Even the best oil filter is of no use if the gasket/O-ring seal is brittle. And, if you manage a lot oil filters, hydraulic cylinders, and other parts, you need a way to keep these clean, dry, and in good working condition.
The role of the storeroom is to get the right parts at the right price, at the right time, and in the right condition. For this series on Maintenance Repair and Operational Supplies (MRO), we will examine the importance of the right condition.
STORAGE ENVIRONMENT
A storeroom that is maintained at a constant temperature and humidity provides an excellent environment for storage of MRO parts and provides a favorable work space for the storeroom staff. But maximizing lifespan and reliability requires a little planning and preparation.
Components cannot speak for themselves. We are their champions. After all, parts don’t have a red light indicator or sensor showing when they have become defective or contaminated from the environment, but after installation the red lights will glare. Therefore, preservation of sound storage conditions is a responsibility of the shop or fleet manager who oversees the parts room or warehouse.
The challenges of environmental control maintenance for parts rooms or warehouses can be overcome with PM service tasks triggered on time intervals in a computerized maintenance management system (CMMS). But this requires identification of contaminations sources such as dust (small abrasive particles), heat, humidity, improper handling, leakage, etc.
PARTICULATE CONTAMINATION
Dust particles can range from 5 to 500 microns with atmospheric dust averaging 30 microns in size. Contrast that with a particle of sand at 100 microns and the period at the end of this sentence at 600 microns. However, most gearbox and hydraulic system damage comes from particles in the 2 to 20 micron range, which is the size of lead dust and vehicle combustion-related particles. The human eye can only detect down to 40 microns (a speck of ginger), which makes many contaminate sources undetectable with the naked eye.
A storeroom located next to the shop facility will be exposed to numerous sources of airborne particulate contamination and these will find their way onto the parts and materials stored in this location. Walling off vertical space or relocating storage far from the repair facility can provide some level of environmental control for contamination-sensitive components. Periodic dusting and dust removal as well as strategic placement of air purifiers with HEPA filters are potential solutions, but isolation and environmental control are recommended for contamination-sensitive components. HEPA-filtered air can also be used to positively pressurize the room to prevent contaminates from entering.
HEAT AND HUMIDITY
Both heat and humidity accelerate the deterioration of certain parts and materials. To reduce degradation, most items should be kept at a temperature of less than 80 degrees F and a relative humidity of less than 50-60 percent. In storerooms without significant air movement and cooling, the dew point becomes a factor when humidity levels are in excess of 60 percent. The dew point is the temperature at which air is saturated with water vapor.
Although warm air holds more moisture than cold air, it’s important to realize that the humidity of the air changes only as a result of the change in temperature. When air cools it becomes more humid, even though the moisture content in the air remains the same. As warm air cools, humidity rises and eventually reaches a point of condensation buildup on various surfaces like walls or stored items, which impacts component or material reliability.
Excessive heat and cold on parts can cause:
- Drying and cracking of oil filter media leading to a potential 50 percent reduction in life expectancy.
- Similar effects on cork, rubber, or silicone seals.
- Faster battery discharge.
Using temperature-controlled environments can extend the usable lifespan of paints, solvents, catalysts, and other compounded chemicals from the normal 2 years to as many as 5 years. The solution is to apply air conditioning and humidity control with desiccants or humidifiers, as well as the use of digital humidity and temperature monitoring tools for heat and moisture sensitive items.
BELT STORAGE
Premature belt failure can often be linked to improper belt storage. By following a few
- Hanging on nails or small diameter pins as the weight of the belt could damage the tensile cord material. (If hanging is necessary, suspend the belts on a wall rack, saddle, or large diameter tubular bracket to avoid crimps and deformation.)
- Direct sunlight storage.
- Heat and humidity. (Store in a cool, dry place with environmental conditions below 80 degrees F and less than 70 percent relative humidity for potential 6-year shelf life.)
- Stacking too many layers of belts to prevent damage to bottom belts from the weight of those above.
- Hanging variable-speed belts as they are more sensitive to distortion.
- Storage adjacent to ozone-generating equipment, such as transformers and electric motors.
- The use of ties or tape to pull belt spans tightly together near the end of the belt.
- Storing belts near radiators or heaters or in the air flow from heating devices.
- Storing where they are exposed to solvents or chemicals.
- Any tension-inducing storage methods with belts in idle equipment by reducing the tension (or removal), if storage last longer than 6 months.
Look for part 2 of this series on Maintenance Repair and Operational Supplies in the next issue of MCS as electric motor storage and inventory shelf-life take center stage.
About the authors:
Preston Ingalls consults with construction industry fleets on equipment costs and uptime improvements. He can be reached at www.tbr-strategies.com.
Wally Wilson is a senior subject matter expert with on Life Cycle Engineering and specializes in materials management. He can be reached at www.lce.com.
Modern Contractor Solutions, January 2019
Did you enjoy this article?
Subscribe to the FREE Digital Edition of Modern Contractor Solutions magazine.
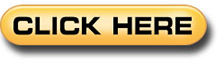