Maintaining proper storage for parts and materials inventory
In part one of this series on the proper storage of parts, an explanation of the right environment and particulate contamination was detailed, along with factors of heat and humidity and bullet points on belt storage. In this final installment, the storage of electrical motors and parts needing extra care and a preventive maintenance schedule are explained.
ELECTRICAL MOTOR STORAGE
Most electric motors are designed with grease-lubricated, antifriction, rolling-element bearings. Grease is the lifeblood of these bearings because it provides a fine film of lubrication that prevents metal-to-metal contact between the rotating element and races. Bearing troubles account for 50 to 60 percent of all electric motor failures, and poor lubrication practices account for most of these bearing troubles, resulting in 80 percent of all bearings never making it to their life expectancy.
Damage to electric motor bearings can occur while a motor is in storage due to static corrosion from:
Inadequate rust and corrosion inhibitors to protect the metal surfaces.
Motor vibration that forces out the grease from between the rollers and raceways in the load zone, which also leads to rust formation on the metal surfaces.
The other storage related damage is false brinelling. Vibration of the bearing in a static position (non-rotating) causes the rolling elements to vibrate against the raceway in one place. Over time, the vibration can remove miniscule pieces or particles of metal surfaces. This vibration-induced metal extraction can continue until the wear becomes severe. This is evident when wear marks line up with the spacing of the rolling elements.
To prevent these other types of damage, you should adhere tags to the motors that state “Grease during installation,” but otherwise, initial greasing is good for 12-month storage. Also, fully grease rebuilt motors or removals arriving into storage and purge motors of dried grease plugs that have been idle for years.
In all greasing scenarios it important to ensure the grease gun contains the appropriate lubricant. Do not use EP grease. Clean the areas around the relief and fill fittings and remove the grease relief valve or drain plug (grease outlet plug) at bottom of motor.
Grease the bearing with a calculated amount of grease. Slowly add grease (10-12 seconds for each stroke) to minimize excessive pressure buildup in the grease cavity. Keep in mind that the standard manual grease gun can produce pressures up to 15,000 psi while most seals can pop at 500 psi.
After excessive grease has been purged, reinstall the drain plug and clean excessive grease from the relief port area and wipe the grease fitting.
Avoid excess greasing, which can lead to cavity overfill, resulting in surplus grease buildup between the shaft, the inner bearing cap, and inside of the motor, which can cause both winding insulation and bearing failures.
Tag the stored motor with the date of last lubrication and the lubricant type. Store motors in a clean, dry, vibration-free area.
Use pieces of used conveyor belting as isolation padding between the motor and a wood skid or floor. This serves to insulate the motor from the effects of vibration and harmonics from fork lifts and other sources of floor vibration.
Rotate idle motor shafts every other month or quarterly to redistribute grease and maintain a corrosion-preventive film on bearing surfaces and prevent false brinelling. A Preventive Maintenance (PM) can be generated from the CMMS to trigger this activity.
During installation, align equipment and motor shafts carefully to obtain longest bearing life. Label the proper lube type near the lube point to minimize mistaken lubrication.
Other parts that need extra care and a scheduled PM program during storage are listed below:
Pneumatic valves. Large pneumatic valves should be cycled at least quarterly to prevent damage to the seals and valve seating surfaces
Rubber Components. V-belts, cog belts, gaskets containing rubber compounds, and O-rings have shelf lives. Belts should be managed by the date received, first-in-first-out. Belt replacement on operating equipment should be a scheduled PM activity. A proactive maintenance organization will kit these items when possible and order the belts in as needed and keep a small number of belts for critical applications.
Electronic drive boards and components. It is a good idea to store electronic drive boards and electronic components in an environmentally controlled space when possible. Drive boards can be damaged by exposure to extreme environmental conditions such as dust, static, extreme heat, and humidity. Drive boards should be stored in the appropriate static bags and anytime the board is removed from the static bag a new bag should be used if it is put back on the shelf.
Gearboxes and pumps should be under a scheduled PM program that includes lubrication and exercising of the bearings to prevent brinelling and static corrosion. These components should also be stored on vibration dampening pads and large gearboxes blocked to prevent damage to the bearing and raceway. Gearboxes and pumps should be under a 90-day PM program schedule.
Pneumatic and hydraulic cylinders should be under a scheduled PM program with the openings capped to prevent contamination. Large pneumatic and hydraulic cylinders should be stored in a vertical position to prevent damage to the actuator seal during storage. Cylinders should be stored with the base down and the actuator in the up position. With cylinders stored in this position it will be necessary to secure them in position to prevent falling causing injury or damage to the cylinder.
INVENTORY SHELF-LIFE
Establishing a spare parts management policy of first-in-first-out (FIFO) ensures the oldest parts are used first. Include a date received on the inventory tag or physically write a date on the packaging to ensure the person picking the items can pull the items by received date.
The use of high density storage cabinets provides additional protection from dust and exposure to UV lights that can accelerate the degradation of many of the parts stored in the MRO storeroom inventory. Component manufacturers and OEMs typically publish their recommend storage procedures. Be sure you know and follow those.
About the authors:
Preston Ingalls consults with construction industry fleets on equipment costs and uptime improvements. He can be reached at www.tbr-strategies.com.
Wally Wilson is a senior subject matter expert with Life Cycle Engineering and specializes in materials management. He can be reached at www.lce.com.
Modern Contractor Solutions, February 2019
Did you enjoy this article?
Subscribe to the FREE Digital Edition of Modern Contractor Solutions magazine.
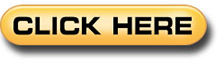