A good starting point for ensuring you have the power you need to keep things moving on the jobsite is to choose a generator with enough kilowatt output. Or you might find there’s a way to get greater dependability, cost savings, and efficiency in numbers—paralleling.
Paralleling, or connecting multiple generators to operate in parallel so they meet the same kW as a single larger unit, ensures reliable power if one goes out of service. Paralleling also allows the powering down of some units when they are not in use or the load falls below a certain level. The gensets not only provide predictable power, but also operate more efficiently, reduce fuel costs, and offer greater versatility.
BATCHES OF BENEFITS
Asphalt and aggregate plants have commonly practiced paralleling for quite some time, but it wasn’t always as easy to do as it is today. There was a time when connecting generators required numerous wires and connections, and operators needed to adjust controls manually and monitor loads frequently. Technology has evolved, and now “plug-and-play” designs allow operators to connect the units’ controls with just one cable. Afterwards, they can connect the power cables to a common bus, set a few parameters in the controller, and hit the start button. From there, the generators automatically synchronize.
Not all generators are plug-and-play. Operators will need to upgrade genset units that are not equipped to parallel with a special controller that creates a power management system (PMS) to operate all of the units. Generators with these types of controllers feature motorized breakers that, once connected, allow the units to automatically start and stop as loads fluctuate. This makes synchronization considerably faster than what older models could achieve. Some manufacturers’ models can parallel as many as 16 generators.
With asphalt and aggregate plants, dependable power is crucial. If you’re operating with just one generator and it goes down, you will face a tough situation as that asphalt cools and hardens. This not only is difficult and time-consuming to remove from the hopper, but also can cause damage. Replace that one generator with several smaller units operating in parallel and there will be little to no impact if you take one out of service. You greatly reduce risk of damage to equipment and, more importantly, there’s more uptime.
Paralleling also can reduce fuel consumption. Let’s say the plant needs 5 megawatts of power to operate numerous pieces of equipment. Paralleling five 1-megawatt generators can provide the same amount of peak power as two 2.5-megawatt generators, but they automatically power down as usage decreases or power up as it increases. The generators consume only the necessary fuel to supply the load. Also, as the load falls below certain levels on some larger generators, so does the fuel efficiency. For example, if the load requirement falls below 750 kilowatts, a 2.5-megawatt unit will be operating at 30 percent load, which is below optimal operating range. If you are using three paralleled 1-megawatt generators, however, two will automatically power down and the remaining 1-megawatt genset will be in a more efficient operating range. This can save a considerable amount of fuel.
FORM AND FUNCTION
When looking for generators to parallel at your batch plant, you’ll first need to consider many of the same criteria you would for a stand-alone unit: altitude, ambient temperature, amperage, voltage, motor starting method, and surge capacity.
It’s also important to keep in mind that generator power ratings for prime power applications, such as batch plants, are 10 percent lower than they are for standby applications. Just because a generator is new doesn’t mean it will be user-friendly. Some might need to be set up by a specialist and can require several cables for connecting units and external switchgear. This all adds up to more costs, hassle, and time. Instead, look for units with plug-and-play technology.
You’ll want to be sure accessing the control panel isn’t a hassle, either. Placing your generators on a trailer could put your control panel out of reach and require you to make several trips on and off the trailer every time you need to monitor the controls. By comparison, a movable exterior control panel gives operators flexibility, optimal ergonomic height, and eliminates the time and hassle associated with getting on and off a trailer. This also minimizes the risk of injury from falling and hearing loss from the equipment. Keep an eye out for models that have factory-designed and -installed sound attenuation, which can help reduce noise, as well.
With tough jobsite conditions, durability and longevity should be key considerations when selecting generators, too. Rather than placing them in standard ISO shipping containers, some manufacturers build them into 20-foot enclosures they design and manufacture from the ground up. This ensures the units are structurally sound and can accommodate features, such as larger openings for maintenance access and control panels on the outside, features that would otherwise weaken the integrity of standard ISO containers. Instead, custom-designed and -manufactured enclosures are safer and easier to use; they maintain the same footprint and form factor of ISO containers.
If you’ll be operating in cold weather, look for optional features, such as coolant heaters, battery chargers, heavy-duty batteries, and synthetic 0W-40 engine crankcase oil, which maintain the appropriate viscosity in colder temperatures.
SMOOTH OPERATOR
For consistent, predictable power to keep your jobsite up and running smoothly, paralleling is one of the best ways to get it. Now that’s smart power. ■
About The Author
Jim Siffring is the product manager for Atlas Copco Construction Equipment’s generator product line. He works out of Atlas Copco’s U.S. headquarters in Commerce City, Colorado. For more information, visit www.atlascopco.com.
Modern Contractor Solutions, December 2014
Did you enjoy this article?
Subscribe to the FREE Digital Edition of Modern Contractor Solutions Magazine!
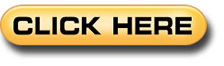