There’s nothing magical about the number 19, yet there’s a misconception that general contracting projects like framing, painting, and installing HVAC, electrical systems, or drywall require a 19-foot scissor lift. But there is more to choosing the best lift for your job than just how high it can go.
HEED THE HYDRAULICS
Heavier lifts aren’t the only thing that can damage floors; hydraulic systems can be a culprit, as well. Hydraulic systems that operate the lift’s steering, driving, and lifting have more routing with six to eight connection points. If these points become loose, fluid can leak and damage carpeting, which will require costly replacement. Not only that, but fluid that leaks onto hard surfaces like tile or laminate creates slip hazards. Nineteen-foot lifts feature hydraulic steering, driving, and lifting, which means there is an increased risk for damage and safety incidents, which in turn can lead to more workers’ compensation claims.
The hydraulic system on low-level lifts typically only powers them up and down, while battery power operates the driving and steering. This configuration has only two connection points, so the chance of a leak is greatly reduced. Some even feature a fully contained hydraulic system, so even if a leak occurs the fluid does not escape to damage carpeting or create hazards.
GETTING AROUND (OR UNDER)
Maneuvering between studs and walls, around tight corners or into small spaces can be challenging with a large lift. Many are no wider than 32 inches, well within the width of most doorways in commercial, industrial, and government buildings. However, those with higher stowed heights can make ducking under doorways or into elevators with drywall or framing on board nearly impossible. It also limits the range of work that can be performed them. In addition, wider lifts with wider turning radiuses might not be able to maneuver around tight corners. And, finally, there is a risk that inexperienced users could raise the lift too high and get caught or even crushed between the lift and ceiling.
Low-level scissor lifts, on the other hand, can be as narrow as 25 inches and they feature stowed heights as low as 66 inches. This provides more clearance for getting under doorways and into elevators, even with taller materials on board. And, because users can choose the right lift with the right working height for the job, the risk of users becoming crushed between the ceiling and lift is reduced.
Low-level lifts also feature platform lengths as short as 47 inches, so they can easily fit in any elevator in the United States that’s built to code. In addition, some models allow operators to turn in shorter radiuses, some as low as zero, for easier maneuverability around tight corners and into hallways or small offices without assistance from other crew members.
THE FINAL SHOW
Nineteen-foot scissor lifts might take you a little higher than low-level lifts, but when comparing what really matters on a jobsite, it goes beyond simple height capabilities.
The benefits of the thoughtful design of low-level scissor lifts aren’t just smoke and mirrors.
Whether you’re hanging drywall, installing sprinkler systems, painting or doing electrical work, your lift’s features should allow you and your employees to get all these jobs done safely and easily. With 14- to 20-foot working heights, low-level lifts are revealing that the “higher is always better” perception is the real illusion. ■
About the Author: Justin Kissinger is the marketing manager for Custom Equipment, Inc., which engineers and manufactures all-purpose Hy-Brid Lifts’ brand of scissor lifts in electric self-propelled and push-around models. Contact him at 262.644.1300 or email justin@customequipmentlifts.com. For more information, visit www.hybridlifts.com.
_________________________________________________________________________
Modern Contractor Solutions, March 2017
Did you enjoy this article?
Subscribe to the FREE Digital Edition of Modern Contractor Solutions magazine.
The Magic Number: Part 2
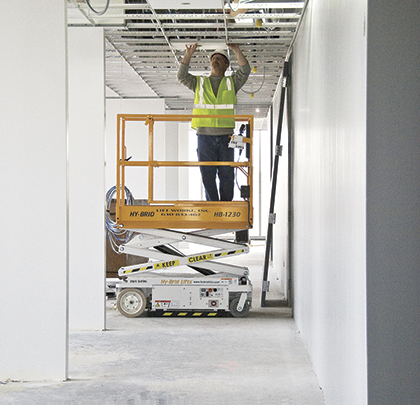