When a January 2012 landslide along a major Washington highway caused closures and damage to residential properties, the city of Bellevue needed a fast solution that would stabilize the slope and get traffic moving again.
West Lake Sammamish Parkway runs along a hill above Lake Sammamish, and several high-end residences lie between the highway and the lake. Officials were unable to determine what caused a water main break during a heavy rain and ice event, which resulted in a significant landslide.
“It basically washed the whole bank down into the houses and out on the beach. We spent about 2 weeks with a vacuum truck cleaning all the dirt and debris out of people’s backyards. It was kind of an environmental disaster,” says Torger Erickson, PE and project manager for TetraTech.
Featured Image: West Lake Sammamish Parkway was closed due to a landslide and broken water main after heavy rains saturated the surrounding terrain.
Above: City officials and engineers contacted a local Redi-Rock manufacturer within 48 hours for a quick repair to get the major highway traffic flowing.
THE SOLUTION
Prior to the slide, the city of Bellevue had been considering Redi-Rock as an option for three to four phases of planned improvements along the highway. When the slide happened, engineers and city officials contacted local Redi-Rock manufacturer, Puget Sound Precast, within 48 hours because “repairing the slope needed to happen quickly; these blocks solved the engineering problem; they had the aesthetics the homeowners wanted, and they were easy to install,” says Erickson.
“We didn’t have soil conditions that would allow us to drill tiebacks or lay geogrid. Other types of retaining walls higher than 6 feet require tie backs, but we were able to achieve a 12 foot tall wall by utilizing the weight of these blocks,” explains Bill Cross, senior construction inspector for the city.
The project actually required two walls: the lower wall was 9 feet tall with 3 feet of freestanding walls on top, and the upper wall was 12 feet tall. Both were built as gravity structures, which rely on the massive size of each block to create tall walls that require no reinforcement at all. Engineers designed the lower wall using Redi-Rock 41-inch gravity blocks in the bottom courses, 28-inch blocks in the middle courses, and freestanding blocks on top. The lower wall also included a 24-inch pipe at the base of the lower wall which allowed a stream to flow under the highway.
The project actually required two walls: the lower wall was 9 feet tall with 3 feet of freestanding walls on top, and the upper wall was 12 feet tall.
“We needed to avoid seepage around the pipe so we used cork sheets to make a tight seal and also allow for the retaining wall to move a bit without crushing the pipe,” says Erickson. To help the pipe blend with the wall, Puget Sound Precast manufactured custom Ledgestone faces, which were attached to the concrete after the wall was installed.
The design of the upper wall called for Redi-Rock 60-inch base blocks in the bottom 6 courses (9 feet) of the wall to increase its stability, topped with one course of 41-inch middle blocks and one course of 28-inch top blocks. “We were holding back a lot of soil. This was a 30-foot embankment with a highway on top that we were holding back with a 12 foot high wall, so that’s a lot of load,” Erickson adds.
Engineers specified freedraining “quarry spalls” (riprap) as backfill so that water wouldn’t be held behind the walls, “so the chances of having a water problem causing a failure again are minimized,” Erickson says.
In total, the solution included two walls and 1,365 square feet of Redi-Rock blocks all in the Ledgestone texture that was stained to match the natural rock tones in the area. Because the walls are located in residential backyards, aesthetics was an important consideration for this project. The Ledgestone texture gives walls the random look of natural stone, with the structural stability of an engineered system.
“This was an innovative project. It was more complicated than just building a retaining wall,” Erickson adds. “We used this as an opportunity to improve more than just the wall. We planted above the wall with trees and ground cover and bushes.”
The solution included two walls and 1,365 square feet of Redi-Rock blocks all in the Ledgestone texture that was stained to match the natural rock tones in the area.
THE OUTCOME
“The construction was quick,” says Doug Neal of Westwater Construction Inc. “We’ve done a lot of smaller block walls, but this was the first time we worked with Redi-Rock. It was like building with Legos!”
The Westwater crew staged the blocks on the main roadway above the project and moved blocks down as they needed them. “We built the wall in two stages. The lower wall took 45 days and the upper wall took 78 days,” Neal says. He adds: “The best thing about the system is that you don’t have to lay the blocks at a batter because it’s already built in. As a contractor, that makes a huge difference. You just build a level base and then pop the blocks in.”
The road was open again 4 months after the slide occurred. Choosing Redi-Rock solved the engineering issue and allowed the City to repair the slide area as quickly as possible, plus the aesthetics kept the homeowners happy. ■
About the Author: For more information about using Redi-Rock on your next project, visit www.redi-rock.com.
_________________________________________________________________________
Modern Contractor Solutions – February 2016
Did you enjoy this article?
Subscribe to the FREE Digital Edition of Modern Contractor Solutions magazine.
Landslide Causes Highway Closures
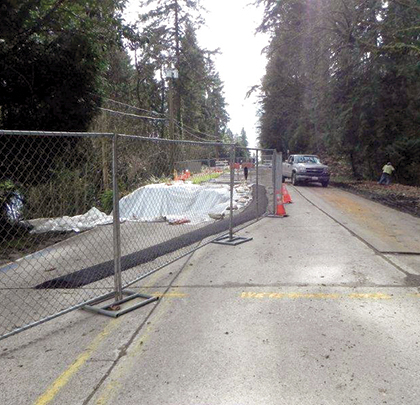