Cranes and under-construction high-rises dot the Seattle-area skyline—a telltale sign of the building boom there. Construction hit a 10-year peak in 2016, with 65 major buildings in progress downtown and in surrounding neighborhoods, according to The Seattle Times. In such a demanding market, it’s important for contractors to complete jobs quickly, while also meeting stringent seismic code requirements.
For Apex Steel, a structural steel contractor based in Kirkland, Washington, finding ways to save time while still meeting quality demands is critical to productivity, scheduling, and the bottom line. Demanding project timelines and quality requirements are key drivers for structural steel contractors like Apex. Many building projects in Seattle must meet the American Welding Society (AWS) D1.8 structural welding code—stringent requirements used in seismic regions. As a result, the area sees a higher demand for D1.8 certified welders.
“The market in our area is so strong that we need to complete these projects faster because we’ve got the next project to move on it,” says Jim Greene, Apex general superintendent. “Our customers really demand quality, and they’ve come to expect the quality that Apex puts out there on every project.”
Apex specializes in steel erection, architectural metals, reinforcing steel, and tower crane, and construction hoist projects, working extensively in the Seattle region with another office in Billings, Montana. The company’s construction work runs the gamut from small to large projects such as high-rises and bridges.
Utilizing wire welding processes and ArcReach® remote control welding technology from Miller Electric Mfg. Co. allows Apex to address numerous challenges—helping to significantly improve productivity while meeting high-quality requirements and improving operator safety on the jobsite.
“The quicker you get jobs done—in an efficient manner, in a safe manner—you’re going to get more jobs and bigger jobs,” says Travis Slovernick, Apex field superintendent. “It’s just night and day, the difference with this (ArcReach) system.”
ADDRESSING MANY CHALLENGES
Like many contractors in the Pacific Northwest, Apex typically uses wire welding processes. Many companies in the region have transitioned from stick welding to self-shielded wire on construction jobsites, due in part to the significantly higher deposition rates they can achieve.
“Apex is a progressive company, and they’re always looking for ways to become more productive,” says John Powers, field construction sales specialist with Pacific Welding Supplies.
Apex works with Pacific Welding Supplies to select welding machines and filler metals; Apex rents about 60 percent of its welding fleet and owns about 40 percent of it. Pacific also helps Apex develop welding procedures.
Staying on top of the latest advancements and technologies is important to Apex, to ensure the company is using solutions that help to meet critical project deadlines and demanding quality requirements. Apex welding jobs often include joint penetrations, fillet welds, and butt welds, with steel thicknesses ranging from ¼-inch to 6 inches or more.
Apex uses Miller® XMT® 350 CC/CV multiprocess welders with ArcReach technology on many jobsites. The ArcReach remote control technology helps Apex increase productivity, maintain consistent arc quality, and improve safety. The solution offers remote control of the power source at the weld joint without a control cable, by way of a SuitCase® X-TREME™ 12VS feeder with ArcReach.
“This system from Miller saves so much time and money,” Slovernick says. “A welder can control everything right where he’s at. Production wise, that’s key.”
SAVING UP TO TWO HOURS PER DAY
The ability to control parameters at the weld joint reduces the time operators spend walking to and from the power source to make adjustments. This can save an hour or two each day per welding operator for Apex, greatly increasing arc-on time and productivity.
“Those 2 hours a day on each welder, with 10 welders on a job, we’d be losing 20 man hours a day in going back and forth,” Greene says. “This ArcReach technology has really helped us become more competitive. It has been an unbelievable savings for us in man power.”
Utilizing remote control technology helps keep Apex on time and on budget, while also making the job easier for welding operators, especially on large jobsites where they may have to climb down a ladder or several flights of stairs to access the power source—perhaps a distance of several hundred feet.
“Running back and forth you can burn up time. You can spend more time doing that then actually doing your job sometimes,” says Willy Perkins, an ironworker from Local 86. “It’s nice to have technology that makes our job easier.”
Apex also reaps time savings since the ArcReach technology provides remote control capabilities without a control cable. This saves time in rolling and unrolling the cable each day, in addition to time and money spent on cable maintenance and repair.
“You have less equipment to worry about getting damaged,” Slovernick says. “I know we used to spend a lot of time fixing that equipment, and you no longer have to do that.”
REMOTE CONTROL TECHNOLOGY
In addition to significantly improving productivity, remote control capabilities at the weld joint also provide benefits for worker safety. The fewer trips an operator must make back and forth to the power source—often up or down ladders or several flights of stairs—the fewer opportunities there are for slips, trips, and falls and exposure to other jobsite hazards.
“We get in spots where it can be hard to get to sometimes, and when you do get there, the last thing you want to do is move again just to go up a volt or drop your amps,” says Kyle DePaoli, an ironworker from Local 86. “Not having to get off the iron every 2 minutes saves a lot of time and it’s safer.”
It can also be an issue of operator fatigue, when an operator must climb up and down stairs frequently or get to and from a hard-to-reach welding location. One Apex job in Bellevue, Washington, involved constructing a sky bridge pedestrian walkway between two buildings. The welding operators used ladders laid flat to reach the spot of the weld, where they were joining two columns about 20 feet off the ground. Getting to the ground required maneuvering from that spot and going down several flights of stairs.
“The wear and tear on the guys and the fatigue—the remote technology saves everybody all the way around,” Slovernick says. ■
For More Information
For more information about the latest welding technology from Miller, visit www.millerwelds.com.
_________________________________________________________________________
Modern Contractor Solutions, August 2017
Did you enjoy this article?
Subscribe to the FREE Digital Edition of Modern Contractor Solutions magazine.
Man Power Savings
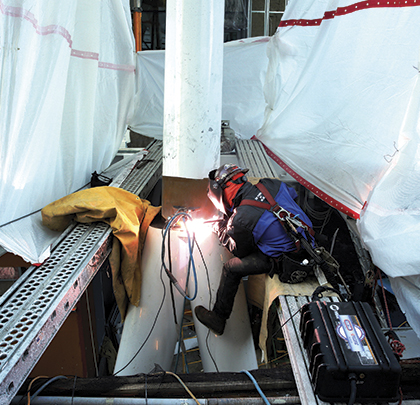