that information with the safety manager and equipment manager at the same time by automatically emailing the completed equipment checklist survey to both. The employee can easily checkout another bulldozer that is available, and request maintenance to quickly replace the tires, avoiding the risk of potential injury and inoperable equipment.
There are several other ways live field data for equipment tracking can also impact jobsite safety. Without an accurate inventory of equipment, employees could be using the wrong equipment for their task at hand because they can’t locate the appropriate equipment. This can lead to accidents and injuries. With live field data, employees have global visibility of all of the company’s equipment, along with the location of each asset, to make sure they can find the right piece of equipment to get the task done in a safe and timely manner.
In the field, contractors run the risk of overusing the more readily available equipment, even when improper, which drastically increases the risk of dangerous equipment failure. Effective maintenance schedules avoid downtime and can help eliminate the temptation to push equipment beyond suggested limits to avoid potential injuries. When asset usage is tracked in the same app as the maintenance forms, employees can quickly see if a piece of equipment is approaching its next scheduled maintenance. If maintenance is overdue, another piece of equipment can be selected to avoid unnecessary risks.
CLOSING THOUGHT
Injuries don’t have to be inevitable; live safety data eliminates unnecessary risks and effectively manages the dangers inherent on the jobsite. The best way to avoid any fines from safety infractions or surprise costs associated with safety injuries is to have a proactive safety program that empowers all of your employees and makes it easy to manage safety on the jobsite. Investing in technology on the front end will help companies avoid hefty uninsurable costs down the line.
about the author:
Mike Merrill is the Co-founder and COO of WorkMax. Mike spent 22 years as an entrepreneur and business owner in the construction and technology industry. He is also a member of the Construction Financial Management Association (CFMA) and Construction Open Standards Alliance (COSA).
Modern Contractor Solutions, November 2020
Did you enjoy this article?
Subscribe to the FREE Digital Edition of Modern Contractor Solutions magazine.
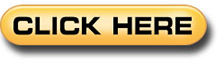