Into its third decade of use, GNSS is only now starting to hit its stride. Its far-reaching impact has been evident in a major Tempe, Arizona, site clearing and development project, where Buesing Corp. is using GPS for a number of varied processes on-site.
TAILGATING LEGACY
Buesing is currently a subcontractor to Ryan Companies for a $650 million development called Marina Heights, which will feature almost 2.1 million square feet of combination office and retail space. Located directly across from Arizona State University’s Sun Devil Stadium, the site was once the prime location for pre- and post-game tailgaters. Prior to that, it was a repository for some of the university’s trash and construction debris (and a “midnight landfill” for some in the area), a fact that has proven problematic since earthwork began for the new facility.
“The site design includes five main buildings and a below-ground podium parking garage for more than 8,500 cars,” says Buesing project engineer, Dan Kuehl. “That design was actually scaled back from a three-level, below-ground parking area to just two levels when those environmental issues were, literally, uncovered. So, when we first arrived on-site, we removed all the asphalt, had it ground down, and sold it as RAP to a local asphalt company. The earthmoving effort itself is pretty significant and includes removal of more than 425,000 cubic yards of material.”
Kuehl says they are taking all the clean material to another Buesing project nearby which is sorely in need of fill. Any pockets of trash they hit, however, they load and haul to the Apache Junction landfill about 25 miles east of the Marina Heights location. “With tipping costs being what they are, it has been a costly cleanup, that’s for certain.”
DRILLING FOR STABILITY
Because of both the general soil composition and the Marina Heights location—adjacent to the Salt River—Buesing took precautions to ensure soil stability throughout construction. This meant, among other things, installation of nearly 1,400, 24-inch-diameter column shafts, drilled as much as 35 feet into the ground, then injected with a concrete slurry mixture. Getting to a point where they could effectively drill for those shafts involved some additional work and brought their GPS capability into play, says Kuehl.
“To install the column shafts in advance of the shoring wall, we decided to construct several temporary benches—of varied heights—that the drilling and support machinery could work off of,” he says. “We are drilling every hole at 3 feet on center, and on the north wall every other hole will have slurry and a 35- to 40-foot steel beam placed in it. Doing so will allow us to use a tie-back system—rather than the soil nails as we are doing everywhere else—to handle the hydrostatic pressure from the river.”
Because the developer was handling survey on the project, none of those temporary benches existed on any of the original plans. Buesing addressed that issue by modifying the existing 3D model, then using a Cat 140M motor grader with Topcon 3D-MC GPS machine, constructed each of the benches. To conduct daily grade control and meet the tight tolerances needed for the shoring wall line, Kuehl and his crew used their own Topcon GR-5 base and rover full time as supplemental survey.
He adds that they took the 50,000 cubic yards of material used to construct the benches from on-site using Cat 623 scrapers. “We basically stripped the top soil until we hit trash, used it to build what we needed, and then moved on to another area, and did it again,” he says.
MODEL PROJECT
The Marina Heights project design includes five separate structures, each with a unique subgrade elevation. Originally, a single master GPS model provided guidance and verification to crews involved in the mass excavation facet of the job. According to Kuehl, however, Buesing opted to generate additional models better suited to the functions they are self-performing.
“For example, we created a secondary model of the mass excavation plan for this entire site,” he says. “So, rather than just having neat, lined subgrade areas for the five different zones, the model shows all the intricacies—the safe slopes, elevator pits, mat foundation pits, ramps, and so on. That helps us not only for layout with our base and rover, but also for use of the 140M motor grader, one of our Cat 374D excavators, and probably even our dozer. We are a GPS company—we have been for some time—it just makes sense to capitalize on that.”
CALCULATING SUCCESS
Examples of the benefits GPS technology has provided on the Marina Heights project are also in non-equipment related functions. Project tracking issues, such as volume calculations, had long been a tedious and time-consuming effort. Today, using that GNSS capability, that’s all changed, according to Brett Smith, another project engineer at the site. Now, the company can quickly and easily perform tasks, such as generating quantity estimates for monthly pay applications.
“Another good example of this can be seen in ‘turnover areas,’ sections which have firm milestone dates at which work must be completed. Often, we have to calculate how much material is in an area and how long it will take us to move it to meet those targets. Doing that is now as simple as taking a quick topo and comparing it to our model. If we see that we have 60,000 yards remaining and 15 days to move it, we know we have to move 4,000 yards a day. From a planning standpoint, that can be huge.”
Buesing Corp. maximized the use of its GPS technology for the Marina Heights project, which is slated for completion in fall 2017. ■
About The Author:
Larry Trojak is president of Trojak Communications, a Minnesota-based marketing communications firm. He has written for the construction, recycling, demolition, scrap, and aggregate processing industries.
_________________________________________________________________________
Modern Contractor Solutions, February 2015
Did you enjoy this article?
Subscribe to the FREE Digital Edition of Modern Contractor Solutions magazine.
Making the Grade at Marina Heights
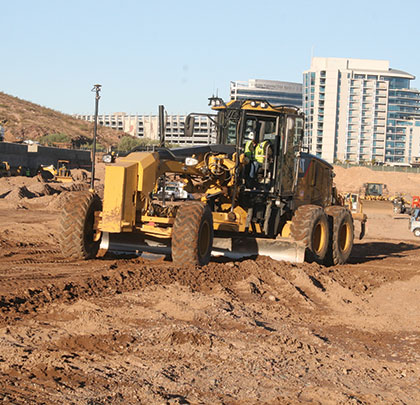