The construction industry is easily one of the country’s riskiest. Approximately 20% of worker deaths in the U.S. occur in the construction field, even though construction workers make up just 6% of the country’s labor force.
Construction site injuries aren’t only harmful to the workers who get hurt on the job. They also affect the entire company. The Workplace Safety and Insurance Board estimates that the average cost of a one-time construction site injury is $35,000.
To avoid the short- and long-term consequences of construction site injuries, it’s vital that employers prioritize regular and comprehensive safety training.
Some of the most significant benefits of safety training are discussed below, along with tips on creating a more effective safety program.
COMMON SAFETY HAZARDS
Construction sites, especially busy commercial construction sites, have many moving parts, making it easy for accidents and injuries to occur. The following are some of the most common safety hazards construction workers regularly face:
- Working at great heights (increasing the risk of injury or death after a fall)
- Moving heavy objects (increasing the risk of lifting and crushing injuries)
- Slips, trips, and falls (which can cause sprains, fractures, and other bodily injuries)
- Noise exposure (which can damage hearing and affect balance)
- Exposure to harmful chemicals (including asbestos, lead, and carbon monoxide)
- Exposure to electrical equipment (increasing the risk of electric shock-related injuries)
REGULAR TRAINING BENEFITS
Thorough and consistent safety training can reduce the risk of several accidents and injuries, including those listed above. The following are some additional benefits of regular safety training for construction workers:
Increased Productivity: Some employers may be wary of increasing their safety training efforts because they worry about wasting time or delaying projects. It’s important to remember, though, that a safe construction site is a productive one. When safety isn’t a priority, accidents and injuries are more likely to occur. When these situations happen, the entire site may have to shut down for hours, days, or weeks to assess the cause of the accident and mitigate the damage.
Better Employee Retention Rates: Construction crew members are more likely to stay with an employer if they feel that employer has their best interests in mind. If they know their employer values their safety and wants to make sure they’re taken care of on the jobsite, their loyalty will increase. As a result, employers will have to worry less about the time and money required to recruit and train new team members.
Increased Savings: Recruiting and training aren’t the only aspects of running a business that cost money. On-the-job accidents and injuries are also expensive. They can result in significant costs for employers, from legal fees to lost productivity. For those who value long-term savings and profitability, it’s best to focus on safety by offering thorough and ongoing training.
Better Public Reputation: Providing regular safety training can also improve an organization’s public reputation. Word travels fast. If one employer is known for frequent injuries on the job, they may have a more challenging time recruiting workers. Potential clients may also be wary of hiring a particular company if they know there’s a greater possibility of accidents happening on their business’s property.
SAFETY PROGRAM ELEMENTS
It’s clear that a commitment to safety matters in the construction field. What constitutes a good safety program, though? Industry experts agree that the following elements contribute to a more effective and beneficial safety program:
Management Buy-In: For a safety program to genuinely benefit employees, management and other leaders must buy into it and its importance. If higher-ups don’t care about safety and allow employees to cut corners (or even encourage it), on-site injury rates are unlikely to budge (and may even get worse). Those who want a greater emphasis on safety should share the benefits of regular safety training with the company’s managers and leaders. After getting top-down support, it’ll be easier to implement the program and enforce its rules.
Employee Involvement: Along with managers and higher-ups, it’s also vital that employees on all levels are involved in the company’s safety program and safety training. Employees should play an active role in lessons. Assessments or hands-on exams may help to increase motivation and engagement while also increasing knowledge retention, too. Leaders should also encourage employees to provide feedback (and implement that feedback when possible). The people who work on the jobsite each day have the greatest insight into the safety challenges and what can be done to correct them.
Worksite Analysis: Regular worksite analyses can help employers to understand how safe their jobsites currently are and where they can make improvements for increased safety. For example, after a worksite analysis, they might learn that they need to provide easier access to first aid kits and other supplies. They may also find that certain employees aren’t following specific safety protocols. Worksite reviews should be conducted by a construction consultant who is familiar with the industry, its safety guidelines, and the most significant risks employees face.
Hazard Control and Prevention: Employers might not be able to eliminate construction site dangers completely. However, they can reduce injury and accident risk with proper hazard control. For example, a manager might set rules stating where equipment should be stored at the end of the workday, how it should be used, and who has permission to use it. They can also ensure hazardous chemicals are properly stored so workers aren’t accidentally exposed to them.
Ongoing Instruction: Ongoing instruction helps to improve the retention of training information. How do employers make sure they prioritize ongoing instruction even during the busiest seasons? Implement a training schedule. Planning training days in advance saves employers from scrambling to put together a lesson at the last minute. Employees will also get regular updates and access to the latest safety information.
CLOSING THOUGHT
When construction workers participate in regular safety training programs, they’re better equipped to handle the stressors and risks of their jobs. Employers benefit, too, through increased productivity, better retention rates, and an improved public reputation.
About the Author:
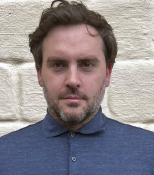
Steven John Cumper, B.App.Sc. (Osteo.), M.Ost., is a businessman with a strong background in biomedical science and osteopathic medicine. He founded Medshop while studying at RMIT University in Australia, expanding its reach to markets in Papua New Guinea, Singapore, and Malaysia. In September 2021, the Bunzl Group acquired a majority stake in Medshop, but Cumper remains involved as the Managing Director (Medshop Group). His journey from Zimbabwe to the UK and Australia reflects his dedication to academia and entrepreneurship, combining diverse knowledge and experience. For more, visit www.medshop.com.au.
Modern Contractor Solutions, July 2023
Did you enjoy this article?
Subscribe to the FREE Digital Edition of Modern Contractor Solutions magazine.
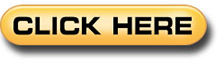