The telehandler is one of the most indispensable pieces of equipment on the jobsite, providing the ability to place palletized loads at height and the versatility to tackle other tasks with various attachments.
While telehandlers are useful, it’s important to remember they are powerful and heavy machines, and safe operation is critical. Many factors contribute to safe telehandler use, including machine design, proper training, and having enough lifting capacity for the job.
HYDRAULICS AND VISIBILITY
Today’s leading telehandlers are engineered to give the operator full confidence in the machine, whether they are a regular user of a telehandler or a rental customer in an unfamiliar unit.
It starts with the smoothness of the hydraulic controls. A good hydraulic circuit will provide an intuitive feel and eliminate jerky movements when landing loads. Single joystick, pilot operated controls that cover all boom functions help simplify lifting tasks.
Another design trend is cylinder cushioning to dampen the end of strokes—for both extending and retracting the boom—to help prevent load spilling. This also reduces machine wear-and-tear by avoiding hard, jarring stops. Users can also benefit from frame leveling, where a sway cylinder automatically levels the load on the forks as the machine travels across terrain.
Another factor is machine stability and the resulting “pants in the seat” feel that allows the operator to feel secure when pushing the telehandler to its top reach or full load capacities.
Visibility is another key component of safety. Some manufacturers will tout great visibility from the cab, only for those clear views to become diminished once the machine is put into a working condition.
The main blind spot for a telehandler operator is typically when looking back toward the curbside. In turn, the best-designed machines are optimized to have their side-mounted engines positioned to allow ample curbside visibility.
Telehandlers that utilize a single, rather than double, lift cylinder typically have better sight lines to the rear. Many machines have an extra set of slave cylinders near the pin where the boom is hinged, which can create a vision obstacle. Designs that do not require slave cylinders are more open for rear views.
Backup cameras and object detection sensors are popular, but it’s still important for the operator to see firsthand when maneuvering. Having clear sightlines around the machine makes a big difference in productivity.
OPERATOR TRAINING
Elevating loads to the height and distance telehandlers can attain requires a trained and observant operator. A unit’s combined center of gravity will constantly shift, creating a risk of overturning the machine or displacing a load when not operated in a proper and safe manner.
Today’s telehandlers trend toward simple, intuitive designs that help operators of any experience level become proficient. Nevertheless, proper training is important for everyone, from operators to account managers to service technicians, so that everybody who handles the machine has proper instruction for using and maintaining it. Dealers and manufacturers can assist with detailed training and operator certification.
SAFE LOAD LANDING
Certain styles of telehandlers can prove more advantageous than others. Long-time users of popular Lull telehandlers are familiar with the horizontal traversing boom concept, a feature now only offered to the market on Pettibone Traverse telehandlers.
Unlike a traditional fixed boom telehandler, the tower portion to which the boom is attached slides forward on a Traverse model. The traversing carriage is mounted to the chassis with a series of slide pads and pulled forward or back with a hydraulic cylinder.
With this traversing capability, an operator can simply and safely place a load on the target landing, release the contact of the forks, and traverse the carriage backward to disengage the forks. With a fixed boom, the operator must coordinate several motions of the controls to withdraw the forks from the payload, leading to intermittent contact with the load or landing.
The practical result of this is that a traditional machine actually loses about three feet of its specified lift height, whereas a traversing machine is capable of landing a load at the telehandler’s maximum lift height.
Additionally, a traversing unit does not need to physically drive back and forth during the landing process. Because the boom itself slides to place the load, the machine can be driven into its desired position and remain there, helping to avoid potential hazards on uneven terrain.
Having the proper size telehandler is another critical factor. Consider the application and consult the machine’s lift chart to ensure there is ample capacity to safely handle anticipated loads as the boom extends farther up and out.
A 9,000-pound-capacity telehandler with 44-foot lift height is capable of tackling numerous jobs; however, when working at increased heights or operating from a street-side position, a 12,000-pound machine and/or a higher-reaching 56-foot unit may be necessary to accommodate the de-rating of the boom as it extends out with a load.
The better maintained a telehandler is, the easier to operate it safely. Perform simple daily checks. Make sure wear pads are in the correct spec to ensure smooth boom travel. Check hydraulic hoses for leaks. Maximize your investment and ensure it’s always safe to use.
Telematics has emerged as a key technology for telehandlers. With real-time access to the status of a telematics-equipped telehandler, potential issues can be detected and avoided.
CLOSING THOUGHT
Elevating loads to the height and distance that telehandlers can attain requires an observant operator and a machine in proper operating condition. Follow the manufacturer’s safe operating guidelines to ensure productivity and safety for all involved.
About the Author:
Mitch Fedie is product manager for Pettibone/Traverse Lift, LLC. Pettibone has been a leading provider of material handling equipment since revolutionizing the industry with the first forward-reaching, rough-terrain machines in the 1940s. For more, visit www.gopettibone.com.
Modern Contractor Solutions, December 2022
Did you enjoy this article?
Subscribe to the FREE Digital Edition of Modern Contractor Solutions magazine.
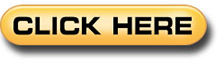